Sand casting is one of the oldest and most versatile metal casting processes, particularly popular in the manufacturing of steel components. This technique utilizes sand as the primary mold material, enabling the production of intricate shapes and structures with varying dimensions. The simplicity of the sand casting process, combined with its cost-effectiveness, makes it an ideal choice for both small and large quantities of steel components.
The sand casting process begins with the creation of a pattern, which is typically made from wood, metal, or plastic. This pattern is an accurate representation of the final part, including all necessary details. Once the pattern is ready, it is pressed into fine, dry sand mixed with a binder, forming a mold. The mold consists of two halves the cope and the drag. After the pattern is removed, the two halves of the mold are assembled, and gates are created to allow molten steel to flow into the cavity.
One of the primary advantages of sand casting steel is its capability to produce complex geometries that would be challenging to achieve with other methods
. The flexibility of the mold allows for features such as internal passages, intricate designs, and undercuts. This versatility caters to various industries, including automotive, aerospace, and general manufacturing, where unique part specifications are often required.Once the mold is prepared, molten steel is poured into it at a carefully controlled temperature. Iron and other alloying elements may be added to enhance the properties of the steel, such as strength, ductility, and resistance to corrosion. The choice of alloying elements significantly impacts the final product characteristics, making it crucial to adhere to specific formulations.
sand casting steel
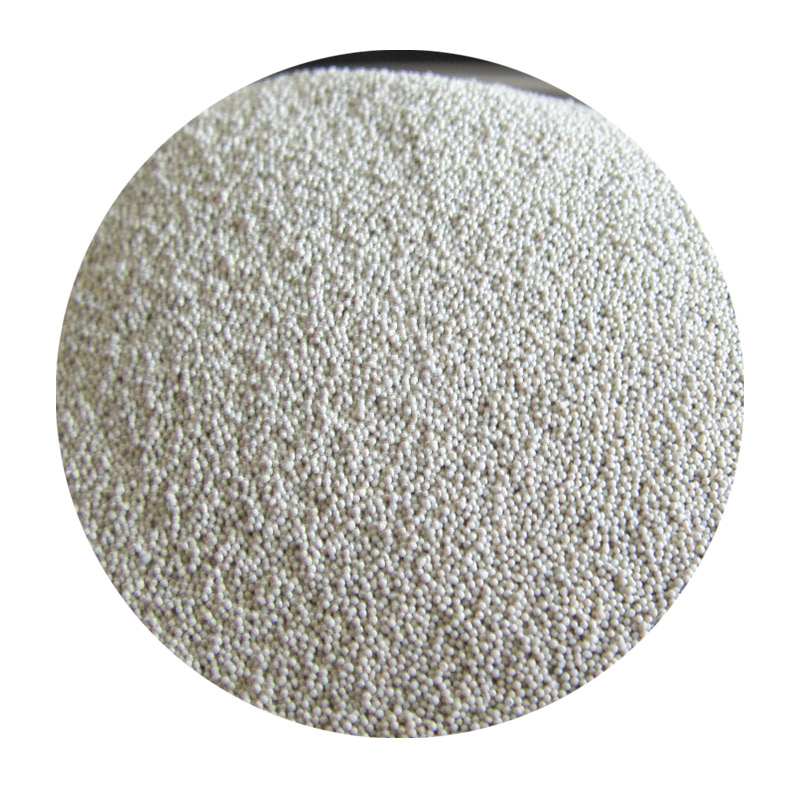
After the molten steel solidifies, the mold is broken away to reveal the cast component. This step may require additional processing, such as trimming, grinding, or machining, to meet precise tolerances and surface finish requirements. Further heat treatment processes are often employed to improve mechanical properties like hardness and toughness, tailoring the steel for its intended application.
Despite its many advantages, sand casting does have some limitations. Key challenges include the potential for defects like sand inclusions, porosity, and dimensional inaccuracies. These issues necessitate rigorous quality control measures throughout the casting process to ensure that the final products meet the desired standards.
In conclusion, sand casting is a crucial method for producing steel components, combining simplicity and versatility in manufacturing. Its ability to create complex shapes at relatively low costs, along with the capacity to adapt steel properties through alloying, makes it an enduring choice in various industries. As technology continues to evolve, advancements in sand casting techniques and materials will likely enhance its efficiency and expand its applications, solidifying its place in modern manufacturing processes.
Post time:Лис . 02, 2024 08:15
Next:sand casting foundry process