Lost Foam Casting Method An Overview
The lost foam casting (LFC) method is an innovative and efficient manufacturing process that has gained significant popularity in recent years, especially in the production of complex metal parts. This technique combines traditional casting methods with the use of foam patterns, allowing for greater design flexibility and enhanced surface finish. Understanding the lost foam casting method involves exploring its process, benefits, applications, and challenges.
At its core, the lost foam casting technique utilizes expanded polystyrene (EPS) foam patterns, which are shaped into the desired component. These foam patterns are then coated with a refractory material to create a mold. After the coating has dried, the foam is placed in a sand mold, where molten metal is poured into the cavity created by the foam. The key aspect of this method is that the foam pattern evaporates upon contact with the molten metal, thus leaving behind a precise metal part that mirrors the original foam shape. This “lost” foam process eliminates the need for traditional core-making, making it a highly efficient casting technique.
One of the primary advantages of lost foam casting is its ability to produce intricate and complex shapes with high precision. Since the foam patterns can be easily molded and shaped, manufacturers can create designs that might be difficult or impossible to achieve with conventional casting methods. Additionally, the foam evaporates without leaving any ash or residue, resulting in minimal cleanup and a superior surface finish on the final product.
lost foam casting method
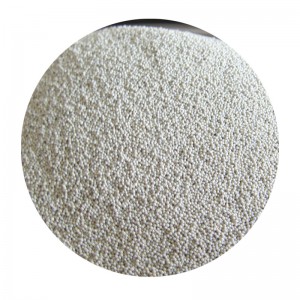
Another significant benefit of the lost foam casting method is its cost-effectiveness. The process allows for rapid prototyping and reduced production times, leading to lower labor costs and efficient material usage. Furthermore, the elimination of traditional molds can lead to significant savings in tooling costs, making it an attractive option for small to medium production runs.
Lost foam casting has found its niche in various industries due to its versatility. It is commonly used in the automotive sector for manufacturing engine blocks, cylinder heads, and other intricate components. The aerospace industry also benefits from this method for producing lightweight and complex parts that require high strength-to-weight ratios. Additionally, the method has applications in the production of artistic sculptures and custom machinery components, showcasing its broad potential.
Despite its many advantages, the lost foam casting method does come with certain challenges. One of the main issues is the potential for gas defects, as the foam's rapid evaporation can create gases that may become trapped in the molten metal. Proper control of pouring temperatures and techniques is essential to mitigate this risk. Additionally, the requirement for precise and consistent foam patterns necessitates advanced manufacturing capabilities, which can be a barrier for some smaller foundries.
In conclusion, the lost foam casting method represents a significant advancement in the field of metal casting, offering manufacturers a combination of flexibility, efficiency, and cost savings. As technology progresses and industries continue to seek innovative solutions for production challenges, the adoption of lost foam casting is likely to increase. Whether in automotive, aerospace, or artistic applications, this method holds the promise of revolutionizing the way complex metal parts are designed and produced.
Post time:Лис . 02, 2024 06:55
Next:3d print sand