Lost Foam Casting An Overview with Examples
Lost foam casting (LFC) is an innovative metal casting process that combines the advantages of traditional sand casting and investment casting, providing unique solutions for complex geometries. This method allows for the production of near-net-shape parts with exceptional surface finishes and dimensional accuracy. In this article, we will explore the lost foam casting process, its benefits, applications, and provide some notable examples to illustrate its effectiveness.
The Lost Foam Casting Process
The lost foam casting process begins with the creation of a foam pattern, typically made from polystyrene. This pattern is designed to replicate the final part's shape and features. The foam pattern is coated with a thin layer of refractory material—usually a mixture of sand and binding agents—to form a mold around it. Once the mold is prepared, the foam pattern is subjected to heat, which causes it to vaporize and leave a void where the foam once existed.
Next, molten metal is poured into the mold. As the metal fills the cavity, it displaces the vaporized foam, which prevents any inclusions or defects from forming during the metal’s solidification. After the metal cools and solidifies, the mold is broken away, revealing the finished part.
Advantages of Lost Foam Casting
Lost foam casting offers several advantages over traditional casting methods
1. Complex Geometries LFC allows for the production of intricate geometries that would be difficult or impossible to achieve with traditional casting techniques. This flexibility is particularly beneficial in the aerospace and automotive industries, where components often have complex shapes.
2. Reduced Waste Since the foam pattern is completely vaporized, there is minimal material waste. This makes LFC an environmentally friendly option compared to methods that involve reusable patterns.
lost foam casting examples
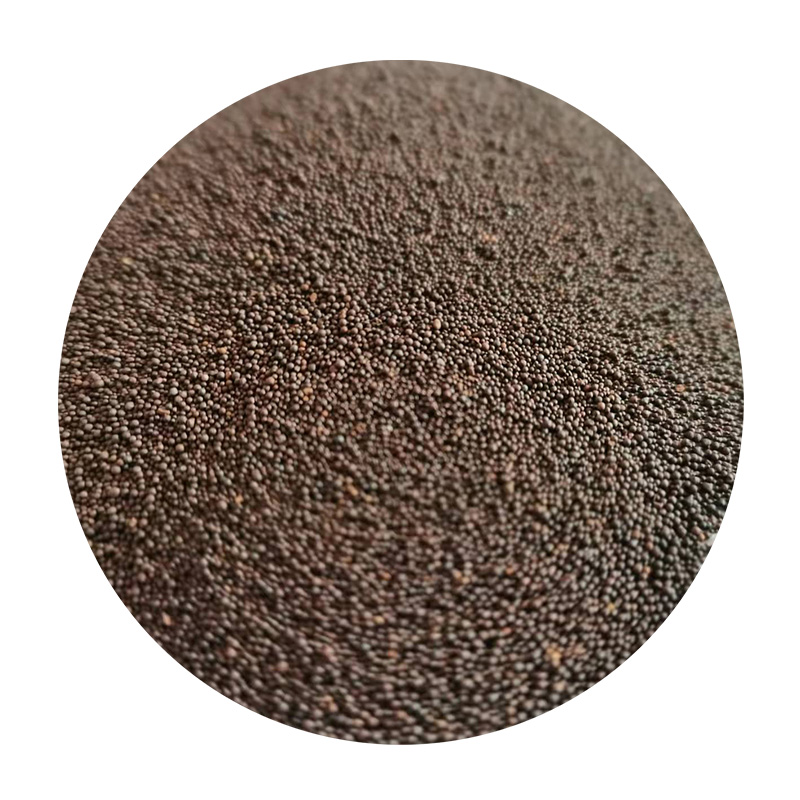
4. Enhanced Surface Finish The process typically yields superior surface finishes compared to sand casting, which can reduce the need for additional finishing processes.
Applications of Lost Foam Casting
Lost foam casting is widely used in various industries, including automotive, aerospace, and general manufacturing. It is particularly advantageous for producing components like engine blocks, turbine housings, and complex automotive parts.
For instance, in the automotive sector, manufacturers have used LFC to create lightweight yet strong components that help improve fuel efficiency. The ability to produce intricate shapes allows for designs that can integrate multiple functions, reducing the number of parts in a vehicle and thus lowering assembly costs.
Notable Examples
1. Aerospace Engine Components Companies in the aerospace industry often employ lost foam casting to produce components like compressor cases and turbine blades. The precision and ability to handle complex designs enable the production of parts that meet stringent performance and weight requirements.
2. Automotive Parts Some automotive manufacturers have successfully implemented lost foam casting for producing intake manifolds and other engine components. The process allows them to create lightweight structures that contribute to overall vehicle efficiency.
3. Artistic and Sculptural Castings In addition to industrial applications, lost foam casting has found a niche in the art world. Artists use the technique to create detailed sculptures and fabric representations, benefiting from the method’s ability to capture fine details and textures.
Conclusion
Lost foam casting represents a significant advancement in metal casting technology, offering numerous benefits such as reduced waste, cost-effectiveness, and the ability to produce complex geometries. Its versatility in various industries, from automotive to aerospace, showcases its potential as a go-to method for modern manufacturing. By continuing to refine and adopt lost foam casting techniques, industries can create innovative products that meet the demands of today’s market while minimizing environmental impact. As technology evolves, we can expect to see even broader applications and improvements in this fascinating casting method.
Post time:Лис . 08, 2024 12:26
Next:Exploring the Beauty and Versatility of Golden Sands Concrete in Modern Construction