The Process and Benefits of Large Sand Casting
Sand casting is one of the oldest and most widely used metal forming processes, known for its versatility and cost-effectiveness. Among its various applications, large sand casting stands out for its ability to produce substantial metal components that play crucial roles in industries such as aerospace, automotive, construction, and marine manufacturing. This article explores the process of large sand casting, its benefits, and its significance in modern manufacturing.
Understanding Large Sand Casting
Large sand casting involves creating molds from a mixture of sand, water, and a binding agent to shape molten metal as it cools. The primary steps involved in the sand casting process include pattern making, mold preparation, pouring, and finishing.
1. Pattern Making This is the initial step where a replica (pattern) of the final part is created, usually from materials like wood, plastic, or metal. The pattern is designed slightly larger than the final component to account for shrinkage that occurs during metal cooling.
2. Mold Preparation The sand mixture, often called green sand, is compacted around the pattern to create a mold. Large sand castings require strong and stable molds to withstand the weight of the molten metal. Cores can be added to create internal cavities or complex geometries.
3. Pouring Once the mold halves are prepared and assembled, molten metal is poured into the cavity. The temperature and properties of the molten metal must be carefully controlled to ensure high-quality castings.
4. Cooling and Removal After pouring, the metal must cool and solidify, which can take several hours or longer, depending on the thickness of the casting. Once cooled, the mold is broken away, revealing the rough casting.
5. Finishing The final step involves removing any excess material, such as gates and risers, and applying surface treatments to achieve the desired finish and mechanical properties.
Benefits of Large Sand Casting
The advantages of large sand casting make it an attractive choice for many manufacturers
large sand casting
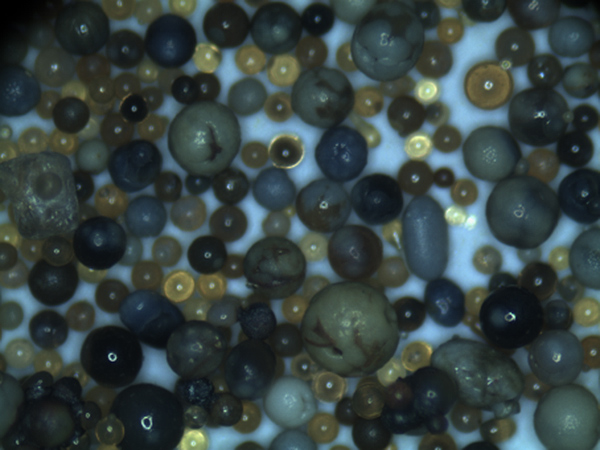
1. Cost-Effectiveness Large sand casting offers significant cost savings, especially for low to medium production volumes. The materials used (primarily sand) are inexpensive, and once the molds are created, the process can be repeated with minimal additional costs.
2. Design Flexibility Sand casting can accommodate complex shapes and designs that may be challenging for other manufacturing processes. Designers have the freedom to create parts with intricate details, and the process can easily be adapted for design changes.
3. Material Variety A wide range of metals can be utilized in large sand casting, including ferrous and non-ferrous alloys. This versatility allows manufacturers to select materials that best meet their specific mechanical and chemical requirements.
4. Large Component Production Perhaps the most prominent benefit of large sand casting is its ability to produce large components. This capability is essential for sectors that require sizeable, heavy parts, such as engine blocks, turbine housings, and industrial fittings.
5. Short Lead Times With modern advancements in pattern-making techniques, such as 3D printing and CNC machining, the time required to produce patterns and molds has been significantly reduced. This improvement results in shorter lead times for casting production.
6. Excellent Surface Finish and Mechanical Properties Although sand castings can have surface roughness, additional machining processes can be incorporated to improve the surface finish. Moreover, properly controlled cooling rates can enhance the mechanical properties of the cast parts.
Applications in Various Industries
Large sand casting is utilized across diverse industries, each benefiting from its unique properties. In aerospace, precision sand casting produces critical engine components. The automotive industry relies on sand casting for engine blocks, transmission cases, and other vital parts. In construction, large sand castings are essential for producing heavy equipment and machinery parts. The marine industry utilizes this process for making components that must withstand harsh conditions and corrosive environments.
Conclusion
In conclusion, large sand casting is a vital manufacturing process that combines cost-effectiveness, flexibility, and the capacity to produce large components. As industries continue to evolve and demand increasingly complex designs, large sand casting will undoubtedly remain a cornerstone of metal casting technology, adapting to meet the needs of modern manufacturing. Its continued relevance highlights its significance within a broad spectrum of applications, ensuring that it remains a preferred choice for producing high-quality metal components.
Post time:Жов . 13, 2024 10:10
Next:Sandgussverfahren und seine Anwendungen in der modernen Industrie und Kunst