Understanding Foundry Casting Sand Key to Effective Metal Casting
Foundry casting sand is an essential material used in the metal casting process, which has a rich history dating back thousands of years. The sand is pivotal in creating molds that are necessary for shaping molten metal into various forms. While many modern materials have emerged in manufacturing, casting sand remains a favored choice due to its unique properties and versatility. In this article, we will explore the types, characteristics, and applications of foundry casting sand, emphasizing its critical role in the metal casting industry.
Types of Foundry Casting Sand
There are several different types of sands used in foundry casting, each with its specific attributes and applications. The most commonly used type is silica sand, primarily composed of silicon dioxide. It is valued for its excellent thermal stability and ability to withstand high temperatures, making it ideal for most casting processes. Another variant is chromite sand, which is known for its high resistance to thermal shock and is particularly useful for casting steel and iron.
Green sand is another popular type of foundry sand. Composed of silica sand, clay, and water, green sand is pliable and can easily hold its shape, allowing for intricate designs and patterns in molds. This type of sand is often used in ferrous casting because of its cost-effectiveness and ability to produce high-quality castings. Additionally, there are resin-bonded sands, which use synthetic resins as a binder instead of clay. These sands offer enhanced strength and a smooth surface finish, making them suitable for precision castings.
Properties of Foundry Casting Sand
The effectiveness of casting sand depends on several key properties. One of the most important characteristics is grain size, which affects the surface finish of the casting. Finer grains tend to produce smoother finishes, while coarser sands result in rougher surfaces. The shape of the sand grains plays a crucial role as well; angular grains provide better strength and compactness, while rounded grains allow for easier flow and less friction during metal pouring.
Another critical attribute is permeability. The casting sand must allow gases generated during the pouring process to escape, which prevents defects such as blowholes in the final casting. Additionally, thermal conductivity is vital; casting sand should effectively conduct heat away from the molten metal to ensure uniform cooling and solidification.
foundry casting sand
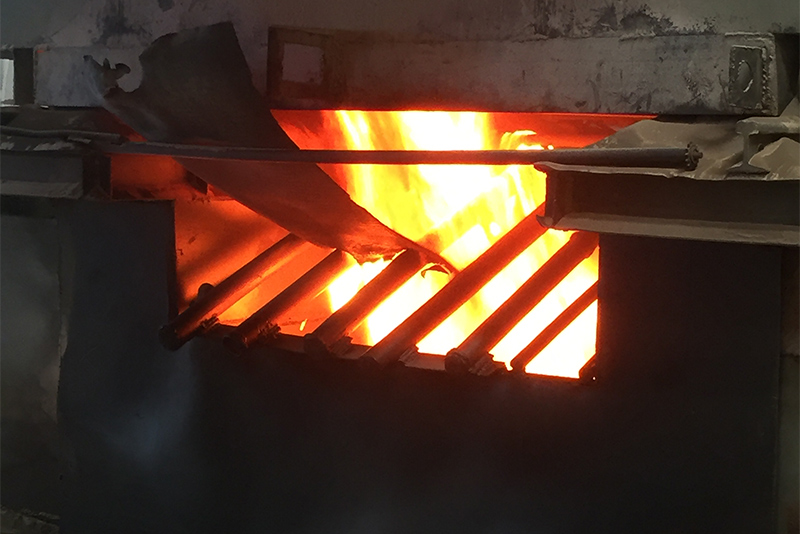
Applications of Foundry Casting Sand
Foundry casting sand is utilized in various applications across different industries. In the automotive industry, it is used to produce engine blocks, cylinder heads, and other critical components. The aerospace sector also relies heavily on casting sand for manufacturing complex components needing precise tolerances and lightweight properties. Beyond these industries, foundry sand is found in machinery parts, oil and gas equipment, and even art sculptures.
The versatility of foundry casting sand also extends to modern 3D printing applications. With the advent of additive manufacturing, sand is used to create molds and cores swiftly, enabling rapid prototyping and reducing the lead time significantly.
Environmental Considerations
As the metal casting industry faces increasing scrutiny regarding environmental impact, the recycling and proper management of foundry sand have gained prominence. Many foundries have adopted methods to reclaim sand after use, thereby minimizing waste and reducing the need for virgin materials. Additionally, research into sustainable alternatives to traditional sands is ongoing, with aims to decrease the ecological footprint of foundry operations.
Conclusion
Foundry casting sand plays a vital role in the metal casting process, providing the necessary properties for producing high-quality castings. With its diverse types and characteristics tailored to meet various industry needs, casting sand remains a linchpin in manufacturing. Understanding this material's properties can help foundries optimize their processes, improve casting quality, and reduce environmental impact, ensuring the industry's longevity in a rapidly evolving landscape. As technology advances and sustainability becomes a priority, the future of foundry casting sand is set to become even more innovative and integral to metal casting practices.
Post time:Гру . 15, 2024 21:20
Next:resin coated sand