Advantages and Disadvantages of the Sand Casting Process
Sand casting is one of the oldest and most widely used manufacturing processes for creating metal components. The method involves creating a mold from sand and then pouring molten metal into the mold to form a desired shape. While sand casting has numerous advantages, it also possesses some disadvantages that need to be considered. This article delves into the key advantages and disadvantages of the sand casting process.
Advantages of Sand Casting
1. Cost-Effectiveness Sand casting is considered one of the most economical manufacturing processes. The materials used, primarily sand and metal, are relatively inexpensive. Furthermore, the process does not require costly specialized equipment, making it accessible for small businesses and startups.
2. Versatility This process is highly versatile, accommodating a wide range of metals, including iron, aluminum, bronze, and magnesium. It can be used to produce components of various sizes and complexities, from small intricate parts to large castings for heavy machinery.
3. Ease of Molding The sand used in this process allows for easy creation of molds. The sand can be easily shaped and compacted, which means that complex geometries can be easily achieved. This is particularly advantageous for producing custom parts.
4. Low Setup Costs Unlike other casting processes, such as investment casting or die casting, sand casting requires lower setup costs. This makes it ideal for short-run productions or when manufacturing prototypes that may be subject to design changes.
5. Excellent Surface Finish and Tolerance While not as precise as some modern machining methods, sand casting can still produce parts with acceptable surface finishes. The process can also achieve decent dimensional tolerances, which can be improved through post-processing techniques.
advantages and disadvantages of sand casting process
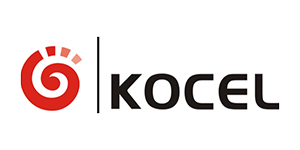
Disadvantages of Sand Casting
1. Surface Finish Quality While sand casting can produce components with acceptable surface finishes, they are often not as smooth as those obtained through other casting methods like die casting or investment casting. The rough texture may require additional machining to achieve the desired finish.
2. Dimensional Accuracy The dimensional accuracy of parts made through sand casting is generally inferior to that of precision casting methods. Variations in sand composition, moisture content, or sand compaction can lead to inconsistencies in the final product.
3. Labor-Intensive Process The sand casting process can be labor-intensive, particularly when creating molds. Although automation is available, many small operations still rely on manual processes, which can reduce efficiency and increase production time.
4. Limited Production Rate Sand casting is generally slower compared to other manufacturing processes. The time required for mold preparation, cooling, and finishing can limit the production rate, making it less suitable for high-volume production without significant investment in equipment.
5. Environmental Concerns The sand casting process can generate significant waste and environmental concerns. The disposal of used molding sand and the emission of fumes during metal pouring can have detrimental effects on the environment. Sustainable practices and improved recycling methods are necessary to mitigate these issues.
Conclusion
In conclusion, sand casting is a widely used method with distinct advantages, such as cost-effectiveness, versatility, and ease of molding. It is particularly well-suited for small to medium-scale production runs and custom parts. However, the disadvantages, including surface finish quality, dimensional accuracy, and environmental concerns, must be carefully considered by manufacturers. By understanding both the advantages and disadvantages of the sand casting process, companies can make informed decisions about its suitability for their specific applications.
Post time:Лис . 10, 2024 09:06
Next:Techniques for Wet Sanding Your 3D Prints for a Smooth Finish