Advantages and Disadvantages of Sand Casting Process
Sand casting, one of the oldest and most widely used manufacturing processes, involves the use of sand as a mold material to create metal castings. This method carries a distinct set of advantages and disadvantages that make it suitable for different applications in various industries.
Advantages of Sand Casting
One of the primary advantages of sand casting is its versatility. The process can accommodate a wide range of metal alloys, including aluminum, iron, and bronze, making it an ideal choice for diverse applications. Furthermore, it can produce complex shapes and intricate designs that would be difficult or impossible to achieve with other manufacturing techniques.
Another significant advantage is the cost-effectiveness of the sand casting process. Sand molds can be produced quickly and inexpensively, allowing for low production costs, especially for small to medium-sized batches. Additionally, the materials used in sand casting, primarily sand and binders, are readily available and cheaper compared to materials used in other casting methods.
The sand casting process also allows for significant flexibility in production schedules. Because the molds can be created on demand, manufacturers can respond to changes in orders without significant delays, making it an attractive option for custom or low-volume production.
Disadvantages of Sand Casting
advantages and disadvantages of sand casting process
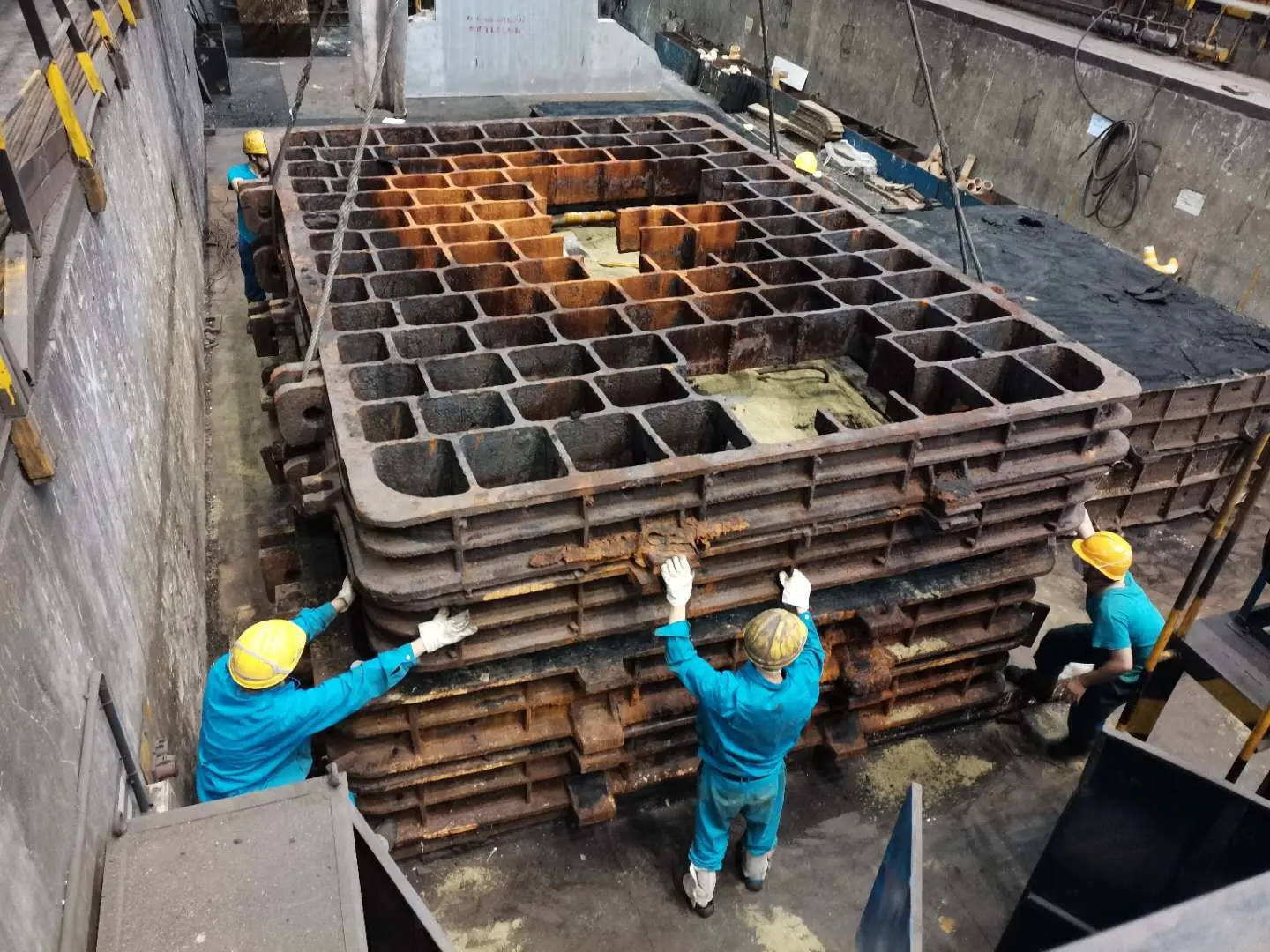
Despite its advantages, sand casting does have several drawbacks. One of the main disadvantages is the surface finish of the castings. Sand-cast parts typically have a rough surface finish, which may require additional machining processes to achieve the desired finish. This can add to the overall production time and cost.
Another challenge is the accuracy of dimensions. Sand casting is generally less precise compared to other casting methods, like investment casting or die casting. This can lead to tighter tolerances, which may not be feasible without further processing.
Additionally, sand casting can be a slow process, particularly when producing multiple castings, as each mold must be created individually. This reduced productivity can be a concern for large-scale manufacturing.
Finally, the nature of sand as a mold material limits the maximum size of castings that can be produced. While large castings are possible, they often pose significant challenges in terms of mold stability and the uniformity of metal flow during pouring.
Conclusion
In conclusion, sand casting presents a unique blend of advantages and disadvantages. Its versatility, low cost, and flexibility make it a favored choice for many applications. However, manufacturers must also consider factors such as surface finish, dimensional accuracy, and production speed when choosing this process for their casting needs. Understanding these aspects can help businesses make informed decisions tailored to their specific requirements.
Post time:Вер . 05, 2024 00:17
Next:sand casting suppliers