Understanding Sand Casting for Steel A Comprehensive Overview
Sand casting, a foundational technique in metalworking, has been utilized for centuries to create intricate metal parts. This method is especially significant in the production of steel components, offering a unique combination of flexibility, cost-effectiveness, and scalability. In this article, we delve into the intricacies of sand casting steel, exploring its process, advantages, and applications.
The sand casting process begins with the creation of a mold made from sand, which is a key component of this manufacturing technique. The sand is mixed with a binder, typically clay, and water, to hold its shape. Once the sand mold is prepared, it is compacted around a pattern that resembles the desired final product. After the pattern is removed, the cavity left behind forms the shape into which molten steel will be poured.
One of the primary advantages of sand casting is its adaptability to various sizes and complexities of components. This versatility allows manufacturers to produce anything from small intricate parts to large heavy-duty components, making it suitable for a wide range of industries, including automotive, aerospace, and machinery. Furthermore, sand casting is particularly effective for low to medium production runs, helping businesses optimize their costs without compromising on quality.
sand casting steel
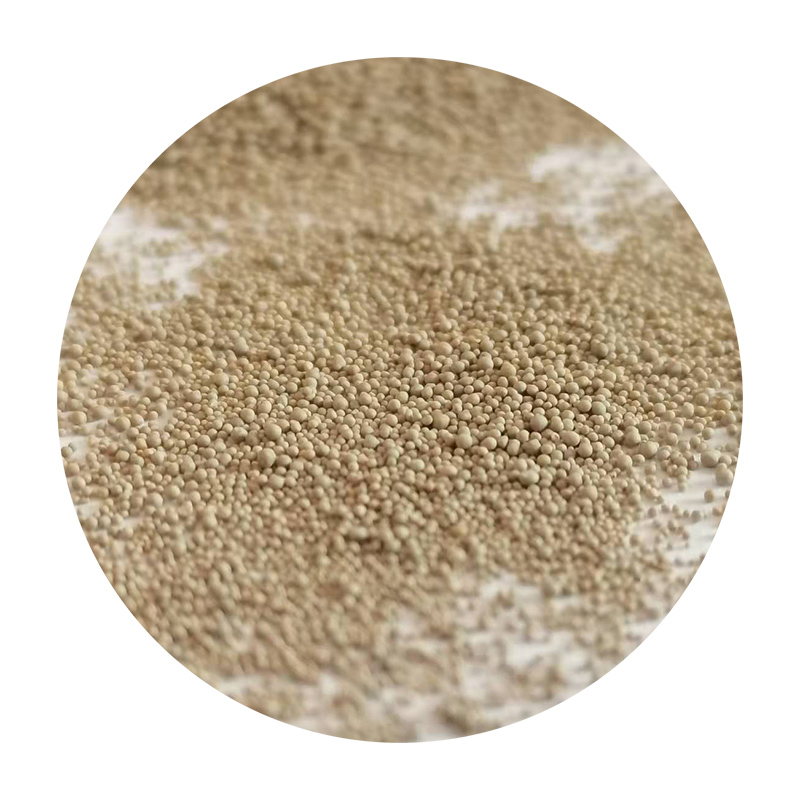
The next step in the process involves heating and melting the steel. This can be accomplished in an electric induction furnace or a cupola furnace, depending on the scale of production and the specific requirements of the steel alloy. Once the steel reaches the desired temperature, it is carefully poured into the sand mold, allowing it to fill the cavity completely while ensuring no air pockets remain.
Cooling and solidification are critical phases of sand casting. As the molten steel cools, it solidifies, taking the shape of the mold. After sufficient cooling time, the mold is broken open, and the newly cast steel part is removed. This phase often requires some degree of post-processing, such as trimming excess material or machining to achieve the desired finish and tolerances.
Despite its many benefits, sand casting does present some challenges, particularly concerning surface finish and dimensional tolerance. However, advancements in technology and mold materials have significantly improved these aspects, allowing for higher precision and better surface quality.
In conclusion, sand casting steel is a robust and efficient method of manufacturing metal parts. Its ability to accommodate complex designs and large variations in size, combined with its cost-effectiveness, makes it a popular choice in various sectors. As industries continue to evolve, sand casting will undoubtedly remain a vital technique in steel production, driving innovation and supporting diverse applications worldwide.
Post time:ئۆكتەبىر . 30, 2024 18:01
Next:golden sand foundation