Sand Casting Iron An Essential Manufacturing Process
Sand casting, one of the oldest methods of metal casting, plays a crucial role in modern manufacturing, particularly in casting iron components. This process is not only versatile but also cost-effective, making it a favored choice in various industries, from automotive to aerospace.
What is Sand Casting?
Sand casting involves creating a mold from a sand mixture in which liquid metal, typically iron, is poured to form a solid shape upon cooling. The procedure begins with the creation of a pattern, usually made from a material such as wood, metal, or plastic. This pattern is a replica of the final product and is used to form a cavity in the sand.
The process begins by mixing sand with a bonding agent, often clay and water. This mixture is then packed around the pattern to form a mold. Once the mold is prepared, the pattern is removed, leaving a hollow cavity that is a negative of the design. Afterward, the mold halves are assembled, and molten iron is poured into the cavity.
Advantages of Sand Casting Iron
1. Cost-Effectiveness Sand casting is relatively inexpensive, requiring less initial investment compared to other casting processes. This affordability makes it accessible for small-scale manufacturers and hobbyists alike.
2. Versatility This method can accommodate complex designs with intricate details. It is suitable for casting a wide range of iron grades, including gray iron, ductile iron, and white iron.
3. Scalability Sand casting is ideal for both small and large production runs. It is commonly used for producing single components or relatively small batches, as well as large quantities when needed.
sand casting iron
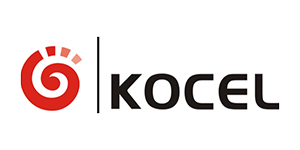
4. Material Efficiency Sand can be reused multiple times, reducing waste and making the process more sustainable. After the casting is complete, the sand can be cleaned, remixed, and used again for future casts.
Applications of Sand Cast Iron
The versatility of sand casting makes it applicable across various industries. In the automotive sector, for instance, sand casting is used to produce engine blocks, manifolds, and other key components that require durability and strength. In construction and infrastructure, cast iron is used for pipes and fittings due to its excellent corrosion resistance and mechanical properties.
Moreover, in the energy sector, sand-cast components are vital for the production of turbines and generators, where high levels of precision and strength are necessary to withstand demanding operational conditions.
Challenges and Considerations
While sand casting presents numerous advantages, it also has challenges. One of the most significant issues is related to surface finish and dimensional accuracy. Sand casts may require additional machining to achieve the desired specifications, particularly for high-precision applications. Additionally, the quality of the sand and the molding process can greatly influence the final product's properties, including strength and porosity.
Temperature control is another critical consideration. Ensuring that the molten iron is at the appropriate temperature during pouring is essential for preventing defects such as cold shuts or shrinkage cavities.
Conclusion
In summary, sand casting iron remains a foundational technique in manufacturing, combining cost-effectiveness with versatility. Its ability to produce complex shapes and forms makes it indispensable in a multitude of applications. As technology advances, the sand casting process continues to evolve, incorporating modern techniques and materials to improve efficiency and output quality. Thus, it stands as a testament to the enduring legacy and relevance of traditional manufacturing methods in today’s fast-paced industrial landscape.
Post time:دېكابىر . 18, 2024 19:11
Next:Innovative Techniques in Lost Foam Casting for Precision Metal Parts Production