The Process and Importance of Sand Casting in Foundries
Sand casting, a time-honored technique in metalworking, has been an integral part of manufacturing for centuries. This process involves creating metal parts by pouring molten metal into a sand mold, allowing it to solidify and take on the desired shape. Sand casting foundries play a crucial role in producing a wide array of components for various industries, from automotive to aerospace, due to its versatility, cost-effectiveness, and ability to produce complex geometries.
The Sand Casting Process
The sand casting process begins with the creation of a pattern, which is a replica of the final product. Patterns can be made from various materials, including metal, plastic, or wood, and they must be designed with shrinkage allowances in mind, as metals expand when heated and contract when cooled.
Once the pattern is ready, a sandbox is prepared using a mixture of sand and a binding agent, typically clay. This mixture provides the mold's required properties, such as strength and permeability. The pattern is pressed into the sand to form a cavity that will hold the molten metal. The mold is then carefully removed from the sand, and the two halves of the mold are assembled, leaving a hollow space that mirrors the pattern's shape.
Next, the metal is heated until it reaches a molten state. Common metals used in sand casting include aluminum, iron, and bronze, each selected for its specific properties and applications. Once the metal has reached the desired temperature, it is poured into the mold through a runner system—a channel that directs the flow of molten metal. The pouring must be done swiftly and accurately to avoid defects in the final product.
After the molten metal has cooled and solidified, the mold is broken apart to reveal the cast part. Various finishing processes, such as machining, sandblasting, or surface treatment, may be applied to enhance the product's dimensional accuracy and surface finish.
Advantages of Sand Casting
sand casting foundry
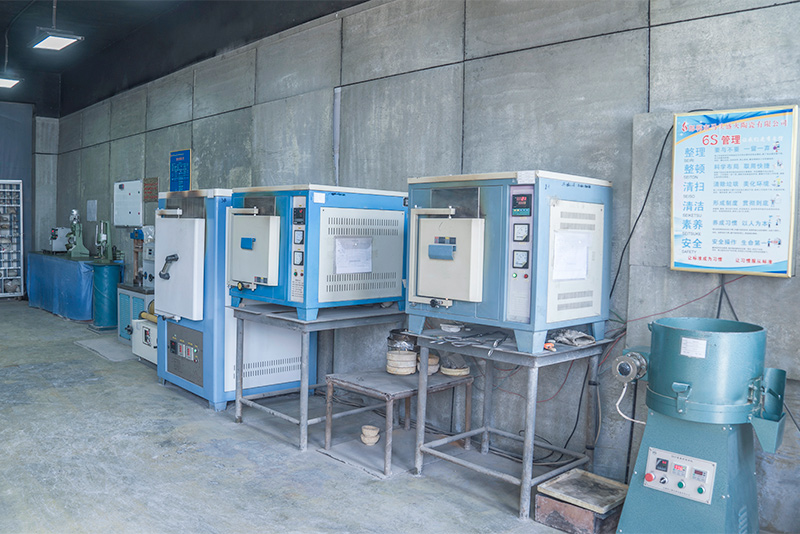
One of the most significant advantages of sand casting is its ability to produce large, complex parts that would be challenging to make using other manufacturing methods. The flexibility in mold design allows for intricate designs, making it an ideal choice for custom components often required in specialized applications.
Cost-effectiveness is another notable benefit. The materials used in sand casting, particularly sand and clay, are relatively inexpensive, and the process can be scaled up for larger production runs without a drastic increase in costs. Furthermore, sand molds can be reused multiple times, which further contributes to the economic viability of this method.
Additionally, sand casting is compatible with a wide range of metals, thus offering considerable versatility for manufacturers. Whether producing small components or large assemblies, the adaptability of sand casting allows foundries to serve various markets effectively.
The Role of Sand Casting Foundries in Industry
Sand casting foundries are pivotal to many industries, supplying critical components for sectors such as automotive, aerospace, marine, and construction. The intricate parts produced through this method often serve as foundational components in vehicles, machinery, and structural systems.
Moreover, the ongoing development and integration of advanced technologies, such as computer-aided design (CAD) and 3D printing, have enhanced the capabilities of foundries. These innovations improve the precision of patterns and molds, reduce lead times, and optimize the overall manufacturing process.
In conclusion, sand casting remains a cornerstone of modern manufacturing due to its unique advantages and capabilities. As industries continue to evolve, the role of sand casting foundries will undoubtedly adapt, yet their fundamental purpose of delivering high-quality, custom metal components will persist. By combining traditional techniques with cutting-edge technology, sand casting foundries are well-positioned to meet the demands of tomorrow's manufacturing landscape.
Post time:ئۆكتەبىر . 19, 2024 13:35
Next:ceramic foundry sand