Understanding Sand Casting An Essential Foundry Process
Sand casting, also known as sand mold casting, is one of the oldest and most widely used metal casting processes. This method involves creating a mold from a mixture of sand and a binding agent, then pouring molten metal into the mold to produce a desired component. The significance of sand casting lies not only in its effectiveness but also in its versatility, allowing for a wide range of metal types and complex part designs.
The Sand Casting Process
The sand casting process consists of several essential steps, each contributing to the successful formation of the final piece. The process begins with the creation of the pattern, which is a replica of the object to be cast. Patterns can be made from a variety of materials, such as wood, metal, or plastic, and they are crafted with precision to ensure that the final product matches the intended specifications.
Once the pattern is ready, the next step involves preparing the sand mold. Typically, the sand used in this process is a silica-based material mixed with a binder (often clay) and water. This mixture is compacted around the pattern to form the mold. After the sand has set, the pattern is removed, leaving behind a hollow cavity in the shape of the desired part. The two halves of the mold are then assembled and secured, creating a complete mold ready for use.
The following step is pouring the molten metal into the mold. The metal is heated until it reaches a liquid state and is then carefully poured into the cavity of the mold. This step requires precision and skill, as any spillage or overflow can lead to defects in the final piece. Once the metal cools and solidifies, the mold is broken apart to reveal the cast part.
Finally, the cast component is cleaned and any imperfections are addressed. This may include processes such as machining, sanding, or surface treatment to achieve the necessary finish and dimensional accuracy.
Advantages of Sand Casting
One of the primary advantages of sand casting is its ability to accommodate complex geometries. The flexibility of the sand mold allows for intricate designs that might be difficult or impossible to achieve with other casting methods. Furthermore, sand casting can be used with a wide range of metals, including aluminum, brass, bronze, and iron, making it suitable for various applications.
sand casting description
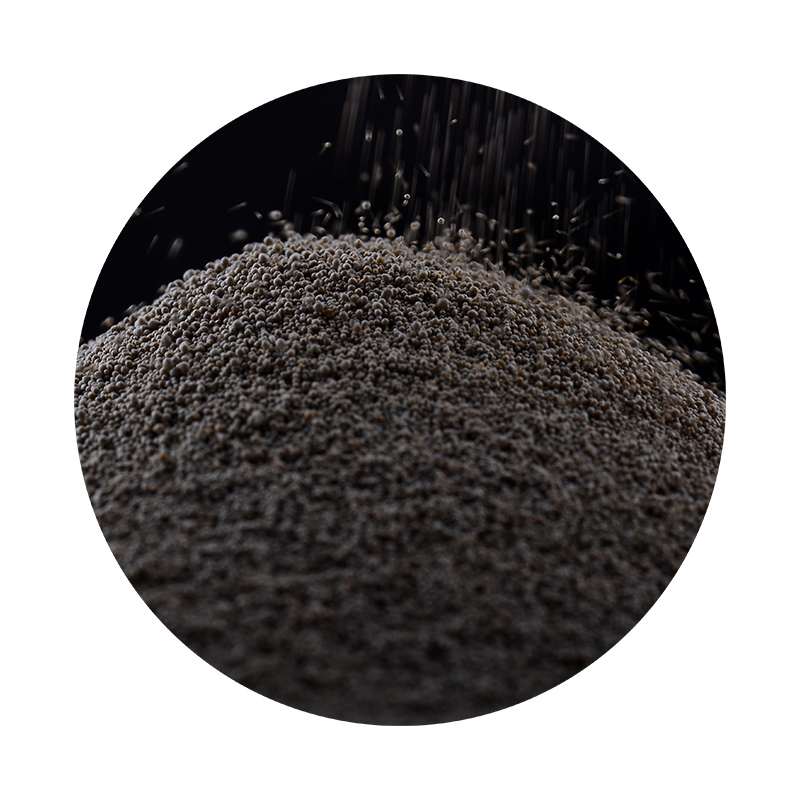
Another notable benefit is the cost-effectiveness of sand casting, especially for low to medium production runs. The materials used, including sand, are relatively inexpensive, and the process does not require the extensive tooling associated with more advanced casting methods. Moreover, the sand molds can often be reused, further reducing costs.
Applications of Sand Casting
Sand casting is widely employed across various industries due to its adaptability. The automotive sector, for instance, utilizes sand casting for manufacturing engine blocks, cylinder heads, and other critical components. The aerospace industry also benefits from this method, using it to produce parts that must withstand extreme conditions.
Additionally, sand casting is prevalent in the construction and energy sectors, where it is used to create components for machinery and tools. Even in artistic applications, sand casting allows sculptors and artisans to produce intricate metal works.
Challenges and Considerations
Despite its many advantages, sand casting is not without its challenges. The process can be labor-intensive and requires skilled personnel to ensure high-quality results. Furthermore, achieving consistent quality across large production runs can be difficult due to variations in the sand mixture and mold making.
Environmental considerations also play a role, as the disposal of used sand and other materials must be managed responsibly to minimize waste and pollutants. Innovations in recycling sand and improving the efficiency of the casting process are ongoing to address these concerns.
Conclusion
In summary, sand casting remains a cornerstone of modern manufacturing, blending ancient techniques with contemporary innovations. Its ability to produce complex shapes with a variety of metals, combined with cost-effectiveness and widespread applications, ensures its relevance in the industry for years to come. As technology advances, the sand casting process will likely evolve, incorporating new materials and methods to improve efficiency and sustainability, solidifying its position in the future of metal casting.
Post time:ئۆكتەبىر . 22, 2024 11:21
Next:Best Sanding Techniques for Resin Projects to Achieve a Smooth Finish