Sand in Casting The Unsung Hero of Metal Fabrication
When it comes to metal fabrication, one of the most time-honored and universally utilized methods is sand casting. This technique, rooted in ancient times, continues to play a vital role in the production of complex metal components used across various industries. At its heart lies the understated yet crucial element sand.
Sand in Casting The Unsung Hero of Metal Fabrication
One of the defining features of sand used in casting is its grain size. The size and uniformity of sand grains directly influence the surface finish of the final product. Coarse sands can lead to rough surfaces, while finer sands can produce a smoother finish. However, finer sand also has a higher chance of collapsing under the weight of molten metal, so a careful balance must be struck. To achieve this, foundries often mix different types of sand or add bonding agents to improve strength while maintaining a fine finish.
sand in cast
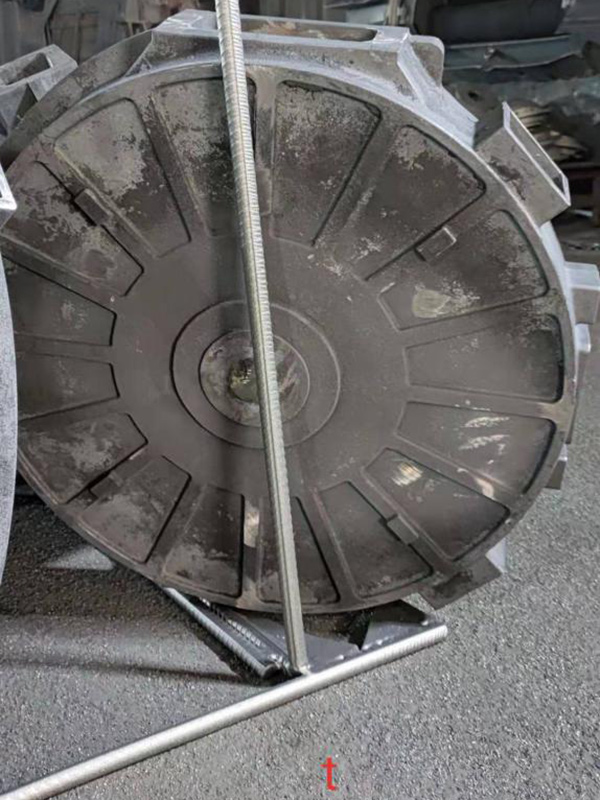
Moreover, the type of binder used in sand mixtures also plays a crucial role in the process. Binders like clay or synthetic resins help hold the sand grains together, giving the mold structural integrity. Green sand, a mixture of silica sand, clay, and water, is a popular choice for many foundries due to its good flowability and ability to retain moisture, which aids in mold strength. Conversely, chemically bonded sands can offer higher precision and durability but may complicate the process due to more stringent handling requirements and costs.
The sand casting process not only allows for a diverse range of shapes and sizes but also permits the incorporation of intricate designs, which are often unattainable through other casting methods. This versatility makes it a favored option for producing components in various sectors, including automotive, aerospace, and art.
However, despite its numerous advantages, the sand casting process is not without challenges. The preparation of the sand, mold making, and the finishing processes can be labor-intensive and time-consuming. Moreover, the quality of the sand used can significantly affect the final product. Contaminants, such as dust and moisture, can lead to defects in casting, making it essential for foundries to uphold stringent quality control measures.
In conclusion, sand in casting serves as the foundation of a process that has stood the test of time. Its ability to withstand the rigors of high temperatures, coupled with the versatility in molding intricate designs, positions it as an integral component in metal fabrication. As industries continue to evolve, the role of sand in casting will undoubtedly adapt, incorporating advanced technologies and materials to enhance efficiency and quality. The humble sand, while often overlooked, remains a testament to the ingenuity and craftsmanship that define the art of metal casting.
Post time:سېنتەبىر . 18, 2024 13:24
Next:ဆူပါသဲပေါင်းစည်းမှု g2 ပါ။