Sand for Casting An Essential Material in Metal Foundry Processes
In the realm of metal casting, sand plays an indispensable role as a mold material due to its unique properties and advantages. Casting is a manufacturing process where molten metal is poured into a mold cavity, allowing it to solidify and take the shape of the desired object. Sand casting, one of the oldest and most versatile casting methods, leverages sand's resilience and thermal stability. This article will delve into the properties, types, and applications of sand in the casting process.
Properties of Sand
The primary properties that make sand suitable for casting are its granularity, thermal conductivity, permeability, and flexibility. Sand grains can vary in size and shape, which directly influences the texture and finish of the final product. For effective casting, the ideal sand should be clean, well-graded, and able to withstand high temperatures without breaking down.
Thermal conductivity is another critical property; the ability of sand to dissipate heat helps to control the cooling rate of the molten metal, thus affecting the microstructure and properties of the finished casting. Furthermore, the permeability of sand molds allows gases produced during solidification to escape, preventing defects like blowholes and ensuring a smooth surface finish.
Types of Sand Used in Casting
There are several types of sand commonly used in the casting process, each with distinct characteristics
1. Green Sand This is a mixture of sand, clay, and water. It is the most traditional form of sand used in casting, widely appreciated for its affordability and ease of use. The moisture content ensures good mold integrity and provides the necessary flexibility.
sand for casting
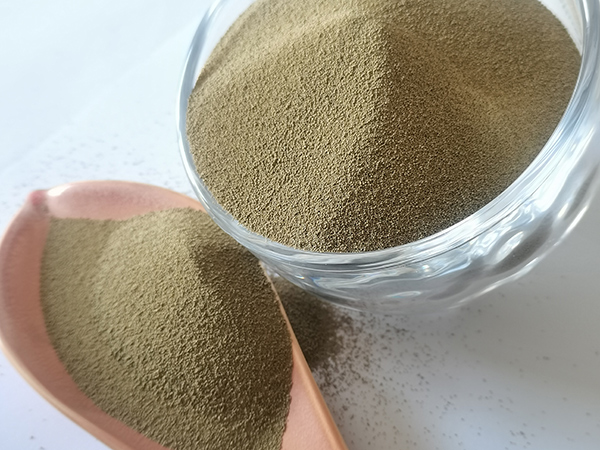
2. Silica Sand Renowned for its high melting point and excellent thermal properties, silica sand is often employed in situations requiring high precision and durability. Its uniform grain structure helps achieve finer finishes.
3. Resin-Bonded Sand In this type, traditional sand is coated with a thermosetting resin, giving enhanced strength and hardness. This allows for more intricate patterns and complex shapes, which is especially beneficial in high-production environments.
4. Zircon Sand With superior thermal resistance, zircon sand is used for casting high-temperature alloys. Its refractory properties make it suitable for applications in aerospace and automotive components.
Applications of Sand Casting
Sand casting is remarkably versatile and is employed across various industries, including automotive, aerospace, marine, and art. It is capable of producing both small and large-scale components, from intricate parts like engine blocks to massive industrial machinery. This method is particularly valuable for producing castings in brass, aluminum, iron, and steel.
In recent years, advancements in sand recycling technologies have furthered the sustainability of sand casting processes. By reclaiming and reusing sand, manufacturers can reduce waste and mitigate the environmental impact associated with sand mining.
Conclusion
In conclusion, sand for casting is a vital material that combines affordability, versatility, and performance. Whether in traditional green sand casting or modern resin-bonded methods, the role of sand is critical in ensuring the efficiency and quality of metal casting processes. As industries continue to evolve, the significance of sand casting remains steadfast, highlighting its enduring legacy in manufacturing.
Post time:سېنتەبىر . 04, 2024 18:33
Next:furan resin sand casting