The Manufacturing Process of Resin Coated Sand
Resin coated sand plays a crucial role in the foundry industry, particularly for the production of high-quality metal castings. Its unique properties, such as excellent strength, thermal stability, and ability to produce smooth surfaces on castings, have made it a preferred choice for many processes. Understanding the manufacturing process of resin coated sand is vital for manufacturers who wish to optimize production and achieve superior results.
Raw Material Selection
The manufacturing process begins with the selection of high-quality sand, typically silica sand. The sand should be clean and free from impurities such as clay and silt. The selection of the resin is equally important; epoxy and phenolic resins are commonly used due to their favorable properties. The choice of resin affects the performance of the coated sand in terms of strength, thermal resistance, and the curing time.
Sand Preparation
Once the raw materials are selected, the first step in the manufacturing process is sand preparation. This involves washing the sand to eliminate any impurities and drying it to a specific moisture content. The drying process is crucial, as any residual moisture can interfere with the coating process and affect the bonding of the resin to the sand grains.
Coating Process
After the sand has been prepared, it undergoes the coating process. This is where the sand is mixed with liquid resin to create the resin coated sand. The typical method used for this process is the fluidized bed method. In this process, the sand is placed in a fluidized bed chamber where it is suspended and agitated by a stream of air. This helps to achieve a uniform coating on each sand grain.
During the application of the resin, a catalyst or hardener may be added, depending on the type of resin used. The mixture is then cooled to ensure that the resin adheres properly to the sand. The quantity of resin used is carefully controlled to optimize the properties of the final product. Too much resin can lead to brittleness, while too little can result in inadequate binding strength.
resin coated sand manufacturing process
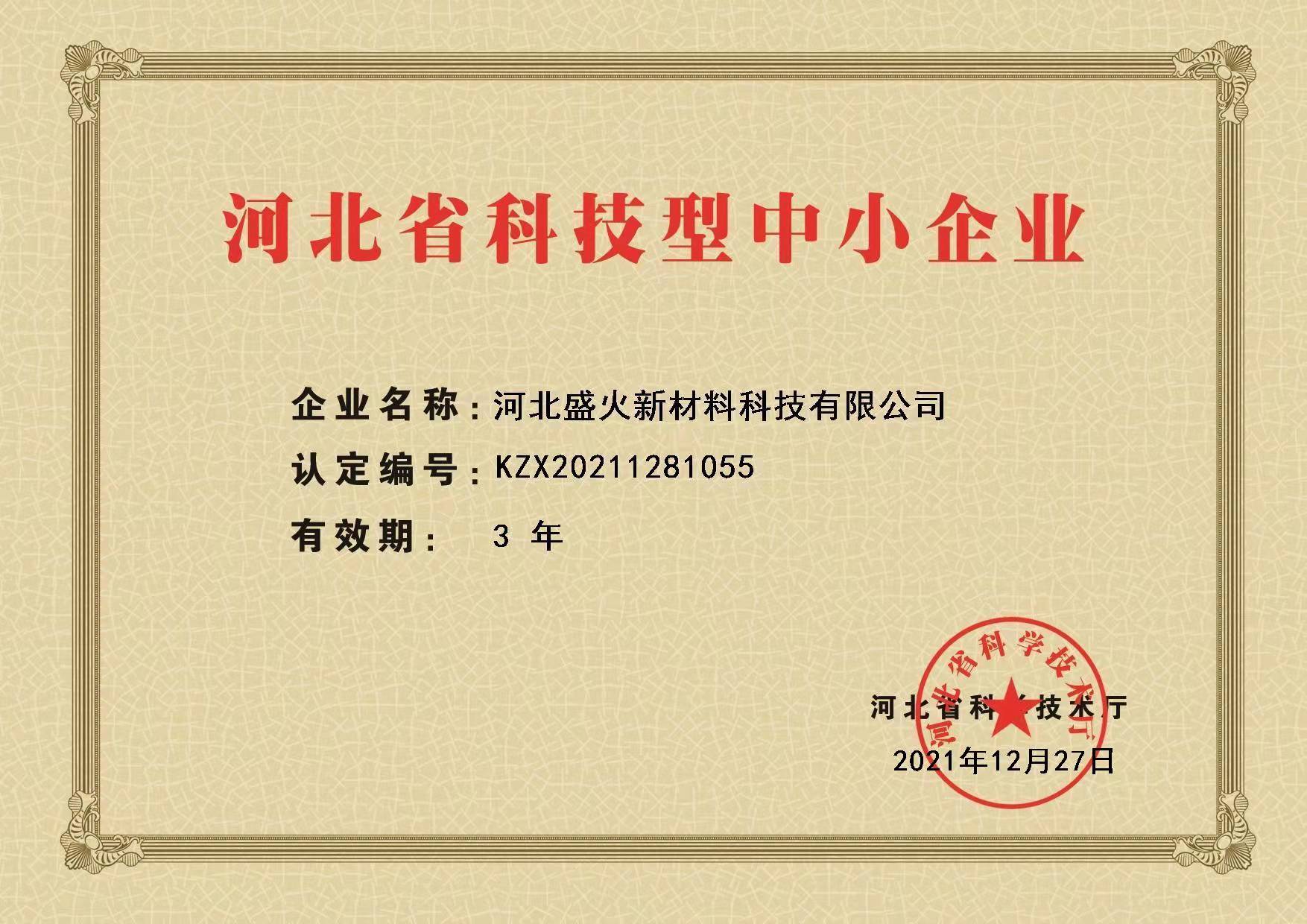
Curing Process
Once coated, the resin sand enters the curing stage. Depending on the type of resin used, this might involve heating the coated sand to activate the curing process. Curing is essential as it determines the final properties of the resin coated sand. Proper curing results in a product with enhanced strength, durability, and thermal stability. It also promotes a fast setting time, which is particularly advantageous in high-volume production settings.
Cooling and Screening
After curing, the resin coated sand is cooled in a controlled environment to prevent any thermal shock that could disrupt the integrity of the sand grains. Once adequately cooled, the sand is screened to remove any oversized particles and ensure uniformity. This step is critical to maintain the quality and consistency of the coated sand, which directly influences the quality of the castings produced.
Quality Control and Testing
Quality control plays an integral role throughout the manufacturing process. Samples of the resin coated sand are regularly taken for testing to ensure they meet the required specifications, including grain size distribution, strength, and thermal properties. This quality assurance is vital to prevent issues in the foundry process, such as defects in the final castings.
Conclusion
The manufacturing process of resin coated sand is intricate, involving careful selection of materials, precise processing steps, and rigorous quality control measures. By optimizing each stage of the process, manufacturers can produce high-quality resin coated sand that meets the demands of the foundry industry. As technology advances and the industry evolves, innovations in the resin coating process will undoubtedly lead to even greater efficiency and improved product performance, solidifying the importance of resin coated sand in metal casting applications.
Post time:نويابىر . 05, 2024 22:50
Next:Bauxite Sand Key Component for Aluminum Production and Environmental Considerations