The Advantages of Resin Coated Sand in Modern Foundries
In the ever-evolving landscape of foundry technology, resin coated sand has emerged as a pivotal material, revolutionizing the production of castings. This innovation addresses long-standing challenges in the casting process, offering numerous benefits that enhance both quality and efficiency. This article explores the features, advantages, and applications of resin coated sand in contemporary foundries.
Resin coated sand, also known as chemically bonded sand, is produced by combining sand grains with a resin binder. The process typically involves mixing high-quality silica sand with thermosetting resins and catalysts, subsequently curing them to create a strong, stable sand grain. This method not only preserves the natural qualities of the sand but also enhances its performance, making it ideal for a variety of casting applications.
One of the most significant advantages of resin coated sand is its excellent dimensional accuracy. When compared to traditional green sand, resin coated sand provides a superior surface finish, allowing for tighter tolerances in casting dimensions. This precision is crucial for industries that demand high-quality outputs, including automotive, aerospace, and heavy machinery sectors. By achieving finer details and smoother surfaces, manufacturers can reduce the need for extensive machining post-casting, which saves time and reduces production costs.
Another key benefit is the enhanced strength and durability of the molds and cores produced using resin coated sand. The cured resin forms a strong bond within the sand, resulting in molds that can withstand the rigors of the casting process. This increased strength reduces the likelihood of mold failure during casting, which can lead to defects, increased scrap rates, and production downturns. Additionally, resin coated sand is less susceptible to moisture, which can compromise the integrity of traditional sand molds, further enhancing reliability.
resin coated sand
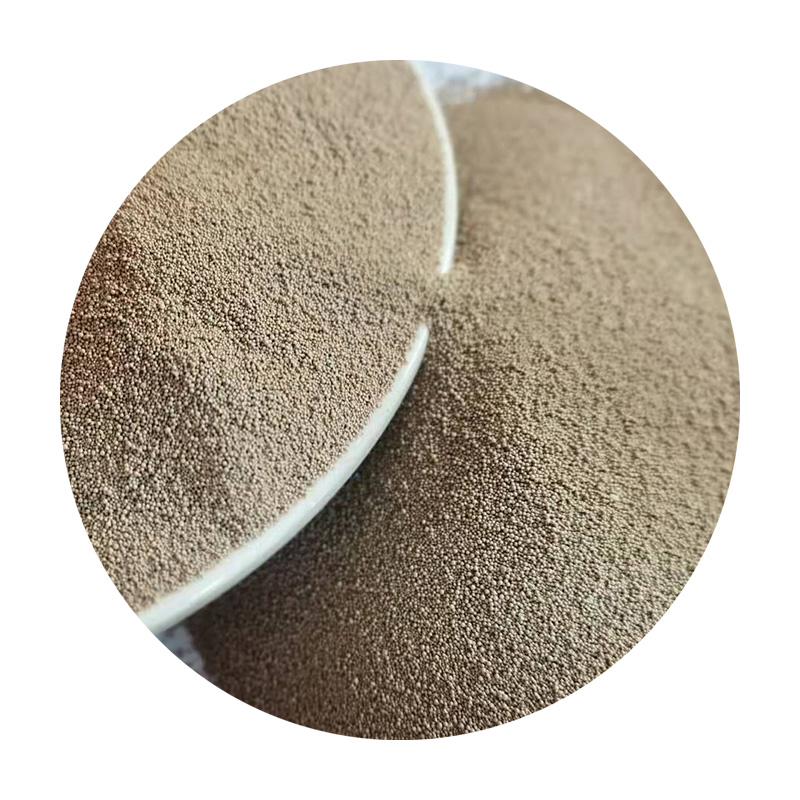
Moreover, resin coated sand contributes to improved surface quality of the final castings. The smooth surface finish of the molds created from this material leads to reduced surface roughness on the castings themselves. As a result, foundries benefit from a decrease in the need for post-casting operations like grinding and machining. This not only streamlines the production process but also enhances the overall aesthetic of the finished product, which is particularly relevant for decorative and consumer-oriented applications.
Environmental concerns are also addressed with the use of resin coated sand. Traditional sand casting processes can generate significant amounts of waste and pollutants, particularly when using green sand. In contrast, the use of resin coated sand allows for greater recyclability. Used sand can often be reclaimed and reused, minimizing waste and reducing the environmental footprint of foundry operations. Additionally, advancements in resin technology have led to the development of more ecologically friendly formulations that align with global sustainability goals.
The versatility of resin coated sand makes it suitable for a wide range of casting methods. It can be utilized in both manual and automated processes, adapting easily to various types of foundries, whether large-scale or specialized. This flexibility encourages foundries to switch to resin coated sand without significant changes to their existing equipment.
In conclusion, resin coated sand represents a significant advancement in foundry materials, offering compelling benefits in terms of dimensional accuracy, mold strength, casting surface quality, and environmental sustainability. As industries continue to demand higher standards for their products, the adoption of resin coated sand is likely to grow, positioning it as a cornerstone of modern casting processes. The transition to this innovative material not only ensures superior casting quality but also aligns with the industry’s increasing focus on efficiency and sustainability.
Post time:ئۆكتەبىر . 17, 2024 06:35
Next:ceramic sand