The Evolution and Benefits of Resin-Bonded Sand Casting
Resin-bonded sand casting has emerged as a highly effective method in the manufacturing industry, particularly for producing precision metal components. This casting technique integrates the traditional sand casting process with modern resin bonding systems, providing significant advantages over conventional methods.
At the heart of resin-bonded sand casting is the use of a synthetic resin as a bonding agent for sand grains. Unlike traditional methods, which rely on water-based clay to bind the sand, resin-bonded systems utilize a chemical reaction initiated by a catalyst to cure the resin rapidly. This process results in a solid mold that is both durable and capable of holding intricate shapes with high fidelity. As a result, manufacturers can create complex geometries and achieve tighter tolerances, which are often critical for industries such as automotive, aerospace, and electronics.
The Evolution and Benefits of Resin-Bonded Sand Casting
Another advantage is the rapid turnaround time associated with resin-bonded sand casting. The curing process of resin is quick, allowing for faster production of molds. As a result, manufacturers can reduce lead times and respond more swiftly to customer demands. This agility in production is increasingly vital in today's competitive landscape, where speed and efficiency can make a substantial difference in market positioning.
resin bonded sand casting
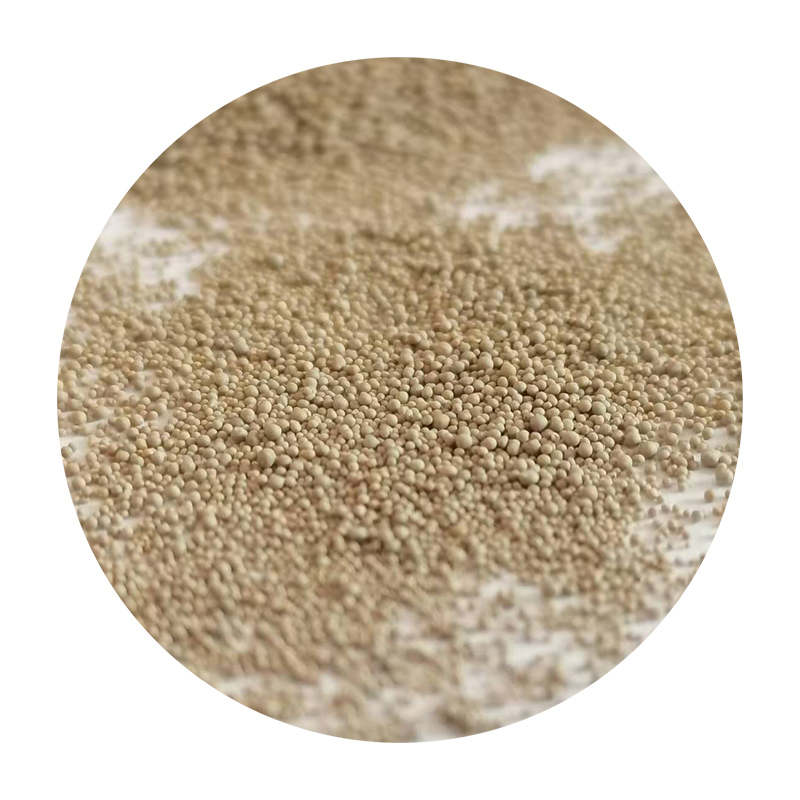
Environmental concerns and sustainability also play a role in the adoption of resin-bonded sand casting. Traditional sand casting often generates significant amounts of waste and requires extensive cleaning processes to remove impurities. Conversely, resin-bonded systems allow for better control over these factors, leading to reduced waste and a more environmentally friendly process. Moreover, advances in sustainable resin formulations are helping to further enhance the eco-friendliness of this casting method.
The versatility of resin-bonded sand casting cannot be understated. It is compatible with a wide range of metals, including aluminum, iron, and bronze, making it suitable for various applications. Manufacturers can produce everything from small components to large, complex assemblies, catering to diverse market needs. Additionally, the flexibility in mold design means that changes to specifications can be accommodated relatively easily, facilitating the bespoke production of components.
While resin-bonded sand casting offers numerous advantages, it is important to note that it also presents challenges. The material cost associated with resin can be higher than traditional binding agents, and the handling of chemicals requires careful management to ensure the safety of workers and compliance with environmental regulations. However, for many manufacturers, the benefits outweigh these challenges, leading to increased adoption of this innovative process.
In conclusion, resin-bonded sand casting represents a significant advancement in the field of manufacturing. Its ability to produce high-quality, precise metal components quickly and sustainably positions it as an attractive option for a wide array of industries. As technology continues to evolve, the techniques and materials used in resin-bonded sand casting are likely to improve further, making this method an even more integral part of modern manufacturing processes. With its combination of efficiency, precision, and environmental benefits, resin-bonded sand casting is set to play a pivotal role in the future of metal casting.
Post time:نويابىر . 27, 2024 12:00
Next:Understanding the Definition and Purpose of Foundry Sand in Metal Casting