The Physical Properties of Foundry Sand An Essential Element in Metal Casting
Foundry sand plays a pivotal role in the metal casting process, serving as the primary material for creating molds and cores. Its properties significantly influence the quality of castings and, consequently, the efficiency and productivity of the manufacturing process. Understanding the physical properties of foundry sand is essential for foundry engineers and metallurgists, as it helps in selecting the appropriate sand for specific casting applications and in optimizing the casting process itself.
1. Chemical Composition
The primary component of foundry sand is quartz (SiO2), which typically constitutes 80-90% of the sand used in foundries. Other components may include feldspar, clay, and minerals that can affect the properties of the sand and the final cast product. The chemical composition is critical since impurities can introduce inconsistencies in the casting process, leading to defects such as inclusions or poor surface finishes. Therefore, the purity and composition of foundry sand should be carefully controlled to ensure optimal performance.
2. Grain Size and Shape
The grain size and shape of foundry sand significantly affect its behavior during the molding process. Sands are classified by their grain size, which typically ranges from 0.1 to 0.5 mm for most foundry applications. A uniform grain size can help in achieving a consistent mold density and surface finish, while a well-graded mixture of sand grains can enhance permeability and allow gases to escape during pouring. Furthermore, the shape of the grains—whether angular, sub-angular, or rounded—also influences the packing density and strength of the mold. Angular grains tend to interlock better, providing higher mold strength, while rounded grains improve flowability, making them easier to handle.
3. Permeability
Permeability is one of the most critical physical properties of foundry sand. It refers to the ability of the sand mixture to allow gases (like steam and air) to escape from the mold during the pouring of molten metal. High permeability prevents defects such as gas porosity in the castings. Fine sand often has lower permeability, while coarser sands generally exhibit higher values. The balance between grain size and the amount of binder used is vital to achieve the desired permeability without compromising the mold strength.
physical properties of foundry sand
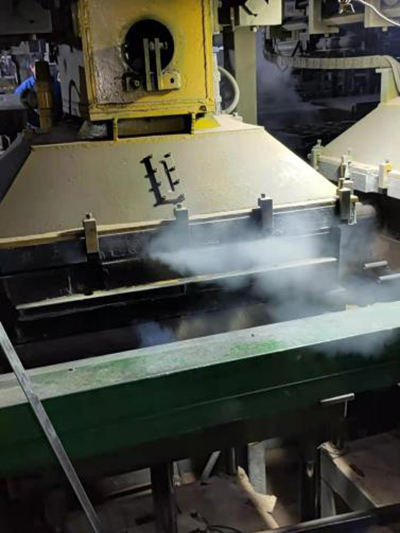
4. Moisture Content
The moisture content in foundry sand is another important physical property. It affects the bonding and cohesive strength of the sand mix. A precise moisture level is necessary to ensure that the sand binds together effectively when packed around the pattern. Typically, foundries aim for a moisture content of around 3-7%. Excess moisture can lead to sand expansion and defects in the casting, while too little moisture may prevent the sand from staying compacted sufficiently, resulting in a weak mold.
5. Thermal Stability
Foundry sand must possess excellent thermal stability to withstand the high temperatures of molten metal without degrading or losing its structural integrity. Sands that can maintain their strength and shape at elevated temperatures will contribute to higher quality castings. Some sands, like chromite and zircon, exhibit superior thermal properties, making them suitable for high-temperature applications and for casting metals with high melting points.
6. Strength and Resilience
The strength of the mold and core made from foundry sand is crucial to prevent deformation during the pouring and cooling of molten metal. This tensile strength is influenced by factors such as the type of binder used, moisture content, and the compaction of the sand. The resilience of the sand mix also affects its ability to return to its original form once the metal is removed. A good foundry sand should withstand the mechanical stresses experienced during the casting process while also providing a smooth surface finish to the final product.
In conclusion, the physical properties of foundry sand—such as grain size, shape, permeability, moisture content, thermal stability, and strength—are critical factors that affect the quality of castings and the efficiency of the casting process. Foundry engineers must carefully evaluate these characteristics when selecting sand for specific applications to ensure optimal performance and minimize defects in the final product. As advancements in sand technologies continue to evolve, understanding these physical properties will be essential for achieving higher performance standards in metal casting.
Post time:ئۆكتەبىر . 09, 2024 12:13
Next:Specifications and Standards for Foundry Sand in Metal Casting Applications