Metal Sand Casting An Overview
Metal sand casting is a versatile and widely used manufacturing process that allows for the creation of complex metal parts. This technique has a rich history and continues to be a relevant method for producing various components across multiple industries, including automotive, aerospace, and general manufacturing. In this article, we will explore the principles of metal sand casting, the materials involved, the process, its advantages, and applications.
Principles of Metal Sand Casting
Metal sand casting involves pouring molten metal into a mold made from sand, which can be easily shaped to create intricate designs. The basic principle centers around creating a cavity in the sand that mirrors the desired final product. Once the molten metal cools and solidifies, the mold can be removed, revealing the finished piece. This process allows for flexibility in design and is particularly suited for small to medium-sized production runs.
Materials Used
The primary material for molds in sand casting is silica sand, which is favored for its excellent properties, including grain size, permeability, and ability to withstand high temperatures. Additives such as clay and water are mixed into the sand to improve cohesion and help maintain the shape of the mold. The metal used for casting can vary widely, including cast iron, aluminum, bronze, and steel. The choice of metal depends on the intended application, desired mechanical properties, and cost considerations.
The Metal Sand Casting Process
The metal sand casting process can be broken down into several key steps
1. Pattern Creation A pattern, typically made of wood, plastic, or metal, is crafted to represent the final product. This pattern is crucial as it serves as the original form from which the mold is made.
2. Mold Making The pattern is placed in a mold box, and sand is packed around it to form the mold. Once the sand is compacted, the pattern is removed, leaving a cavity that matches the shape of the object to be cast.
3. Core Making For more complex shapes that require internal features, cores made from sand are created. These cores are placed in the mold to produce hollow sections in the final casting.
metal sand casting
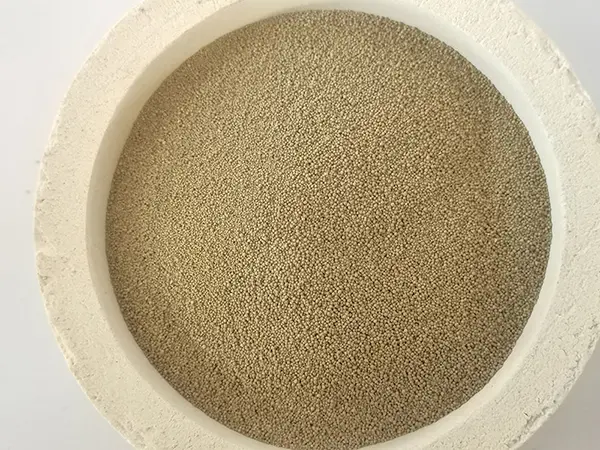
4. Metal Melting The chosen metal is melted in a furnace. This process requires careful temperature control to ensure the metal reaches its melting point without contamination.
5. Pouring The molten metal is poured into the prepared mold. This step needs to be executed quickly and accurately to fill the mold before the metal begins to solidify.
6. Cooling After pouring, the metal is allowed to cool and solidify in the mold. The cooling rate will affect the properties of the final product, including strength and surface finish.
7. Mold Removal Once the metal has cooled sufficiently, the sand mold is broken apart to reveal the casting.
8. Finishing The final step involves cleaning, machining, and finishing the casting to meet the required specifications. This may include removing any defects, smoothing surfaces, and applying coatings.
Advantages of Metal Sand Casting
Metal sand casting boasts several advantages that make it a popular choice for manufacturers. Its ability to create large, complex geometries is unrivaled, and the process can be adapted for both ferrous and non-ferrous metals. Additionally, the initial setup costs are relatively low compared to other casting processes. Since sand molds can be reused, the overall production can be economical for moderate batch sizes. Furthermore, the process is flexible, as it can accommodate rapid design changes without the need for extensive tooling adjustments.
Applications
Due to its adaptability, metal sand casting finds applications in various sectors. The automotive industry utilizes it for creating engine blocks, transmission cases, and other critical components. The aerospace sector benefits from lightweight aluminum castings for aircraft parts. Additionally, sand casting plays a vital role in the production of decorative items, art, and sculpture, where intricate designs are paramount.
Conclusion
In summary, metal sand casting is a time-tested technique that remains relevant in modern manufacturing. Its ability to produce complex shapes with a variety of metals makes it invaluable across numerous industries. As technology continues to evolve, the integration of advanced materials and techniques in metal sand casting promises to enhance its efficiency and broaden its applications, ensuring that it will continue to play a significant role in the manufacturing landscape for years to come.
Post time:ئۆكتەبىر . 20, 2024 04:23
Next:sand castings supplier