Understanding Foundry Sand Composition A Critical Element in Metal Casting
Foundry sand is a vital component in the metal casting process, serving as a molding medium to shape molten metal into desired forms. The composition of foundry sand plays a crucial role in determining the quality of the final metal product, influencing factors such as strength, permeability, and thermal stability. This article delves into the various constituents of foundry sand, their functions, and the significance of proper composition in casting applications.
Primary Components of Foundry Sand
The fundamental material used in foundry sand is silica, primarily in the form of quartz. Silica sand is favored for its high melting point, chemical inertness, and ability to withstand thermal shock. It constitutes the bulk of the sand mixture, typically making up 80% to 90% of the total composition. The roundness and grain size of silica sand also significantly affect its flowability and compactability, which contribute to the overall quality of the mold.
In addition to silica, foundry sands may contain various additives to enhance specific properties. These include clay, which is often used to bind the sand grains together, providing strength and cohesiveness to the mold. Bentonite clay is a common choice due to its excellent binding capabilities and ability to retain moisture. The presence of clay not only improves mold strength but also contributes to the permeability of the sand, allowing gases to escape during the pouring of molten metal.
Another additive commonly found in foundry sand is lubricant, which reduces friction between the sand mold and the molten metal, facilitating easier removal of the casting after cooling. Additionally, coal dust or other carbonaceous materials may be mixed into the sand to improve the surface finish of the casting and minimize oxidation of the molten metal.
The Importance of Grain Size and Shape
foundry sand composition
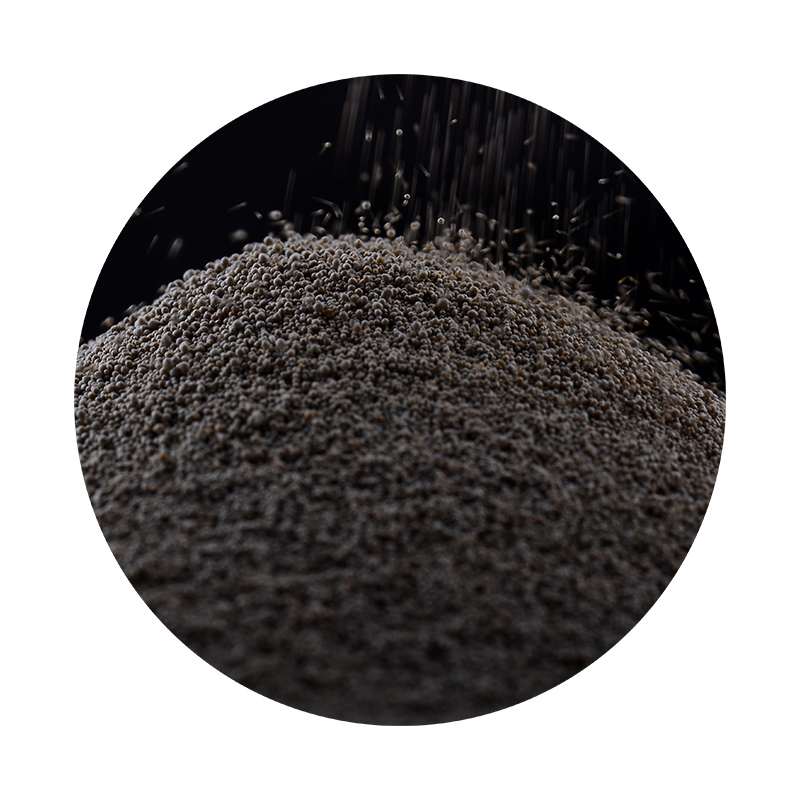
The grain size and shape of foundry sand critically influence its handling and performance properties. Ideal foundry sand should have a well-graded mix of fine and coarse grains to ensure optimal packing density. Fine sands provide excellent detail reproduction and surface finish, while coarser grains contribute to increased strength and permeability. A balanced grain size distribution allows for better airflow and escape of gases, reducing the risk of defects such as porosity or blowholes in the final casting.
Round grains are preferable in foundry sand because they facilitate better flow and packing efficiency. Angular grains, while providing more interlocking and strength, can lead to difficulties in handling and less effective flow. Therefore, choosing the right shape and size of sand grains is key to achieving high-quality molds and castings.
Contaminants and Their Effects
The composition of foundry sand can be affected by contaminants, which may arise from the environment, recycling processes, or the materials used in previous castings. Common contaminants include dust, clay, and metal residues, which can adversely affect the properties of the sand. The presence of contaminants can lead to inadequate mold integrity, resulting in casting defects such as surface imperfections and dimensional inaccuracies.
To maintain optimal foundry sand composition, regular testing and quality control measures are essential. This includes monitoring for moisture content, grain size, and the presence of contaminants. Many foundries will implement recycling processes to reuse sand, which not only reduces costs but also minimizes environmental impact. However, proper processing and conditioning of recycled sand are vital to ensure that its properties remain suitable for high-quality metal casting.
Conclusion
The composition of foundry sand is a critical factor in the metal casting industry, impacting the performance and quality of the final product. Understanding the roles of silica, clay, and various additives is essential for foundries to optimize their casting processes. As the industry moves towards more sustainable practices, maintaining the integrity and quality of foundry sand through proper sourcing, testing, and recycling will be paramount in producing high-quality castings that meet stringent market demands. By prioritizing the right sand composition, foundries can ensure the longevity and reliability of their cast products while also adhering to environmental standards.
Post time:نويابىر . 08, 2024 08:34
Next:The Historical Origins and Development of Sand Casting Techniques Through the Ages