The Role of Ceramsite Foundry Sand in Modern Casting Processes
In the ever-evolving field of metallurgy and casting, the materials used play a crucial role in the quality and efficiency of the final products. Among these materials, ceramsite foundry sand has emerged as an innovative alternative to traditional sand types, offering numerous advantages that enhance the casting process.
Understanding Ceramsite Foundry Sand
Ceramsite foundry sand is a type of engineered sand produced through the high-temperature sintering of clay and other natural raw materials. The result is a lightweight, spherical, and uniform grain structure that enhances mold and core-making capabilities. Unlike conventional foundry sands, ceramsite sand boasts higher thermal stability, lower water absorption, and improved flowability, making it an attractive choice for modern foundries.
Advantages of Ceramsite Foundry Sand
1. Improved Casting Precision The uniformity of ceramsite sand particles contributes to better mold surface finish and dimensional accuracy. This precision is critical in industries where intricate designs are prevalent, such as aerospace, automotive, and intricate component manufacturing.
2. Enhanced Thermal Properties Ceramsite foundry sand can withstand higher temperatures compared to traditional sands. This property ensures that the sand retains its shape and does not deform during the casting process, reducing scrap rates and improving yield.
3. Reduction in Defects The superior flowability of ceramsite allows for better packing density in molds and cores, leading to fewer air pockets and defects in cast products. This characteristic is vital in producing high-quality castings with minimal rework.
4. Environmentally Friendly As environmental regulations tighten, the need for sustainable materials in foundries has become paramount. Ceramsite sand is often produced from recycled materials and can be used in a closed-loop system, reducing waste. Additionally, its non-toxic nature makes it safer for workers and the environment compared to some traditional sand materials.
ceramsite foundry sand
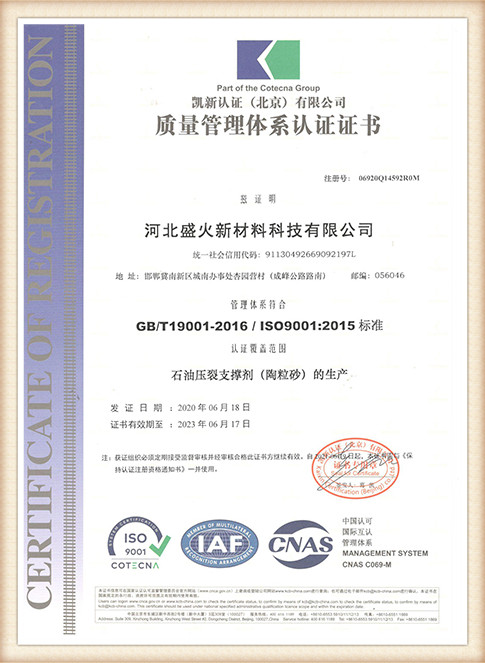
5. Cost-Effectiveness While the initial cost of ceramsite foundry sand may be higher than conventional sand, the long-term savings can be significant. The increased durability of ceramsite sand reduces the frequency of sand replacement and maintenance, leading to lower operational costs. Furthermore, the reduction in defects translates directly into financial savings by minimizing rework and scrap.
Applications in Various Industries
Ceramsite foundry sand is increasingly utilized across various sectors, including
- Automotive Industry In casting complex engine components requiring high precision and strength, ceramsite sand proves to be an invaluable asset. Its ability to maintain structural integrity at high temperatures aligns perfectly with the rigorous demands of automotive manufacturing.
- Aerospace Sector The aerospace industry demands exceptional quality and performance from its components. Ceramsite foundry sand provides the required dimensional accuracy and surface finish necessary for parts that undergo extreme conditions.
- Artistic and Architectural Applications Beyond industrial usage, ceramsite foundry sand is also employed in artistic and architectural applications. Its fine grain allows for intricate designs and detailed artwork, catering to the creative needs of sculptors and architects.
Conclusion
In summary, ceramsite foundry sand is revolutionizing the casting process by offering enhanced properties that traditional sands cannot match. Its improved casting precision, thermal stability, and environmentally friendly production methods make it an essential material in modern foundries. As industries continue to push for innovation and efficiency, ceramsite foundry sand is poised to play an increasingly significant role, driving advancements in casting technologies and resulting in superior products across various sectors. By embracing this advanced material, foundries can not only improve their processes but also contribute to a more sustainable and efficient future in manufacturing. As the demand for high-quality, precise castings increases, ceramsite foundry sand will undoubtedly solidify its position as a crucial component in the foundry landscape.
Post time:نويابىر . 15, 2024 10:59
Next:youtube sand casting