Casting Sand The Unsung Hero of Metal Foundry Process
Casting sand is a critical material in the metal foundry industry, playing an integral role in the production of various components used in everyday applications. While it may not receive the accolades it deserves, casting sand significantly contributes to the efficiency, precision, and overall quality of metal casting processes. This article delves into the world of casting sand, exploring its composition, types, applications, and the future of this essential foundry material.
The Composition of Casting Sand
Casting sand primarily consists of silica, which is the key ingredient responsible for its desirable properties. The grains of silica sand provide a good balance between permeability and strength, allowing them to withstand the heat of molten metal. In addition to silica, casting sand may contain other materials, such as clay and water, which enhance its binding properties and improve its moldability. The typical grain size for casting sand ranges from 0.1 mm to 1.5 mm, with finer grains creating finer details in castings and coarser grains providing better drainage.
Types of Casting Sand
There are several types of casting sand, each suited for specific applications. The most common types include
1. Green Sand This is the most widely used type of casting sand, composed of a mixture of silica sand, clay, and water. Green sand molds are known for their excellent formability, allowing them to capture intricate details. They are commonly used for casting ferrous metals, such as iron and steel.
2. Dry Sand Unlike green sand, dry sand molds are made without water, resulting in a much harder and more durable mold. These molds are typically used for casting non-ferrous metals like aluminum and can withstand higher temperatures.
3. Resin Sand This type of sand uses a resin binder, providing superior strength and thermal stability. Resin-coated sands are often employed for complex castings that require high precision and intricate designs.
casting sand
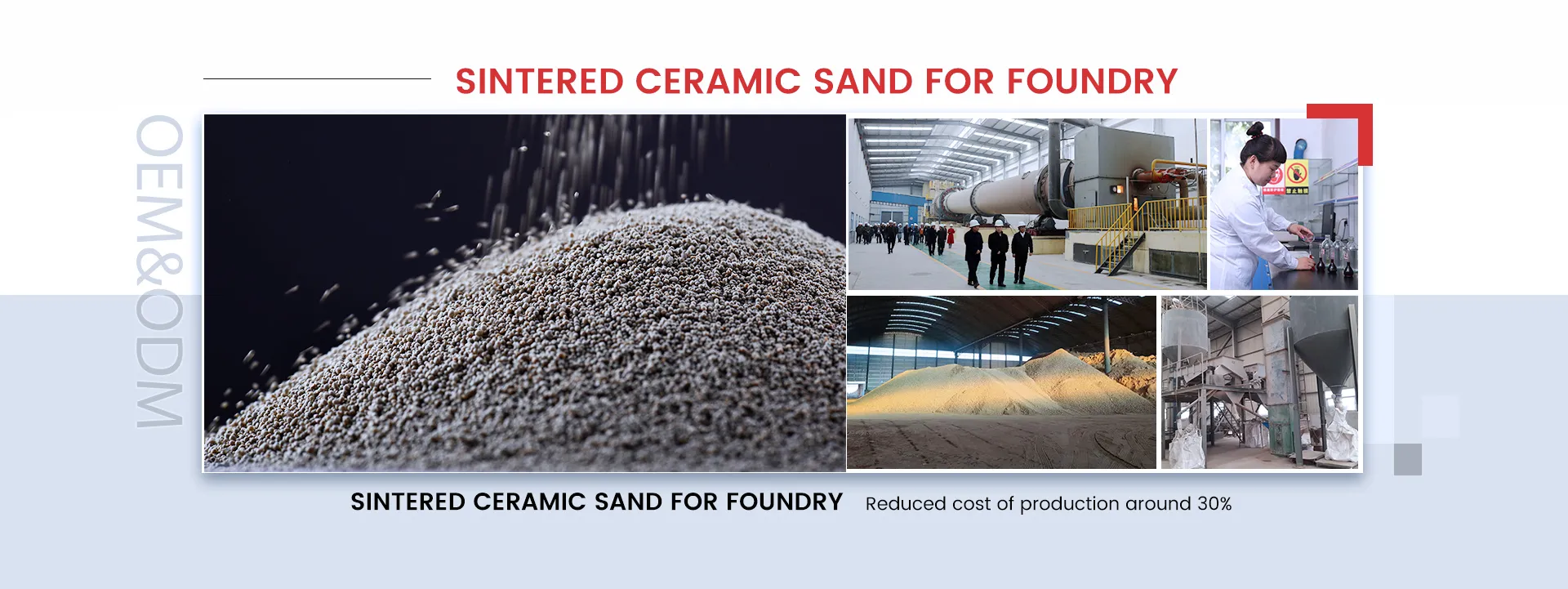
4. Shell Sand Shell sand casting involves creating a thin shell of sand around a mold. This method provides excellent surface finish and dimensional accuracy, making it suitable for high-performance applications.
Applications of Casting Sand
Casting sand is used in a variety of industries, including automotive, aerospace, and construction. It is instrumental in producing engine blocks, cylinder heads, gears, and many other components critical to modern machinery. The aerospace sector relies on high-precision cast parts that meet stringent quality standards, where casting sand’s ability to create intricate designs and fine details becomes invaluable.
Additionally, casting sand is not limited to metal casting. It also plays a role in artistic endeavors, such as sculpting and decorative casting. Artists and artisans utilize different types of casting sands to achieve unique textures and finishes in their works.
Future of Casting Sand
As industries evolve, so too will the materials used in the casting process. The push for sustainable practices has prompted researchers to explore alternatives to traditional casting sand. Innovations include reclaiming and reusing spent sand, as well as developing eco-friendly binders. These advancements aim to reduce waste and environmental impact while maintaining the quality required for effective metal casting.
Moreover, advancements in 3D printing technologies are beginning to revolutionize the way molds are created. While casting sand will remain a staple in traditional foundries, the integration of 3D printing techniques may lead to faster, more efficient casting processes, further solidifying casting sand’s place in the future of manufacturing.
Conclusion
Casting sand, despite being an unsung hero in the metal foundry industry, plays a pivotal role in the production of numerous metal components. Its unique properties and versatility make it an essential material across various applications. As the industry moves towards more sustainable and innovative practices, the importance of casting sand will continue to evolve, ensuring its relevance in a changing manufacturing landscape.
Post time:نويابىر . 10, 2024 07:06
Next:When and Why to Sand Your 3D Printed Models for the Best Finish