Application of Sand Casting Process
Sand casting, one of the oldest and most versatile metal casting processes, has been a cornerstone of modern manufacturing. This method, characterized by its simplicity and cost-effectiveness, is widely used in various industries such as automotive, aerospace, and art. Its applicability to creating intricate shapes and large components makes it an invaluable process in manufacturing today.
Historical Background
Sand casting dates back over 5,000 years, with its origins traced to ancient civilizations that utilized clay molds to produce simple metal items. Over the centuries, the technique has evolved, incorporating advancements in materials and technology. This evolution enhances both the quality and efficiency of the casting process, allowing for the production of intricate designs and large-scale parts.
Process Overview
The sand casting process involves several steps. First, a pattern made of wood, metal, or plastic is created, which reflects the desired final product. This pattern is then placed into a molding box, and sand is packed around it, forming a mold. The sand used is typically mixed with a binding agent, allowing it to hold its shape. Once the mold is set, the pattern is removed, leaving a cavity that reflects the shape of the pattern.
Next, molten metal is poured into the mold. The choice of metal varies based on the desired characteristics of the final product, with options ranging from aluminum, iron, to various alloy compositions. After the molten metal cools and solidifies, the sand mold is broken away, revealing the cast part. This part may then require further processing such as machining or surface treatment to achieve the desired specifications.
Advantages of Sand Casting
application of sand casting process
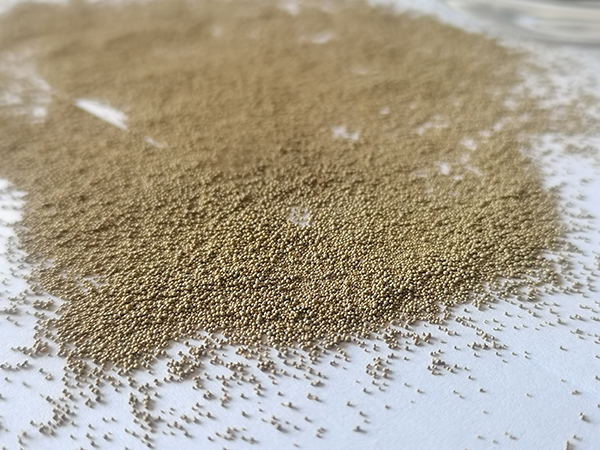
One of the main advantages of sand casting is its ability to produce large and complex components. The flexibility of sand as a mold material allows for designs that would be difficult or impossible to achieve with other casting methods. Furthermore, sand casting is cost-effective, particularly for low to moderate production runs. The materials used, primarily sand, are abundant and inexpensive, making this technique accessible to a wide range of manufacturers.
Another key benefit is the ease of pattern making. Patterns can be crafted from various materials depending on the scale of production, and modifications can be made without significant investment in new tooling. This adaptability is crucial in industries like automotive manufacturing, where rapid prototyping and iterative design processes are essential.
Applications in Industry
Sand casting finds application in multiple sectors. In the automotive industry, it is commonly used for producing engine blocks, transmission housings, and other components that require durability and strength. The aerospace sector also benefits from sand casting, allowing for the production of lightweight and strong parts that can withstand high-stress conditions.
Moreover, the art and sculpture industry utilizes sand casting for creating intricate artworks and sculptures. Artists can create detailed patterns, capturing minute details that traditional methods may find challenging. This process not only provides an avenue for artistic expression but also allows for the mass production of decorative items.
Future Trends
Looking ahead, the sand casting process is poised for continued innovation. Advancements in materials, such as the development of high-performance sands and environmentally-friendly binders, are enhancing the effectiveness and sustainability of the process. Moreover, the integration of digital technologies, like 3D printing, in the pattern-making stage is streamlining operations and reducing lead times.
In conclusion, sand casting remains a vital manufacturing process with a rich history and broad applications. Its ability to produce complex shapes at a low cost ensures its relevance in today’s competitive landscape. As industries continue to evolve, the sand casting process is expected to adapt, integrating new technologies to meet the challenges of modern manufacturing while preserving its foundational principles. The continued exploration of its capabilities will no doubt yield innovative solutions that advance the field of metal casting.
Post time:ئۆكتەبىر . 10, 2024 02:32
Next:Understanding the Process of Sand Casting in Metalworking Techniques