Advantages and Disadvantages of Sand Casting Process
Sand casting, one of the oldest and most widely used metal casting processes, involves creating a mold from sand to produce intricate metal parts. This method has several advantages and disadvantages that must be considered when deciding whether to employ it for a particular project.
Advantages of Sand Casting
1. Cost-Effectiveness One of the most significant advantages of sand casting is its cost-effectiveness. The materials used, such as sand, clay, and water, are relatively inexpensive and readily available. This makes sand casting an economical option, especially for small-scale production and prototyping.
2. Versatility Sand casting can accommodate a wide range of metals, including aluminum, copper, iron, and bronze. This versatility allows manufacturers to produce various products across different industries, from automotive components to artistic sculptures.
3. Complex Geometries The sand casting process can create intricate and complex geometries that would be challenging or impossible to achieve with other methods. The ability to produce detailed features makes sand casting an attractive option for designers and engineers looking to innovate.
4. Large Parts Sand casting is capable of producing large components, which can be challenging for other casting technologies. Large sand molds can be made to cast heavy machinery parts, engine blocks, and other significant components.
5. Easy Pattern Making The pattern for sand casting can be made from various materials, such as wood, metal, or plastic, and it can be relatively easy and quick to fabricate. This flexibility allows for rapid prototyping and adjustments to designs.
6. Low Setup Time Compared to other casting processes, such as die-casting, sand casting typically requires less setup time. This is advantageous for both short production runs and the rapid prototyping of new designs.
advantages and disadvantages of sand casting process
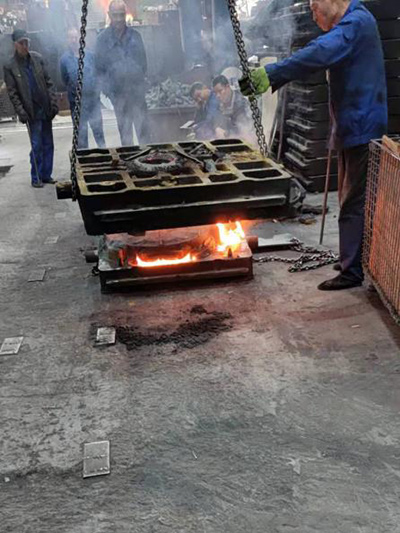
Disadvantages of Sand Casting
1. Surface Finish and Tolerances One of the main drawbacks of sand casting is the surface finish quality. Parts produced through this process often have a rough surface, which may require additional machining or finishing to meet aesthetic or functional demands. Additionally, tolerances may not be as tight as in other casting methods, leading to potential issues in assembly.
2. Labor-Intensive The sand casting process can be labor-intensive, especially in the assembly of sand molds and the subsequent cleaning and finishing of cast parts. This can increase production costs and time.
3. Limited Production Rates While sand casting is cost-effective for small runs, it is not ideal for high-volume production. The time required to create each mold can lead to longer lead times compared to methods like die-casting or injection molding.
4. Environmental Concerns The sand casting process can produce waste material and generate dust. Though many foundries are implementing environmentally friendly practices, the traditional methods can pose environmental challenges that need addressing.
5. Inconsistency Due to the manual aspects of the process, there can be inconsistencies in the quality of the cast products. Factors such as sand quality, moisture levels, and human error can affect the final result.
Conclusion
In conclusion, sand casting remains a popular choice for metal casting due to its cost-effectiveness, versatility, and ability to produce complex geometries. However, its disadvantages, such as rough surface finishes and labor-intensive processes, may lead manufacturers to consider alternative methods for specific applications. Ultimately, the decision to use sand casting should be guided by the specific requirements of the project, including the desired final product characteristics and production volume. Understanding both the advantages and disadvantages of sand casting allows industries to make informed decisions and optimize their manufacturing processes.
Post time:ئۆكتەبىر . 13, 2024 03:18
Next:how does sand casting work