Types of Sand Used in Sand Casting
Sand casting is a versatile and widely used manufacturing process that involves creating metal parts by pouring molten metal into a mold made of sand. The choice of sand is crucial, as it impacts the quality of the final product. Here, we will explore the various types of sand commonly used in sand casting, each with its unique properties and applications.
Types of Sand Used in Sand Casting
2. Dry Sand Dry sand is prepared by thoroughly drying the sand mixture before molding. This type of sand is often used for more intricate casting processes because it produces finer details and a smooth surface finish. Although it can be more expensive to produce than green sand, dry sand molds are less prone to moisture-related defects, resulting in better overall quality for high-precision castings.
types of sand used in sand casting
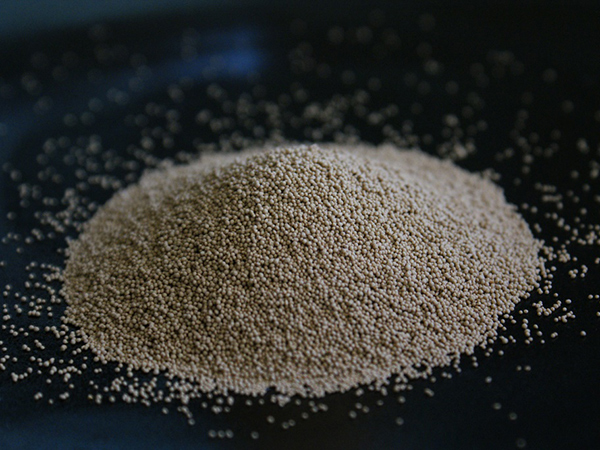
3. Nobake Sand Nobake sand, also known as cold box sand, is a mixture of silica sand and a thermosetting resin binder. The sand is not dampened with water; instead, the binder hardens when subjected to heat, creating a strong and durable mold. Nobake sand is particularly useful for complex geometries and can be used to produce high-quality castings with exceptional dimensional accuracy. This type of sand is commonly employed in the production of parts for the automotive and aerospace industries.
4. Shell Sand Shell sand casting utilizes a mixture of fine sand coated with a thermosetting resin. This sand is heated in a pattern to form a thin shell mold that is strong yet lightweight. Shell sand molds are noted for their excellent surface finish and dimensional accuracy, making them ideal for producing intricate and detailed components. The shell mold technique is often used in industries where high precision is necessary.
5. Ceramic Sand Ceramic sand, made from zircon or other ceramic materials, is sometimes utilized for sand casting, especially when casting high-temperature metals. This type of sand withstands higher temperatures than traditional silica sand, making it suitable for applications involving molten metals like titanium or superalloys.
In conclusion, the choice of sand in the casting process significantly influences the efficiency and quality of the final product. From green sand to ceramic sand, each type serves specific needs in different industries, thereby enhancing the versatility of sand casting as a manufacturing method. Understanding these options allows manufacturers to achieve optimal results based on their production requirements.
Post time:Ноя . 03, 2024 11:18
Next:foundry sand in concrete