Sand Casting of Steel An Overview
Sand casting, one of the oldest and most widely used metal casting processes, has proven its efficacy and versatility in manufacturing complex metal components. The technique employs sand as a primary mold material, allowing for the production of intricate shapes and large parts. Among various metals, steel is a popular choice due to its strength, ductility, and ability to withstand high temperatures. In this article, we will explore the sand casting process for steel, its benefits, challenges, and applications.
The Sand Casting Process
The sand casting process involves several key steps pattern making, molding, pouring, and finishing.
1. Pattern Making The first step in sand casting is the creation of a pattern that replicates the final product. The pattern is typically made of materials such as wood, metal, or plastic, and it must account for the shrinkage that occurs as the molten steel cools and solidifies. The design of the pattern plays a crucial role in ensuring that the final cast component meets the desired specifications.
2. Molding Next, the pattern is placed in a sand mold. The sand used in the molding process is usually a mixture of silica sand, clay, and water, forming a malleable yet stable mold. The sand is packed around the pattern to create a hollow cavity that mirrors the shape of the desired part. After the pattern is removed, a two-part mold (cope and drag) may be assembled to facilitate pouring the molten steel.
3. Pouring Once the mold is prepared, molten steel is poured into the cavity. Steel is a versatile alloy, and choosing the right composition is critical for the application requirements. The pouring process must be carefully controlled to avoid defects such as cold shuts or sand inclusions, which can compromise the integrity of the final product.
4. Finishing After the molten steel has cooled and solidified, the mold is broken apart to reveal the cast component. The finishing stage involves cleaning, machining, and surface treatment to remove any imperfections and prepare the part for its intended use. This may include processes such as grinding, polishing, or coating, depending on the specifications.
Benefits of Sand Casting Steel
Sand casting offers several advantages, particularly when it comes to steel components
- Cost-Effective The process is relatively low-cost compared to other casting methods, especially for low to medium production volumes. The materials required (sand and binder) are inexpensive, and the equipment needed is generally less complex.
- Versatility Sand casting can accommodate a wide range of steel grades, including carbon steels, alloy steels, and stainless steels. This versatility allows for the creation of a variety of parts, from small intricate components to large structural elements.
- Complex Shapes Due to the flexibility of sand molds, intricate geometries can be achieved. This is particularly beneficial in industries such as automotive and aerospace, where complex shapes are often required.
sand casting steel
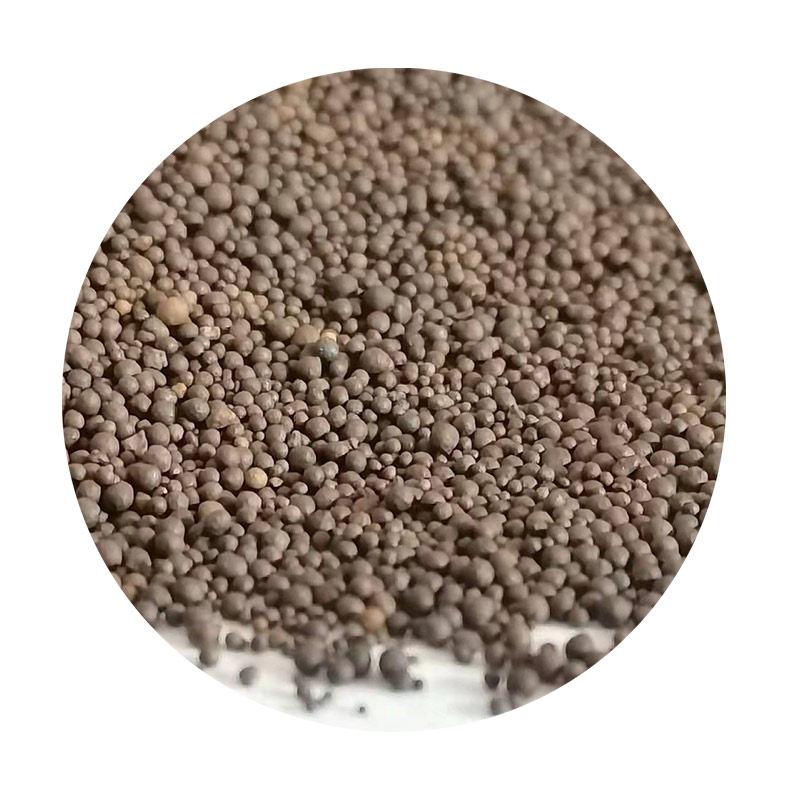
- Large Size Capability Sand casting is well-suited for producing large components that may be difficult or impossible to manufacture using other methods. This makes it a preferred choice for industries that require large steel parts, such as engine blocks or heavy machinery components.
Challenges of Sand Casting Steel
Despite its advantages, sand casting steel does come with certain challenges
- Surface Finish The surface finish of sand-cast components may not be as smooth as those produced by other methods, such as die casting or investment casting. This can necessitate additional machining, which may add to production costs and time.
- Defects Common defects in sand casting, such as gas porosity, shrinkage, and sand inclusions, can affect the mechanical properties of the final product. Thorough quality control and process optimization are essential to minimize these risks.
- Labor-Intensive The sand casting process can be labor-intensive, particularly in the pattern-making and finishing stages. As a result, the overall process can be slower compared to more automated methods.
Applications of Sand-Cast Steel
Sand-casted steel components find applications across various industries, including
- Automotive Engine blocks, transmission cases, and various structural components are commonly produced using sand casting.
- Construction Structural steel elements, such as beams and columns, benefit from the strength of sand-cast steel.
- Aerospace Components with complex shapes, such as brackets and housings, can be effectively manufactured through sand casting.
In conclusion, sand casting of steel is a time-honored process offering versatility, cost-effectiveness, and the ability to produce complex geometries. While it presents challenges, advancements in technology and techniques continue to enhance its applications and improve the quality of sand-cast products. As industries evolve, sand casting remains a relevant and valuable method for steel component manufacturing.
Post time:Дек . 15, 2024 21:21
Next:foundry casting sand