Understanding Sand Casting Services A Comprehensive Overview
Sand casting is one of the oldest and most versatile metal casting processes used to produce a variety of components in different industries. Its enduring popularity stems from its simplicity, cost-effectiveness, and ability to create complex shapes with high precision. In this article, we will explore the intricacies of sand casting services, highlighting their applications, advantages, and the overall process involved.
What is Sand Casting?
Sand casting, also known as sand mold casting, is a manufacturing process in which molten metal is poured into a mold made of sand. The sand, mixed with a binding agent, forms a mold that can withstand the heat of the molten metal. This process is suitable for both ferrous and non-ferrous metals, including aluminum, iron, and bronze. Due to its adaptability, sand casting is widely used in industries ranging from automotive and aerospace to arts and construction.
The Sand Casting Process
The sand casting process typically involves several key steps
1. Pattern Creation A pattern, often made of wood, plastic, or metal, is created to form the shape of the final product. This pattern is slightly larger than the desired part to allow for shrinkage as the metal cools.
2. Mold Making The pattern is then pressed into a mixture of sand and a binding agent to create the mold cavity. The two halves of the mold—known as cope and drag—are typically assembled, ensuring that they fit together tightly.
3. Pouring Once the mold is prepared, molten metal is carefully poured into the cavity through a pouring basin. The metal fills the mold and takes on the shape of the pattern.
4. Cooling After pouring, the molten metal is allowed to cool and solidify. This process can take anywhere from a few minutes to several hours, depending on the thickness of the metal.
5. Mold Removal Once the metal has solidified, the sand mold is broken away to reveal the cast product. This step usually involves mechanical methods or vibration to ensure that the mold parts are removed without damaging the casting.
6. Finishing Touches The final step involves cleaning and finishing the cast product. This may include machining, painting, or surface treatment to meet specific tolerances and aesthetic requirements.
Advantages of Sand Casting Services
Sand casting offers numerous benefits that make it an attractive option for manufacturers
sand casting services
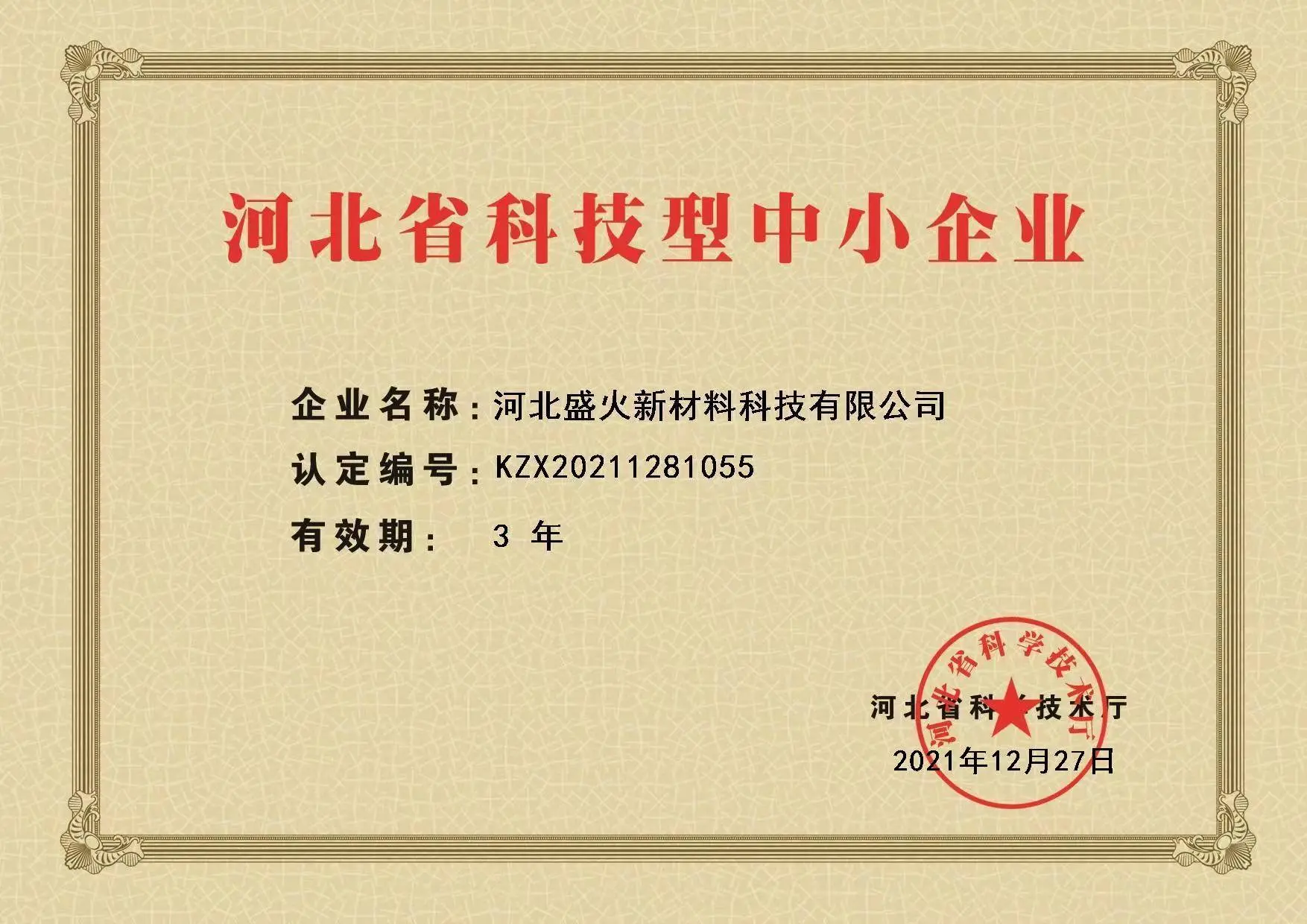
- Cost-Effective Compared to other casting methods, sand casting is relatively inexpensive
. The materials used, primarily sand, are readily available and low-cost.- Flexibility Sand casting can accommodate a wide range of metal alloys and allows for the casting of both small and large components. This flexibility makes it popular for producing unique and complex designs.
- Large Production Volumes Companies can use sand casting to produce parts in large volumes, making it suitable for mass production.
- Short Lead Times The process allows for quick prototyping and lead times, enabling manufacturers to get products to market faster.
- Excellent Surface Finish While the surface finish may vary, advances in sand casting techniques allow for improved surface quality, which can often reduce the need for extensive machining.
Applications of Sand Casting
Sand casting is utilized in various sectors, including
- Automotive Industry Many engine blocks, transmissions, and structural components are produced using sand casting due to its strength and durability.
- Aerospace Components like brackets, supports, and housings are often made via sand casting, as they require high precision and quality.
- Heavy Machinery Sand casting is commonly used to manufacture parts for heavy machinery, such as gears, frames, and housings.
- Artistic Items Beyond industrial applications, sand casting is also employed in creating sculptures, fashion accessories, and decorative items.
Conclusion
Sand casting services play a vital role in modern manufacturing, offering flexibility, cost-effectiveness, and the ability to create high-quality components. Understanding this process and its advantages can help businesses make informed decisions about their production needs. Whether you are in the automotive, aerospace, or artistic sectors, leveraging sand casting can serve as an effective solution for bringing your designs to fruition. As the industry continues to evolve, advancements in sand casting technology will further enhance its capabilities, making it an enduring choice for manufacturers worldwide.
Post time:Ноя . 30, 2024 00:35
Next:Techniques for Achieving a Smooth Finish with Clear Resin Using Sanding Methods