Sand Casting Metal Process An Overview
Sand casting is one of the oldest and most versatile metal forming processes in manufacturing. Utilizing sand as the primary molding material, this method has been widely used across many industries due to its simplicity, cost-effectiveness, and ability to produce complex metal parts. The following discussion provides insights into the sand casting process, its advantages, applications, and the fundamental techniques involved.
The Sand Casting Process
The sand casting process begins with the creation of a mold. A pattern, typically made from metal, wood, or plastic, is crafted to the desired shape of the final product. This pattern is then placed in a mold box and surrounded by a mixture of sand and binding agents, which can include clay and water. The combination of these materials creates a mold that can withstand the extreme temperatures of molten metal.
After the mold is prepared, the pattern is removed, leaving a cavity in the sand that maintains the shape of the desired cast part. This cavity is then filled with molten metal, which is poured from a ladle. The pouring process must be controlled carefully to prevent defects such as air pockets or inclusions. After the metal has cooled and solidified, the sand mold is broken away to retrieve the cast component.
Key Techniques in Sand Casting
There are various techniques within sand casting that enhance the quality and efficiency of the process
1. Green Sand Casting This is the most common sand casting method, where the sand is damp and contains clay as a binder. The moisture in the sand helps to strengthen the mold, making it ideal for intricate designs.
2. Dry Sand Casting In this method, the sand is mixed with a binder and heated, which helps to create a stronger mold. Dry sand casting is often used for larger parts that require more durability during the pouring process.
3. Investment Casting Also known as lost-wax casting, this technique involves creating a wax pattern that is coated with a ceramic material. Once the ceramic hardens, the wax is melted away, and molten metal is poured into the mold. Although it is not strictly sand casting, investment casting shares similarities and can produce highly detailed parts.
sand casting metal process
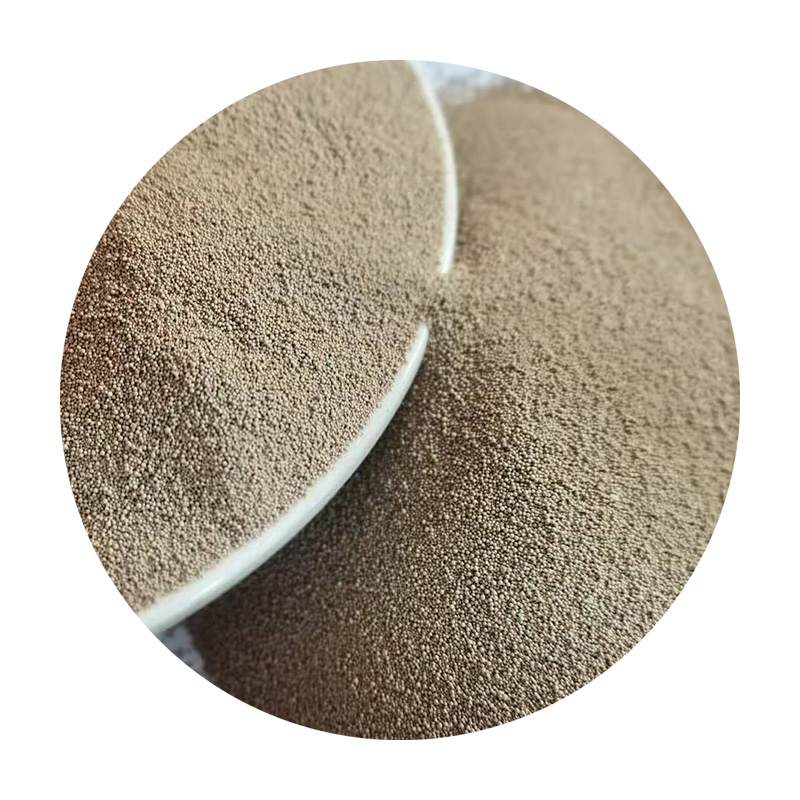
4. Shell Molding This process uses a thin shell of sand and resin to create the mold. The shell is stronger and more accurate than traditional sand molds and is particularly advantageous for parts with complex geometries.
Advantages of Sand Casting
The sand casting process offers several advantages that make it a preferred choice in many applications
- Cost-Effectiveness The materials used in sand casting are relatively inexpensive, allowing for low production costs, especially when manufacturing large or complex components. - Versatility Sand casting can accommodate a wide range of metals, including iron, aluminum, and various alloys, making it applicable in multiple industries, from automotive to aerospace.
- Complex Geometries The flexibility of sand allows for intricate designs and shapes, which would be difficult or impossible to achieve with other manufacturing processes.
- Scalability Sand casting can be used for both small production runs and large-scale manufacturing, making it adaptable to changing market demands.
Applications of Sand Casting
Sand casting is employed in a diverse range of industries. In the automotive sector, it is commonly used to produce engine blocks, cylinder heads, and various structural components. In aerospace, sand casting can create lightweight yet strong components for aircraft. Additionally, it is used in the production of machinery parts, art sculptures, and tooling applications.
Conclusion
In conclusion, the sand casting metal process is a time-honored manufacturing technique that continues to prove invaluable in today’s industrial landscape. Its ability to produce high-quality components with complex designs at a competitive cost makes it a prominent choice for manufacturers worldwide. As technology advances, innovations within the sand casting process are likely to enhance its efficiency and effectiveness, further solidifying its place in modern manufacturing practices. Whether used for prototyping or high-volume production, sand casting remains an essential method for producing metal parts across various industries.
Post time:Дек . 20, 2024 17:02
Next:sanding machine 3d print