Sand Casting Mass Production A Time-Tested Manufacturing Technique
Sand casting is one of the oldest and most widely used metal casting processes, known for its versatility and cost-effectiveness. It is especially favored in mass production settings due to its ability to produce large quantities of complex metal parts in a relatively short timeframe. This article explores the principles of sand casting, its advantages, innovations in mass production, and applications across various industries.
The Process of Sand Casting
The sand casting process begins with the creation of a mold, which is typically made from a mixture of sand, clay, and water. The sand is packed around a pattern that represents the object to be cast, forming the mold cavity. Once the pattern is removed, molten metal is poured into the mold, filling the cavity and taking the shape of the desired part. After cooling, the sand mold is broken away, revealing the finished casting.
The typical steps in sand casting include
1. Pattern Making The pattern is usually made from materials such as wood, metal, or plastic. It serves as a replica of the final product and is crucial for the accuracy of the casting.
2. Mold Preparation The sand mixture is compacted around the pattern to create a mold. This step may include the use of mechanical molding machines to ensure uniformity and reduce labor costs.
3. Melting and Pouring Specific metals are chosen based on the application. The metal is melted in a furnace and poured into the mold.
4. Cooling and Solidification After pouring, the metal cools and solidifies into the shape of the mold. This process can vary in duration depending on the size and complexity of the part.
5. Finishing After solidification, excess sand is removed, and the casting is cleansed. Additional finishing processes may include machining, grinding, or polishing to achieve the final specifications.
Advantages of Sand Casting in Mass Production
sand casting mass production
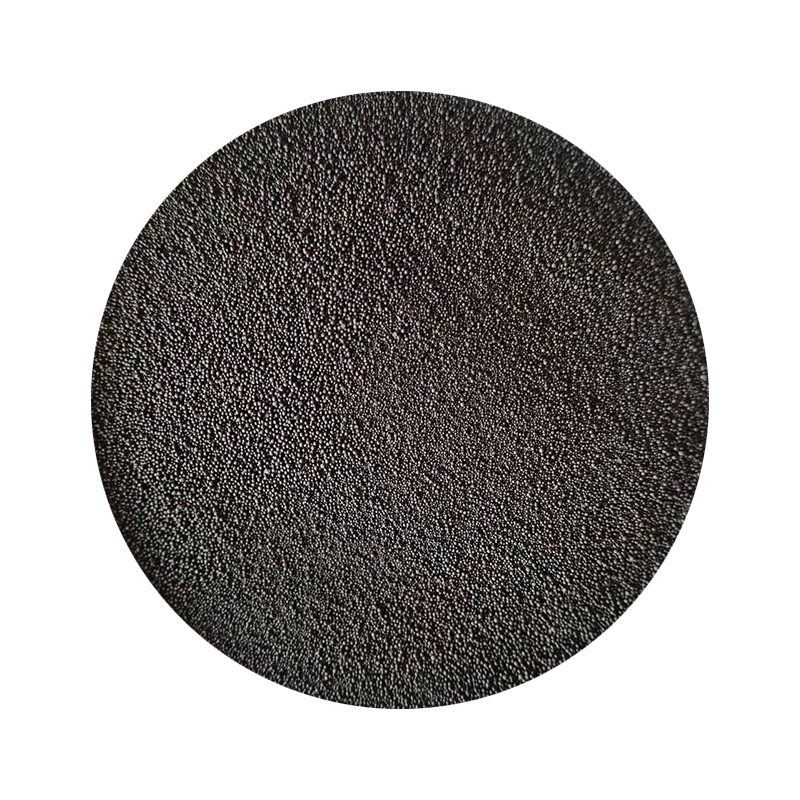
One of the major advantages of sand casting is its low cost, particularly when compared to other casting methods such as die casting or investment casting. The materials used are inexpensive, and the process can be scaled efficiently for large production runs.
Another benefit is the flexibility that sand casting offers in terms of design. Since the molds are made from sand, they can accommodate intricate designs and complex geometries. This capability makes sand casting suitable for a wide range of applications, from automotive components to intricate artistic sculptures.
Additionally, sand casting is highly adaptable to different types of metals, including aluminum, iron, copper, and magnesium alloys. This adaptability allows manufacturers to select materials best suited for their specific requirements.
Innovations in Mass Production
Recent advancements in technology have further enhanced sand casting's efficiency in mass production. Automation and computer numerical control (CNC) technologies have streamlined the mold-making process, increasing precision and reducing lead times. Moreover, 3D printing is being integrated into sand casting to create more complex molds and reduce the need for traditional pattern making.
Sustainability has also become a focus in modern sand casting practices. Efforts are being made to recycle used sand and reduce waste, thereby minimizing the environmental impact of the process.
Applications Across Industries
Sand casting is prevalent in various industries including automotive, aerospace, marine, and manufacturing. It is often used to produce engine blocks, transmission housings, and other critical components that demand precision and durability. Additionally, artistic industries utilize sand casting techniques to create sculptures and functional art pieces, showcasing the versatility of this method.
Conclusion
In conclusion, sand casting remains a cornerstone of mass production due to its cost-effectiveness, versatility, and adaptability to various metals and designs. As technological advancements continue to evolve the process, sand casting is set to maintain its relevance in the manufacturing landscape, meeting the demands of modern industries while paving the way for sustainable practices. Ultimately, its enduring legacy and continuous innovation ensure that sand casting will remain a vital part of metal fabrication for years to come.
Post time:Дек . 16, 2024 18:59
Next:difference between die casting and sand casting