Sand Casting of Cast Iron An Overview
Sand casting is one of the most traditional and widely used methods of producing metal components, particularly for cast iron. This technique involves creating a mold from a sand mixture to shape molten metal into a desired form. The simplicity and adaptability of the sand casting process make it a preferred choice for many industries, especially those dealing with cast iron.
The Process of Sand Casting
The sand casting process begins with the preparation of the mold. This typically involves a mixture of sand, clay, and water to create a bonding agent. The custom blend of materials allows for flexibility, durability, and the ability to produce intricate designs. The pattern, which is an exact replica of the final product, is embedded in the sand, creating a cavity into which molten iron will be poured.
The pattern is usually made from materials like wood, aluminum, or plastic. Once the pattern is in place, the sand is compacted around it to form a mold shell. After the mold is formed, the pattern is removed, leaving behind a precise cavity. This step is crucial, as any imperfections in the mold can translate into flaws in the final casting.
The next phase involves melting the cast iron. Cast iron, known for its excellent fluidity and ability to retain shape, is melted in a furnace at temperatures exceeding 1200 degrees Celsius (2192 degrees Fahrenheit). The molten metal is then poured into the mold cavity, filling the space and taking the shape of the pattern.
Once the metal has cooled and solidified, the mold is broken away to reveal the casting. This process often requires the use of tools to carefully separate the sand from the cast piece. The finished casting may then undergo additional processes such as cleaning, machining, or surface treatment to achieve the desired specifications.
Advantages of Sand Casting Cast Iron
sand casting cast iron
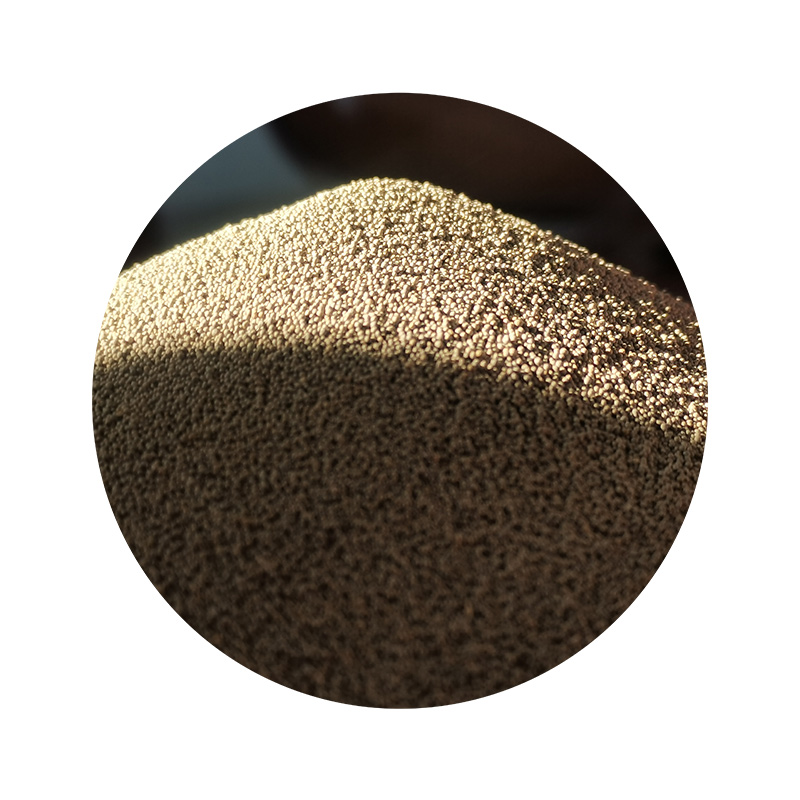
Sand casting offers several advantages, particularly for producing cast iron components. First and foremost, it is an economical method for creating small to medium-sized production runs. The ability to use the same mold multiple times reduces costs per unit, making it a cost-effective solution for manufacturers.
Another advantage is the versatility of sand casting. It allows for a wide range of cast iron grades, including gray iron, ductile iron, and white iron, each offering unique properties suitable for various applications. This adaptability also extends to the size and complexity of the castings produced, catering to everything from simple shapes to intricate designs.
The sand casting process also provides excellent dimensional accuracy and surface finish, especially when combined with modern technologies such as 3D printing for pattern making. The ability to produce highly detailed features without extensive machining further enhances its appeal.
Applications of Sand Casting for Cast Iron
The applications of sand casting in the production of cast iron parts are vast. Common applications include automotive components such as engine blocks, transmission cases, and brake components. Cast iron is also prevalent in the manufacturing of various machinery parts, pipes, and fittings, as well as artistic sculptures and architectural elements.
Moreover, the durability and excellent wear resistance of cast iron make it an ideal material for heavy-duty applications. Its ability to withstand high stress and high temperatures ensures reliability in a variety of industrial contexts.
Conclusion
In conclusion, sand casting remains a cornerstone method in the production of cast iron components due to its economical, versatile, and effective nature. As industries continue to evolve, the integration of new technologies with traditional sand casting practices promises to enhance its capabilities, making it an enduring choice for manufacturers worldwide. Whether for small-scale projects or large industrial applications, sand casting of cast iron is poised to remain a vital part of modern metalworking.
Post time:Окт . 19, 2024 21:37
Next:advantages and disadvantages of sand casting process