Sand Casting Components An Overview
Sand casting is a widely used metal casting process that involves creating metal parts by pouring molten metal into a mold formed from sand. This technique is particularly valued for its versatility, affordability, and the ability to produce complex geometries. Several key components play a significant role in the sand casting process, each contributing to the overall efficiency and quality of the final product.
1. Patterns A pattern is a replica of the final product and is used to create the mold cavity. Patterns can be made from various materials, including wood, metal, or plastic, depending on the complexity and size of the casting. They can either be single-piece patterns or multi-piece patterns, where different sections are created and assembled to form the complete shape. The choice of pattern material and design influences the accuracy and surface finish of the metal casting.
Sand Casting Components An Overview
3. Cores Cores are used when hollow sections or internal cavities are needed in the casting. Made from sand and bound with a resin or other materials, cores are placed in the mold before pouring the molten metal. This allows for the creation of more complex shapes that cannot be achieved through the mold alone. Proper core design and placement are crucial for ensuring that the final casting meets design specifications.
sand casting components
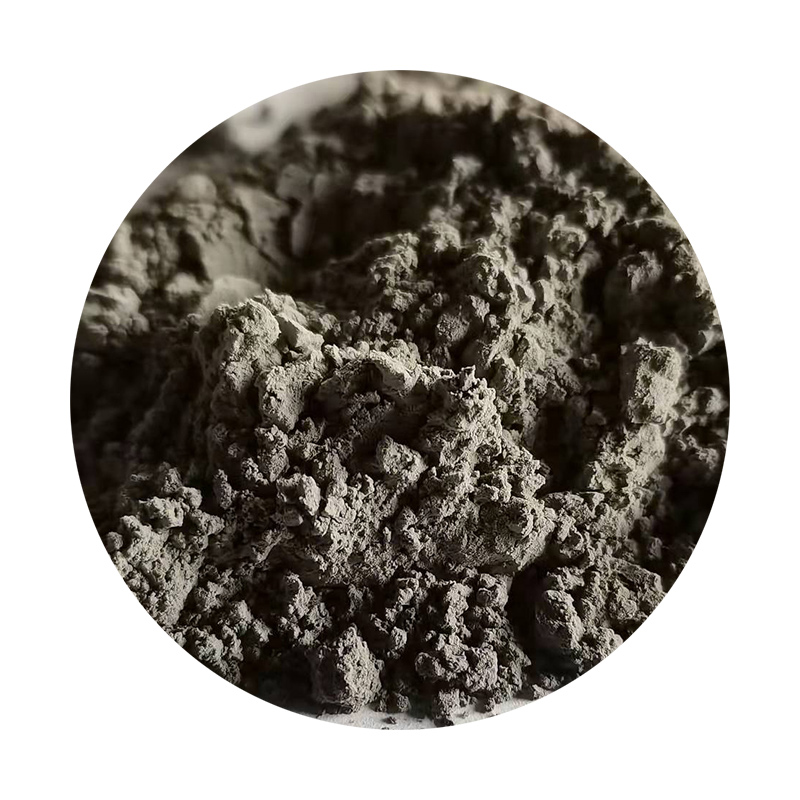
4. Pouring System The pouring system encompasses the components that direct molten metal from the ladle into the mold cavity. This includes the pouring basin, sprue, and runner. The design of this system is vital for controlling the flow of metal and minimizing defects such as air entrapment or turbulence during pouring. Effective pouring techniques help to achieve high-quality surface finishes and dimensional accuracy in the final product.
5. Cooling and Solidification Once the molten metal is poured into the mold, it must cool and solidify before being removed. The cooling rate can significantly affect the microstructure and mechanical properties of the casting. Different metals cool at different rates, and factors such as mold material and environmental conditions can influence this process. Understanding the cooling and solidification behavior of the particular metal being cast is essential for producing strong and durable components.
6. Finishing After the casting has solidified, the mold is broken apart to reveal the cast part. However, additional finishing processes such as sand blasting, machining, and heat treatment may be necessary to achieve the desired surface finish, dimensional accuracy, and mechanical properties. Often, castings require post-processing to meet stringent specifications required for various applications.
In conclusion, sand casting remains a fundamental method in manufacturing, providing a cost-effective solution for producing intricate metal components. Understanding the various components involved—patterns, molds, cores, pouring systems, cooling, and finishing—helps to optimize the sand casting process, ensuring high-quality and reliable products that meet industry standards.
Post time:Сен . 07, 2024 06:52
Next:Advanced 3D Sand Printing Casting Solutions