High Volume Sand Casting An Overview
High volume sand casting is a widely utilized manufacturing process known for its efficiency and versatility in producing metal components. This technique is particularly prominent in industries requiring large quantities of cast parts, such as automotive, aerospace, and heavy machinery. The process employs sand as the primary molding material, which allows for the production of intricate designs and geometries while maintaining effective cost-efficiency.
The Process of Sand Casting
The sand casting process begins with the creation of a mold. First, a pattern, usually made of metal or plastic, is produced to the exact dimensions of the desired part. This pattern is then placed into a mixture of sand and a bonding agent, which is typically clay and water. The sand is compressed around the pattern to form a mold cavity. After the pattern is removed, two halves of the mold are assembled, creating a hollow space that reflects the shape of the final product.
Metal is melted in a furnace and poured into the mold, filling the cavity defined by the sand mold. Once the metal cools and solidifies, the sand mold is broken apart, and the cast part is extracted. This method is capable of producing complex shapes and large components, making it ideal for high-volume requirements.
Advantages of High Volume Sand Casting
One of the main advantages of high volume sand casting is its cost-effectiveness. The materials involved—primarily sand—are low-cost and readily available. Furthermore, the process can be automated for high-volume production, significantly reducing labor costs.
high volume sand casting
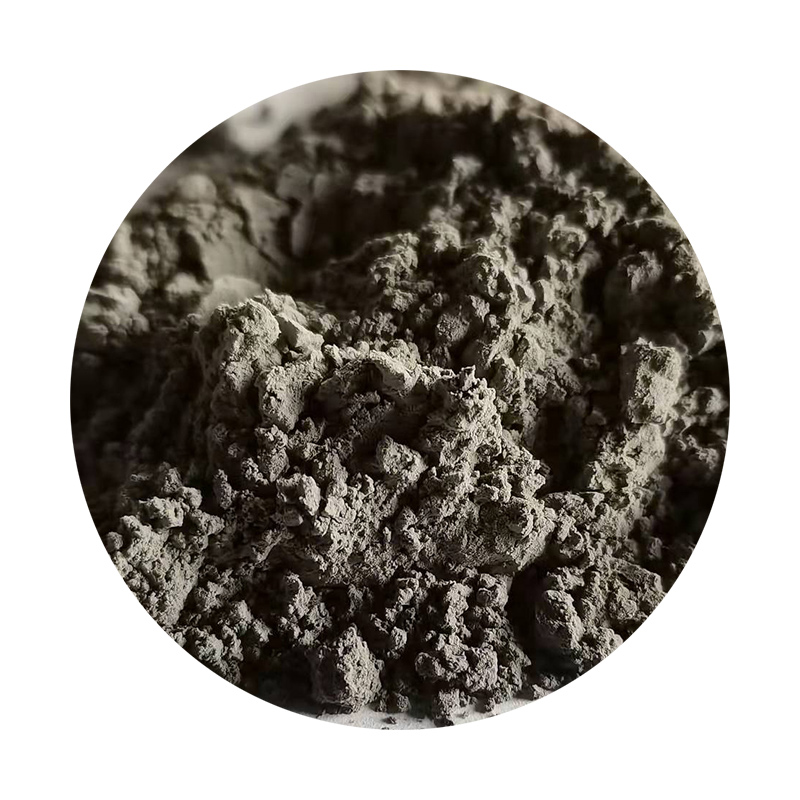
Another significant benefit is the design flexibility that sand casting offers. It can accommodate a wide range of metal alloys, including aluminum, iron, magnesium, and bronze. This versatility allows manufacturers to select materials based on the specific mechanical properties required for the finished part.
Additionally, sand casting is capable of producing components with excellent surface finishes and dimensional accuracy, especially when using advanced techniques such as 3D printing for creating molds. This contributes to reducing the need for additional machining processes, which can save time and further decrease costs.
Applications of High Volume Sand Casting
The applications for high volume sand casting are extensive. In the automotive industry, components such as engine blocks, transmission cases, and various brackets are produced using this method. In aerospace, sand casting is employed to manufacture structural components, landing gear parts, and engine casings that must adhere to strict specifications and safety standards.
Moreover, the heavy equipment sector benefits from sand casting, producing parts such as housing, frames, and various machine components. The durability and strength of sand-cast items ensure that they can withstand the rigorous demands of heavy-duty applications.
Conclusion
In summary, high volume sand casting is an essential manufacturing process that combines cost efficiency with design versatility. Its ability to produce large quantities of high-quality cast components makes it a preferred choice in various industries, from automotive to aerospace. As technology continues to advance, including innovations in mold-making and automation, sand casting will likely remain a cornerstone in the landscape of metal manufacturing, meeting the growing demands of modern engineering and production.
Post time:Окт . 31, 2024 20:03
Next:Current Market Analysis of Resin Coated Sand Prices and Trends