Casting Sand The Unsung Hero of Foundry Processes
In the world of manufacturing, sand often takes on a role that, while perhaps not glamorous, is undeniably critical. Among the various materials used in the foundry process, casting sand is paramount. It serves as the backbone of metal casting, enabling the creation of intricate designs, precise dimensions, and a myriad of products that fuel industries ranging from automotive to aerospace. Understanding the properties and applications of casting sand can illuminate its importance in modern manufacturing.
Casting sand, primarily composed of silicon dioxide, is not just any sand. Its unique properties make it an ideal medium for the casting process. Foundries typically use two main types of sand green sand and resin-bonded sand. Green sand, which contains a mixture of sand, clay, and water, is prized for its ability to maintain moisture and its capacity to hold shape. This makes it particularly effective for creating molds in which molten metal can be poured.
Resin-bonded sand, on the other hand, involves the addition of synthetic resin, which, when heated, binds the sand grains together more permanently. This method allows for greater detail in the castings and is often preferred for producing items that require finer finishes or more complex geometries. While green sand remains a staple in traditional foundries, the versatility and precision of resin-bonded sand have led to its increased adoption in various industries.
One of the key advantages of casting sand is its recyclability. Unlike many materials used in manufacturing, sand can be reused multiple times without significant degradation of its properties. This not only reduces waste but also contributes to cost efficiency within the foundry. The sand that has been used to create molds can be reclaimed, processed, and reintroduced into the casting cycle. This closed-loop system is not only economically advantageous but also reflects the increasing trend towards sustainable practices in manufacturing.
casting sand
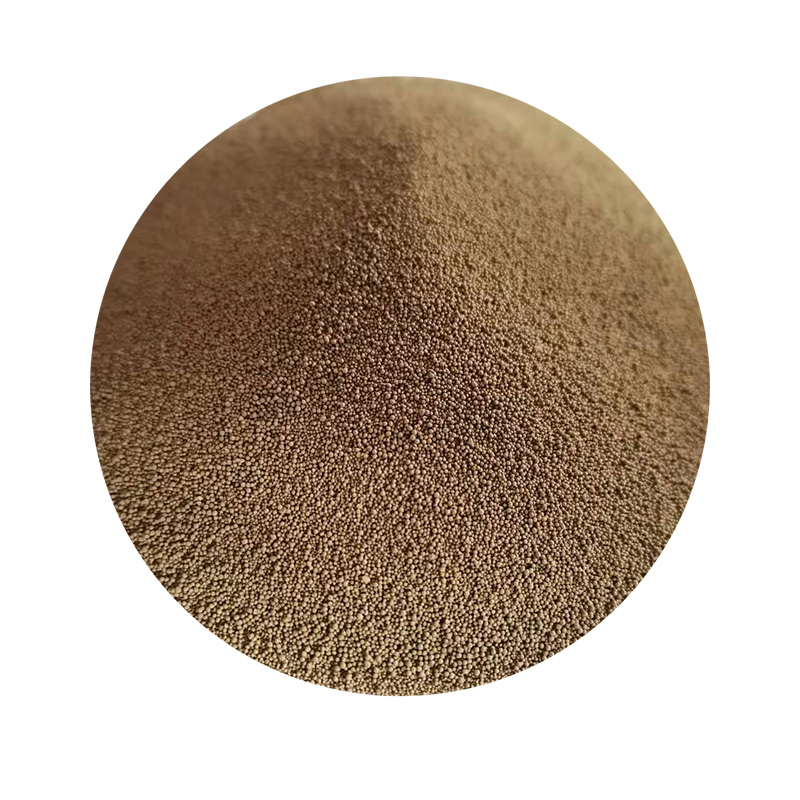
Moreover, the adaptability of casting sand to different casting methods—such as sand casting, lost foam casting, and shell molding—makes it a versatile choice for manufacturers. Each method uses sand differently, but the end goal remains the same to produce high-quality metal parts with precision. Sand casting, for instance, allows for large molds, making it suitable for producing sizable components such as engine blocks or machine frames. In contrast, shell molding allows for thin-walled sections and finer detail, showcasing the flexibility of this seemingly simple material.
The properties of casting sand also play a pivotal role in determining the quality of the final product. Factors such as grain size, shape, and distribution can significantly impact the casting process and the characteristics of the resulting metal. For instance, finer grains can produce smoother finishes, while coarser sands may enhance the strength of the mold. Foundries must carefully select and prepare their sand to ensure optimal performance, closely monitoring these variables throughout the production process.
In addition to its practical applications, casting sand also highlights the innovation within the field of materials science. Researchers are continually exploring ways to enhance the performance of sand-based casting systems, whether through the development of new bonding agents, the incorporation of additives to improve flowability or the use of alternative materials to create eco-friendly sand variants.
In conclusion, while casting sand may not garner the same attention as advanced alloys or high-tech machinery, its role in the manufacturing process is indispensable. Whether driving the production of everyday items or facilitating complex engineering solutions, casting sand serves as the unsung hero in the world of foundries. As industries continue to evolve, the ongoing development and optimization of casting sands will undoubtedly play a vital role in shaping the future of manufacturing.
Post time:Янв . 02, 2025 08:17
Next:ceramic foundry sand