Advantages of Lost Foam Casting
Lost foam casting is a unique and innovative manufacturing process that has gained popularity in various industries due to its numerous advantages. This method, which involves creating a foam pattern that is coated with a refractory material and then filled with molten metal, offers several benefits over traditional casting methods.
Advantages of Lost Foam Casting
Another key benefit is the reduction in machining requirements. The lost foam casting process produces parts that often have a near-net shape, meaning they closely approximate the final dimensions and surface finish needed. As a result, there is less need for secondary machining operations, which saves time and reduces production costs. This efficiency is particularly valuable in industries where precision and rapid turnaround times are essential.
advantages of lost foam casting
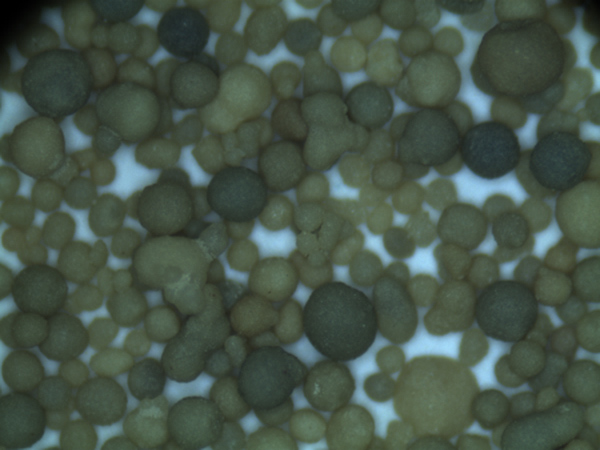
The lost foam process also enhances material efficiency. The foam used as a pattern is typically made from polystyrene, which is lightweight and can be easily molded. When the molten metal is poured into the mold, the foam evaporates, leaving behind a cavity that precisely mirrors the shape of the original pattern. This means less waste, as there are fewer by-products, and the overall material usage is optimized.
Moreover, lost foam casting allows for better control over the casting process, resulting in higher-quality products. The method supports the production of a wide range of materials, including aluminum, cast iron, and various alloys, with reduced porosity and improved mechanical properties. Additionally, because the process can be performed in an environment where temperature and other variables can be controlled, manufacturers can achieve consistent results batch after batch.
Environmental considerations also play a role in the appeal of lost foam casting. The process minimizes waste and can utilize recycled materials in the foam pattern, contributing to sustainable manufacturing practices. Furthermore, the reduced need for machining decreases energy consumption and the carbon footprint associated with production.
In conclusion, lost foam casting presents numerous advantages that enhance both the efficiency and quality of manufacturing processes. With the ability to create complex shapes, reduce material waste, minimize machining needs, and improve environmental sustainability, it is no wonder this method continues to be embraced by industries worldwide. As technology advances, the applications and benefits of lost foam casting are likely to expand even further, solidifying its place as a preferred casting technique.
Post time:Ноя . 14, 2024 14:48
Next:resin sand casting process