The Process and Advantages of 3D Sand Casting
In the realm of manufacturing, technology advancements have continuously revolutionized traditional methods. One such innovation is 3D sand casting, a technique that has significantly transformed the foundry industry. This process marries the age-old practice of sand casting with modern 3D printing technologies, resulting in enhanced efficiency, precision, and creativity.
The Basics of Sand Casting
Sand casting is a manufacturing process wherein a mold is created using sand. The sand is mixed with a binding agent and then shaped into the desired form. Once the mold is prepared, molten metal is poured into it, allowed to cool and solidify, then the sand is removed to reveal the final product. Traditional sand casting methods, while effective, can be time-consuming and require extensive labor, making them less suitable for rapid prototyping and complex designs.
Introduction of 3D Printing to Sand Casting
With the advent of 3D printing technology, foundries have begun integrating this method into sand casting processes. This technique involves using 3D printers to create molds directly from digital designs, significantly reducing the time required for mold production. Unlike traditional sand casting, which may take days to create suitable molds, 3D sand casting can produce high-quality molds in hours, if not minutes.
Advantages of 3D Sand Casting
3d sand casting
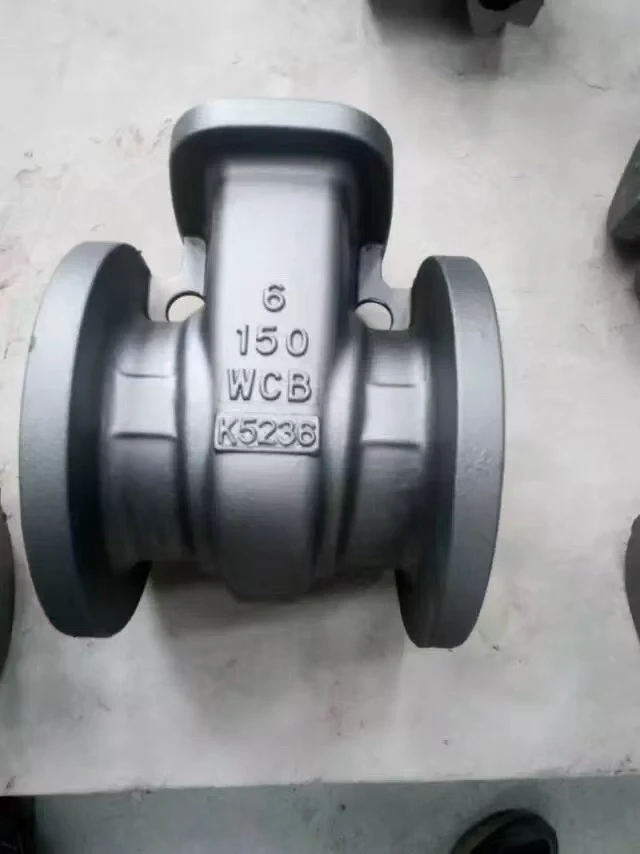
1. Precision and Detail One of the most significant benefits of 3D sand casting is the high level of precision it offers. 3D printers can create intricate designs that traditional methods struggle to replicate. This precision ensures that every detail is captured faithfully, resulting in intricately designed components that meet strict specifications.
2. Reduced Material Waste Traditional mold-making processes often generate a considerable amount of waste material, especially when refining prototypes. 3D sand printing minimizes waste by using only the necessary amount of material, thus promoting a more sustainable manufacturing approach. The capability to reuse sand powder also contributes to reducing environmental impact.
3. Expedited Production Time The speed of production is another primary advantage of 3D sand casting. Since molds can be produced quickly and with less manual intervention, the overall timeline from design to finished product is significantly shortened. This efficiency is particularly beneficial for industries that require rapid prototyping or low-volume production runs.
4. Complex Geometries and Lightweight Designs The 3D printing process allows for the creation of complex geometries that are often impossible to achieve with traditional tooling. Designers can experiment with lightweight structures and intricate designs without the constraints posed by conventional mold-making processes. This ability enables the production of more optimized parts, reducing weight while maintaining structural integrity.
5. Customization 3D sand casting offers exceptional flexibility in product customization. Since molds can be easily designed and modified using CAD software, manufacturers can quickly adapt designs to meet specific customer requirements. Customization is particularly valuable in industries such as automotive and aerospace, where tailored solutions are essential.
Conclusion
In conclusion, the integration of 3D printing technology into the sand casting process marks a pivotal advancement in the manufacturing sector. 3D sand casting not only enhances precision and efficiency but also provides the flexibility to produce innovative designs while minimizing waste. As industries continue to evolve and demand more from manufacturing processes, 3D sand casting stands out as a forward-thinking solution that can meet contemporary challenges and drive future advancements in product design and production. This fusion of traditional techniques and modern technology exemplifies how the manufacturing industry is embracing innovation, paving the way for a more efficient and sustainable future.
Post time:Ноя . 27, 2024 09:34
Next:Exploring Techniques and Benefits of Hard Sand Casting in Manufacturing Industries