3D Printing Patterns for Sand Casting Revolutionizing Traditional Manufacturing
In the realm of modern manufacturing, the integration of 3D printing with traditional techniques has sparked a significant transformation. One such domain experiencing this shift is sand casting, a well-established method used to create metal parts. Traditionally reliant on physical patterns carved from wood or metal, sand casting is now being revolutionized through the use of 3D printing technology, enabling more efficient, precise, and customizable production processes.
Sand casting involves creating a mold from a pattern, into which molten metal is poured to form a desired shape. The traditional method requires time-consuming manual labor to produce these patterns. However, with advancements in 3D printing, manufacturers can rapidly design and create patterns with complex geometries, significantly reducing lead times. This is particularly valuable in industries like aerospace, automotive, and art, where intricate designs are often required.
3D Printing Patterns for Sand Casting Revolutionizing Traditional Manufacturing
Moreover, the precision offered by 3D printing reduces the likelihood of defects in the casted parts. Traditional pattern-making processes can introduce errors due to human factors or limitations of the tools used. In contrast, a 3D printer can replicate intricate details and achieve tighter tolerances, ensuring that patterns are produced exactly as designed. This precision is crucial for industries where even minor discrepancies can lead to significant issues in performance and safety.
3d printing patterns for sand casting
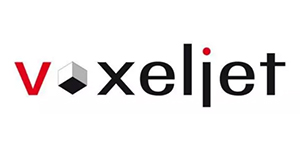
Another significant benefit is the reduction in material waste. Traditional pattern making often involves cutting away material to achieve the desired shape, resulting in a considerable amount of scrap. However, 3D printing is an additive process that builds up material layer by layer, utilizing only what is necessary to create the pattern. This not only minimizes waste but also contributes to more sustainable manufacturing practices, which are increasingly important in today’s environmentally conscious market.
Customizability is another critical factor in the adoption of 3D printed patterns. Manufacturers can easily adjust designs based on client specifications or evolving requirements. This adaptability allows for short production runs and rapid prototyping, enabling businesses to respond quickly to market changes. In addition, the ability to iterate designs without the need for new tooling can significantly enhance a company’s competitive edge.
Despite these advantages, some challenges remain. The initial investment in 3D printing technology can be substantial, and there is a learning curve associated with integrating this technology into existing workflows. Additionally, the selection of printing materials must be tailored to ensure compatibility with the casting process, as the chosen material must withstand high temperatures.
In conclusion, the integration of 3D printing with sand casting is revolutionizing how manufacturers approach pattern creation. The benefits of speed, precision, reduced waste, and customizability position 3D printed patterns as a game-changer in the manufacturing landscape. As the technology continues to evolve and become more accessible, it is likely that the adoption of 3D printing in sand casting will become increasingly prevalent, paving the way for innovative products and processes in various industries. The future of manufacturing is undoubtedly here, blending traditional techniques with cutting-edge technology to create a smarter, more efficient production line.
Post time:Ноя . 14, 2024 21:51
Next:sintered sand