The Benefits of 3D Printing a Sanding Block
In recent years, 3D printing technology has revolutionized various industries by enabling rapid prototyping and customization. One of the most intriguing applications of this technology is the creation of specialized tools, such as sanding blocks. A sanding block is an essential tool in woodworking and metalworking, used to smooth surfaces and prepare them for finishing. This article explores the advantages of using 3D printing to create sanding blocks, including customization, material efficiency, and ease of production.
Customization
One of the most significant advantages of 3D printing a sanding block is the unparalleled level of customization it offers. Traditional sanding blocks typically have fixed shapes and sizes, which may not suit every sanding application. With 3D printing, users can design sanding blocks tailored to their specific needs. For instance, a woodworker may require a block with a unique contour to sand intricate curves on a piece of furniture. By utilizing CAD (Computer-Aided Design) software, users can create personalized designs that optimize their sanding tasks, enhancing the overall quality of their projects.
Moreover, the ability to adjust dimensions, grip styles, and even add features like interchangeable sanding pads opens up opportunities for highly specialized sanding tools that can cater to various materials and finishes. This level of customization is especially beneficial for hobbyists and professionals alike, who often work on projects with specific requirements that standard tools cannot meet.
Material Efficiency
3D printing allows for more efficient use of materials, reducing waste compared to traditional manufacturing processes. When producing a sanding block through conventional methods, excess material is often cut away, leading to significant waste. However, with 3D printing, the design can be optimized to use only the necessary material, creating a more sustainable approach to tool production.
sanding block 3d print
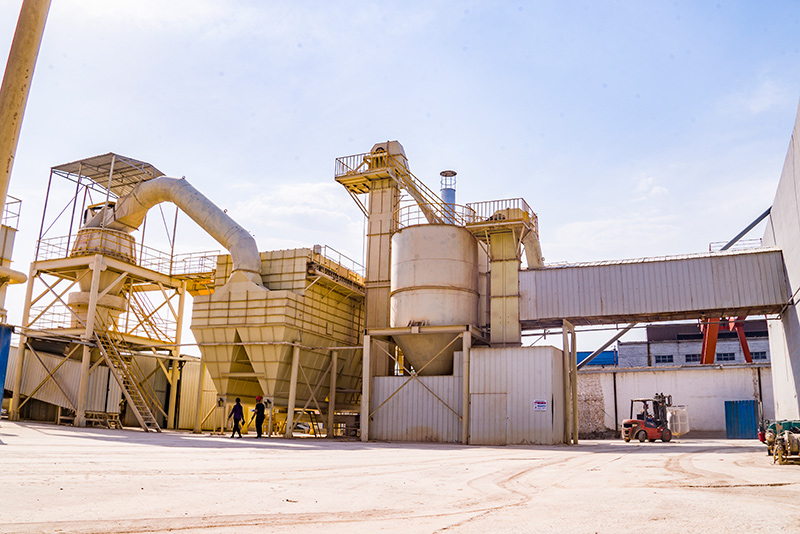
Additionally, 3D printing opens up the possibility of using a variety of filament materials, including environmentally friendly options such as biodegradable PLA (Polylactic Acid) or recycled filaments. This allows users not only to produce effective sanding blocks but also to make environmentally conscious choices in their tool manufacturing and usage.
Ease of Production
Another compelling advantage of 3D printing sanding blocks is the simplicity and speed of the production process. Traditional methods can involve complex setups, molds, or machining processes that require significant time and expense. In contrast, 3D printing allows users to produce sanding blocks in a matter of hours, directly from a digital file. Once the design is finalized, the manufacturing phase becomes an automated process that requires minimal intervention.
This efficiency is particularly valuable for small-scale workshops and individual artisans who may not have access to expensive industrial machinery. With a 3D printer, they can easily print sanding blocks on-demand, reducing inventory costs and ensuring they always have the right tools for their current projects.
Conclusion
In conclusion, the integration of 3D printing technology into the creation of sanding blocks offers numerous benefits, including enhanced customization, improved material efficiency, and streamlined production processes. As more individuals and businesses adopt 3D printing, we can expect to see an increased diversity of sanding block designs that cater to a wide array of applications. This innovation not only enhances the quality of work but also supports sustainability efforts within the industry. For anyone involved in woodworking or metalworking, exploring the realm of 3D printed sanding blocks could lead to more efficient, effective, and enjoyable crafting experiences. As technology continues to evolve, the future of toolmaking is undoubtedly bright, with possibilities limited only by one’s imagination.
Post time:Kas . 25, 2024 13:43
Next:Innovative Techniques in Hard Sand Casting for Enhanced Metal Performance and Quality