Sand Used for Sand Casting An Overview
Sand casting, one of the oldest and most widely used metal forming processes, plays an essential role in manufacturing various components used in industries ranging from automotive to aerospace. At the heart of this process is the type of sand used, which significantly influences the quality and characteristics of the final product. This article explores the significance of sand in sand casting and the different types of sands commonly used.
Sand Used for Sand Casting An Overview
Silica sand, primarily composed of silicon dioxide (SiO2), is well-regarded for its high melting point and excellent thermal resistance. It is widely available and cost-effective, making it the go-to material for many foundries. Silica sand is typically mixed with a binder, such as clay, to enhance its strength and improve the mold's integrity. The most common type of clay used in this application is bentonite, which when mixed with water, forms a plastic mass that assists in holding the grains of silica sand together.
sand used for sand casting
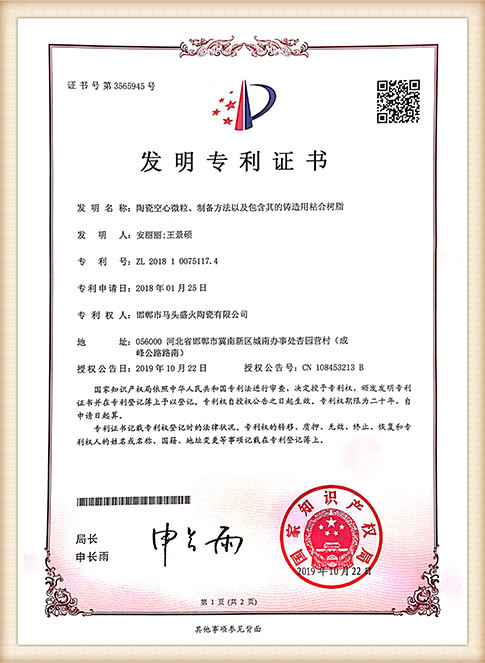
Zircon sand is another popular choice, prized for its low thermal expansion and high melting point. While more expensive than silica sand, its unique properties make it suitable for casting alloys that require high dimensional accuracy and surface finish. Zircon sand molds also have lesser impurities, which is essential when casting high-grade metal components.
Beyond the basic types of sand, other materials can be added to enhance the properties of the sand mix. Coal dust, for example, is often added to improve the surface finish of the castings. The right composition of sand, binder, and additives can make a significant difference in the performance of the final product, reducing defects such as porosity and improving the mold's ability to retain shape during the casting process.
The process of sand casting itself involves several steps pattern making, molding, pouring, and finishing. Each of these steps relies on the quality of the sand used. For instance, during the molding process, the sand must be compacted around a pattern. This requires a careful balance in the sand's moisture content to achieve optimum compaction without cracking.
In conclusion, the type of sand used in sand casting is critical to the success of the operation. Silica and zircon sands offer unique advantages, and understanding their characteristics can lead to improvements in product quality and production efficiency. As industries continue to evolve, advancements in sand technology may further enhance the capabilities of sand casting, ensuring its relevance in modern manufacturing for years to come.
Post time:Eyl . 13, 2024 03:06
Next:Szlifowanie ceramiki - Profesjonalne usługi i porady