Understanding Resin Coated Sand Specifications
Resin coated sand has revolutionized the foundry industry by providing superior casting performance compared to traditional sand molds. The development of this innovative material is primarily driven by its ability to withstand high temperatures and produce detailed finishes, which are integral to modern manufacturing processes. This article delves into the specifications of resin coated sand, highlighting its composition, properties, and applications.
At the core of resin coated sand is a base of high-quality silica sand, which is then coated with a resin binder. The resin used can vary from phenolic to furan or epoxy, each providing unique characteristics that enhance the sand's performance. The typical specification for resin coated sand includes detailed information about particle size distribution, resin type, and coating thickness. For optimal performance, the sand should have a well-defined grain size that promotes uniform packing and minimizes air voids.
One of the key specifications to consider is the *fineness of the sand grains*. Standard specifications often indicate that the sand should have a particle size ranging from 70 to 150 microns, ensuring it can capture fine details in the molds. A well-graded sand mixture will not only improve mold strength but also enhance surface finish and dimensional accuracy in the final product.
resin coated sand specification
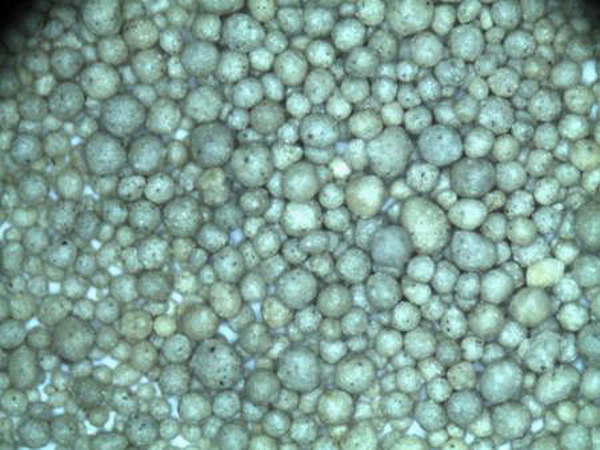
Another critical aspect of resin coated sand is its *mechanical properties*. The compressive strength and tensile strength of the molded sand significantly contribute to the casting's integrity. Typically, resin coated sand exhibits compressive strengths over 4,000 psi, making it suitable for producing intricate and large castings. Furthermore, the sand's *thermal stability* is paramount. It should maintain its integrity at temperatures exceeding 1,000°C, allowing for the casting of ferrous and non-ferrous metals without disintegration of the mold.
In addition to mechanical properties, the *chemical compatibility* of resin coated sand with various metals is an essential specification. The sand must resist chemical reactions that could occur during the casting process. For instance, interactions with molten aluminum or magnesium can lead to mold degradation, negatively affecting the final product.
Applications of resin coated sand are broad and varied. It is predominantly used in the automotive and aerospace industries for producing complex and high-performance components. The precision that resin coated sand provides is instrumental in reducing post-casting machining operations, thereby improving overall efficiency and cost-effectiveness.
In summary, the specification of resin coated sand encompasses multiple factors, including grain size, mechanical strength, thermal stability, and chemical compatibility. Understanding these specifications allows manufacturers to select the appropriate type of resin coated sand for their specific applications, ensuring quality and performance in the final castings. As industries continue to advance, the role of resin coated sand will undoubtedly remain pivotal in meeting the demands for precision engineering and quality in production processes.
Post time:Eyl . 24, 2024 17:17
Next:What Products Are Made from Sand Casting?