How to Sand Cast A Comprehensive Guide
Sand casting is a versatile and cost-effective method of metal casting, widely used in manufacturing various components and parts across multiple industries. This technique involves creating a mold from a sand mixture, and then pouring molten metal into this mold to form the desired shape. In this article, we will walk you through the process of sand casting, including its materials, steps, and some tips for success.
Materials Required
To begin with sand casting, you'll need the following materials
1. Sand The primary component, usually a mixture of fine silica sand and clay, which helps in binding the mold. 2. Pattern A replica of the object you want to cast, made from materials like wood, metal, or plastic. 3. Release Agent A substance applied to the pattern to prevent the sand from sticking to it. 4. Metal The molten metal you plan to cast, commonly aluminum, iron, or bronze. 5. Mold box A container to hold the sand and create the mold. 6. Tools Various hand tools for packing the sand, trimming excess, and pouring the metal.
Steps to Sand Cast
1. Create the Pattern The first step in sand casting is to create the pattern. This pattern should be a bit larger than the final object, accounting for shrinkage as the metal cools. Ensure it has no undercuts, as this will make it difficult to remove from the mold.
2. Prepare the Mold Place the pattern in a mold box and secure it tightly. Begin packing sand around the pattern, making sure to apply enough pressure to form a solid mold. Use a release agent on the pattern to facilitate easier removal after the sand has set.
3. Parting Line For complex shapes, you may need to create a parting line. This is done by using two mold halves to make extraction easier. Carefully lift the top half of the mold, remove the pattern, and then replace the top half, ensuring alignment.
how to sand cast
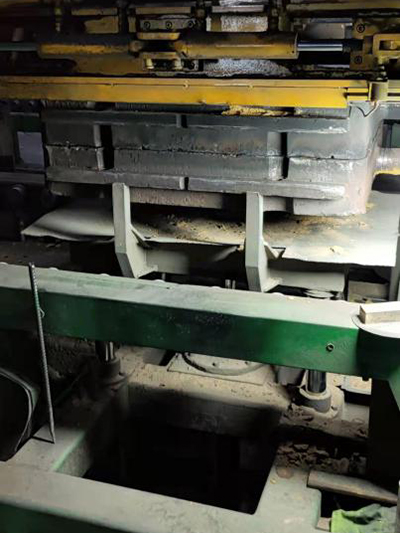
4. Add Pouring Basin Create a pouring basin on the top of the mold to pour the molten metal. This is essential for allowing the metal to flow into the cavity of the mold smoothly.
5. Mix and Melt the Metal Next, heat your chosen metal in a furnace until it reaches its melting point. It’s crucial to achieve the right temperature for the specific metal you’re working with, which ensures better flow and reduces defects.
6. Pour the Metal Once the metal is molten, carefully pour it into the mold through the pouring basin. Pour at a steady pace to minimize splashing and ensure even filling of the mold.
7. Cooling Allow the metal to cool and solidify, which may take from several minutes to hours, depending on the size and type of metal. During this time, avoid disturbing the mold to prevent unwanted defects.
8. Remove the Casting After sufficient cooling, carefully break away the sand mold and extract the casting. Handle the casting carefully to avoid damaging it.
9. Finishing Touches Finally, trim any excess metal (known as flashing) and perform any necessary finishing processes such as grinding or polishing to achieve the desired surface finish.
Tips for Success
- Quality Sand Invest in good quality sand, ideally a mixture that retains moisture without becoming too clumpy. The right sand type can significantly influence the mold quality and final casting. - Pattern Material Choose a durable pattern material; metal patterns tend to last longer than wooden ones, particularly for repeated casting. - Temperature Control Keep a close eye on the molten metal's temperature, as overheating can lead to oxidation and other issues.
In conclusion, sand casting is an ancient yet efficient method of metalworking. By following these steps and tips, you can create high-quality castings for various applications, whether for hobby projects or industrial purposes. With practice and attention to detail, you’ll soon master the art of sand casting. Happy casting!
Post time:Kas . 24, 2024 08:56
Next:density of foundry sand