High Volume Sand Casting A Comprehensive Overview
High volume sand casting is a widely utilized manufacturing process known for its efficiency and cost-effectiveness in producing large quantities of metal components. This process involves creating molds from sand, which are then filled with molten metal to produce intricate shapes and designs. With the growing demand in industries such as automotive, aerospace, and construction, understanding the intricacies of high volume sand casting becomes essential.
At the core of high volume sand casting is the preparation of the sand mold. Sand, typically mixed with a binder, is compacted around a pattern that represents the final product. The choice of sand is critical, as it must withstand high temperatures and maintain its structure during metal pouring. Commonly used sands include silica and olivine, each offering different properties suitable for various applications.
Once the mold is prepared, the next step is to pour molten metal into the cavity created by the pattern. This metal is usually aluminum, iron, or zinc, chosen for their desirable mechanical properties and availability. The pouring process must be carefully controlled to avoid defects such as air pockets or incomplete fillings. Therefore, specialized equipment and techniques, including automated pouring systems, are often employed in high-volume production environments.
After the metal has cooled and solidified, the molds are broken apart to reveal the castings. This stage is crucial as any imperfections in the mold or pouring process can lead to defects in the final product. High volume sand casting often incorporates quality control measures, including rigorous inspection protocols, to ensure that each component meets the required standards.
high volume sand casting
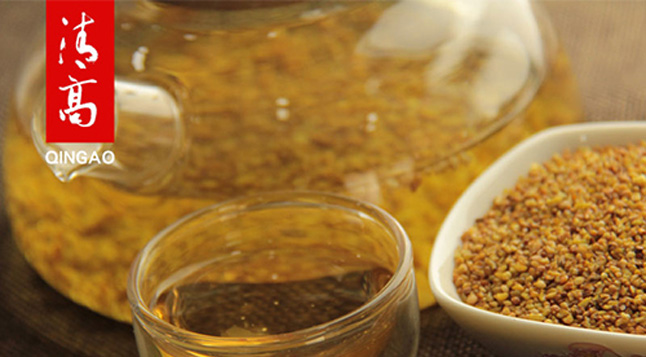
One of the significant advantages of high volume sand casting is its ability to produce complex shapes and designs with relative ease. The flexibility of the sand mold allows for intricate detailing that may be challenging to achieve with other manufacturing methods. Additionally, this process can be highly automated, which not only increases production rates but also minimizes labor costs.
The economic benefits of high volume sand casting cannot be overstated. Once the initial setup costs are covered, the cost per unit decreases significantly with increased production runs. This makes it an attractive option for industries where large numbers of identical parts are required.
However, like all manufacturing processes, high volume sand casting has its limitations. Issues such as mold wear, surface finish quality, and dimensional tolerances must be managed carefully. Continuous advancements in technology, including computer-aided design (CAD) and computer numerical control (CNC) machining, are helping to address these challenges and enhance the overall quality of castings.
In conclusion, high volume sand casting remains a vital manufacturing process, driving innovation and efficiency across various industries. By leveraging its strengths and addressing its challenges, manufacturers can continue to meet the increasing demands for quality metal components in an ever-evolving market.
Post time:Eki . 10, 2024 20:10
Next:how to cast sand in resin