Understanding Foundry Sand Properties A Comprehensive Overview
Foundry sand is a crucial material in the metal casting industry. It plays a vital role in forming molds and cores for various metal casting processes, including sand casting, which is one of the most widely used methods for producing metal parts. The properties of foundry sand directly influence the quality of castings, making it essential for foundry operations to understand and optimize these characteristics.
1. Composition of Foundry Sand
Typically, foundry sand consists of high-purity silica (SiO2), which is essential for its strength and thermal stability. Other components, such as clay and water, are often added to enhance the sand’s cohesive properties. Different types of foundry sands include
- Natural Sand Generally used for molding, it is extracted from riverbeds or quarries and often requires minimal processing. - Synthetic Sand Produced through various industrial processes and designed to have specific properties tailored for particular casting needs. - Recycled Sand Used sand that has been processed for reuse, reducing waste and production costs.
2. Key Properties of Foundry Sand
Several intrinsic properties make foundry sand suitable for casting applications
- Grain Size and Distribution The size of sand grains impacts the mold's surface finish and the flowability of the sand. A uniform grain size enhances mold strength, while a well-distributed grain size improves packing density.
- Shape and Texture The shape of sand grains affects moldability and the ability to form intricate details. Ideally, sand grains should be sub-angular to round, as these shapes provide optimum packing and strength. The texture (smooth or rough) also influences the mold's integrity.
- Thermal Conductivity Foundry sand needs to withstand high temperatures without degrading. High thermal conductivity helps dissipate heat during the solidification of molten metal, reducing defects such as misruns and cold shuts.
foundry sand properties
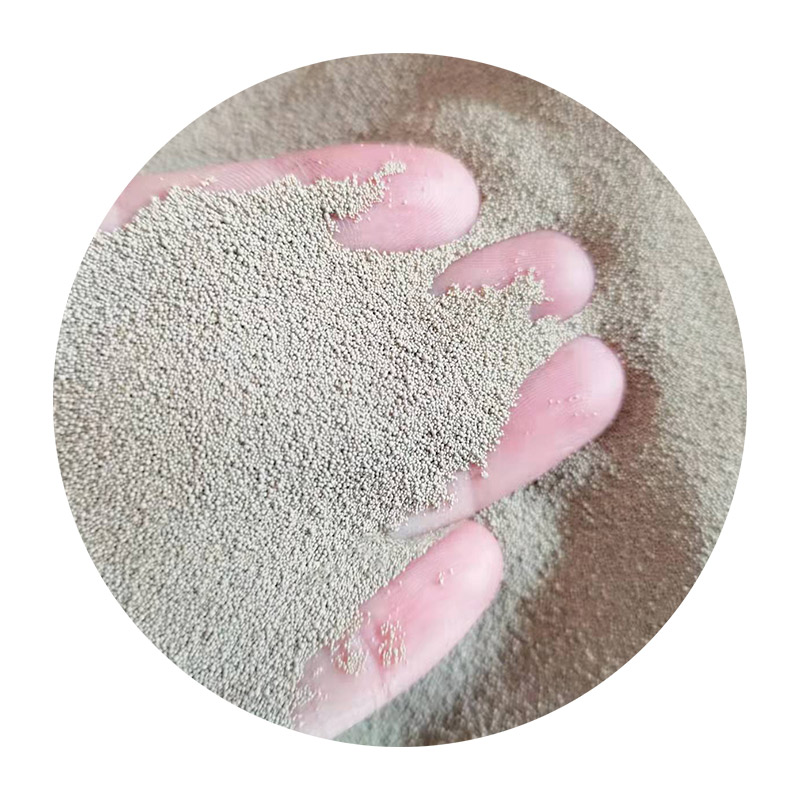
- Strength and Cohesion The ability of the sand to retain its shape under pressure is crucial. This property is influenced by the amount and type of binder used, with clay being the most common. A strong cohesive bond is necessary to withstand the weight of molten metal and external forces during the pouring process.
- Refractoriness This property refers to the sand's ability to withstand high temperatures without melting or deforming. High refractoriness is essential for preventing the sand from fusing with the molten metal.
3. Testing and Evaluation of Foundry Sand Properties
Evaluating the properties of foundry sand involves several tests
- Sieve Analysis This test determines the grain size distribution, which aids in understanding how the sand will behave in mold making.
- Moisture Content The amount of moisture in sand affects its bonding and strength; therefore, it must be carefully controlled.
- Compression Tests These tests help in assessing the strength and durability of the sand mixture under load.
- Thermal Conductivity Tests Understanding how well the sand can dissipate heat ensures that it can handle the casting process without undesirable results.
4. Conclusion
The significance of foundry sand properties cannot be overstated in the casting process. A thorough understanding of these properties enables foundry operations to achieve high-quality castings with minimal defects. By optimizing the composition and characteristics of foundry sand, manufacturers can improve casting performance, reduce costs, and enhance overall productivity. As the industry continues to evolve, ongoing research and innovation in foundry sand technology will help meet the growing demands for efficient and sustainable casting solutions.
Post time:Kas . 19, 2024 23:11
Next:lost foam casting examples