Foundry Sand Casting Process An Overview
The foundry sand casting process is one of the oldest and most widely used methods of metal casting. This versatile technique allows for the production of a broad range of metal components, from small intricate parts to large heavy-duty components used in various industries, such as automotive, aerospace, and machinery. Understanding the steps involved in the sand casting process can provide valuable insights into its efficiency and effectiveness.
The process begins with the creation of a mold. This is typically achieved by compacting sand around a pattern, which is a replica of the object to be cast. The sand is mixed with a binding agent, such as clay or resin, to enhance its cohesiveness and stability. The quality of the sand plays a crucial role in the casting process; it must retain its shape yet be easily removed after the metal has cooled. The pattern can be made from various materials, including metal, wood, or plastic, and it is essential that it is designed with proper allowances for shrinkage and drafts.
Once the mold is prepared, it is typically divided into two halves— the cope (upper half) and the drag (lower half). After removing the pattern, the mold cavities are created, and features such as gates and risers are integrated into the design. Gates allow molten metal to enter the mold, while risers provide a reservoir for metal to flow into, compensating for shrinkage as the metal solidifies.
The next step involves melting the metal to be poured into the mold. This is typically done in a furnace, where the selected metal, often aluminum, iron, or steel, is heated to its molten state. The temperature and composition of the molten metal are critical, as they dictate the final properties of the cast component, such as strength, ductility, and hardness.
foundry sand casting process
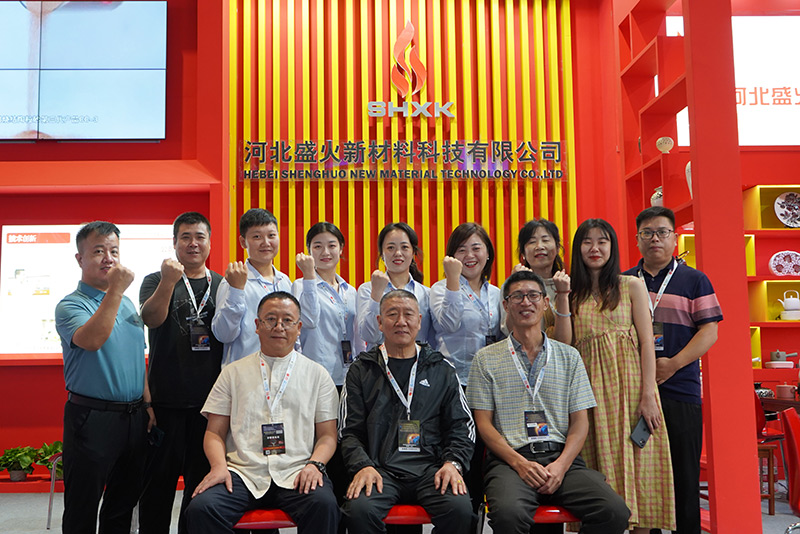
Once the metal reaches the required temperature, it is poured into the mold through the gating system. The flow of molten metal must be carefully controlled to prevent defects such as cold shuts or sand inclusion, which can compromise the integrity of the final product. After pouring, the metal is left to cool and solidify, a process that can take anywhere from a few minutes to several hours, depending on the size and thickness of the casting.
After the metal has cooled sufficiently, the next step is demolding. The sand mold is broken apart to retrieve the casting, which may require some cleaning to remove any residual sand. This is often accomplished through shaking or blasting methods, depending on the surface finish requirements.
Finally, the castings may undergo additional machining or finishing processes to achieve the desired tolerances, surface quality, and aesthetics. This could include operations like grinding, milling, or polishing.
In conclusion, the foundry sand casting process is a robust method for producing metal components with diverse applications. Its adaptability and cost-effectiveness make it a preferred choice in many manufacturing sectors. Despite the advancements in modern casting technologies, traditional sand casting remains a cornerstone of the foundry industry, showcasing the enduring relevance of this ancient technique.
Post time:Kas . 20, 2024 21:45
Next:spherical sand