The Importance of Foundry Molding Sand in Metal Casting
Foundry molding sand plays a pivotal role in the metal casting industry, serving as a crucial medium for shaping metal into complex forms. Its characteristics and quality can significantly influence the properties of the final cast product. Understanding the intricacies of molding sand, including its types, composition, and physical properties, is essential for optimizing the casting process and achieving high-quality outputs.
Composition and Types of Molding Sand
Molding sand primarily consists of silica sand, clay, water, and various additives. The primary constituent, silica sand, provides the required strength and shape retention during the casting process. Clay acts as a binder that helps to hold the sand grains together, while water is added to enhance the plasticity and workability of the mixture. Common types of molding sand include
1. Green Sand This is the most commonly used type of molding sand in foundries. It consists of a mixture of silica sand, clay, and water. Its name derives from the fact that it is used in a moist form. Green sand provides good moldability and is reusable after the casting process.
2. Dry Sand Unlike green sand, dry sand is used in a dry state. It is often employed for producing high-precision castings. Dry sand molds are more durable than green sand molds and provide better surface finishes.
3. Sodium Silicate Sand This type of sand is chemically bonded and provides excellent strength and dimensional accuracy. It is commonly used for producing complex shapes and is more environmentally friendly compared to traditional bonding agents.
4. No-Bake Sand This type of molding sand uses chemical binders that harden at room temperature. It is often utilized for making large molds, as it does not require the application of heat.
Physical Properties
foundry molding sand
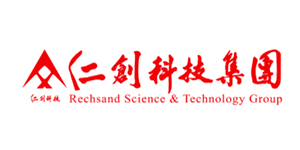
The performance of molding sand is heavily influenced by its physical properties, which include grain size, shape, and distribution. A well-graded sand mixture is critical for ensuring optimal flowability and compaction, which directly affects mold strength.
1. Grain Size and Shape The size of the sand grains influences the surface finish of the cast product. Finer grains lead to smoother surfaces, while coarser grains facilitate easier flow of molten metal. Ideally, a mixture of different grain sizes is used to balance strength and surface detail.
2. Moisture Content The moisture level in molding sand is another critical factor. Too much moisture can lead to expansion during the pouring of metal, causing defects such as “blowholes.” Conversely, insufficient moisture can result in poor moldability and weak molds.
3. Strength The bonding effectiveness of the clay and the density of the sand mix contribute to the overall strength of the mold. High-strength molds can withstand the pressure of molten metal without breaking or deforming.
Environmental Considerations
In recent years, there has been a growing focus on the environmental impact of molding materials in the foundry industry. Traditional molding sands often contain harmful substances, such as phenolic resins and heavy metals. The shift towards more sustainable practices includes the use of synthetic sands or recycled materials, which help in reducing waste and minimizing environmental footprint.
Conclusion
Foundry molding sand is an indispensable component of the casting process, significantly impacting the quality and efficiency of metal casting. As technologies and materials evolve, the foundry industry continues to explore innovative types of molding sands that enhance sustainability and performance. Knowledge of the composition, physical properties, and environmental implications of molding sands will enable foundries to optimize their processes, ultimately leading to superior cast products that meet the demands of an ever-evolving industrial landscape. Investing in research and development in this area is vital for maintaining competitiveness and fulfilling the stringent quality standards expected in modern manufacturing scenarios.
Post time:Kas . 12, 2024 11:40
Next:sand casting steel