3D Printing for Sand Casting Revolutionizing the Foundry Industry
In recent years, 3D printing technology has made significant strides, and its applications have expanded into various fields, including aerospace, automotive, and even healthcare. One of the most exciting developments is the use of 3D printing in sand casting, a traditional manufacturing process used to create complex metal parts. This article explores how 3D printing is revolutionizing sand casting, enhancing precision, reducing costs, and streamlining production.
The Basics of Sand Casting
Sand casting is one of the oldest methods of metal casting, dating back thousands of years. It involves creating a mold out of sand and then pouring molten metal into that mold to produce the desired shape. The process typically includes creating patterns—replicas of the final product—often made from wood or metal. These patterns are used to create impressions in the sand, forming the cavity into which the metal will be poured.
The Integration of 3D Printing
Traditionally, producing patterns for sand casting is time-consuming and labor-intensive. However, the integration of 3D printing technology has changed the game. 3D printers can quickly and accurately create complex patterns from digital models. This not only speeds up the design and production process but also reduces the margin for human error. Advanced 3D printing techniques can produce intricate designs that would be nearly impossible to create with traditional methods.
Enhanced Precision and Quality
One of the primary benefits of using 3D printing in sand casting is the enhanced precision it offers. With traditional methods, slight inaccuracies in the pattern can lead to significant defects in the final product. Conversely, 3D printing allows for high-detail models that ensure precise fit and function of the casted metal parts. This precision is especially crucial in industries such as aerospace and automotive, where even minuscule defects can have dire consequences.
Cost-Effectiveness
3d printing for sand casting
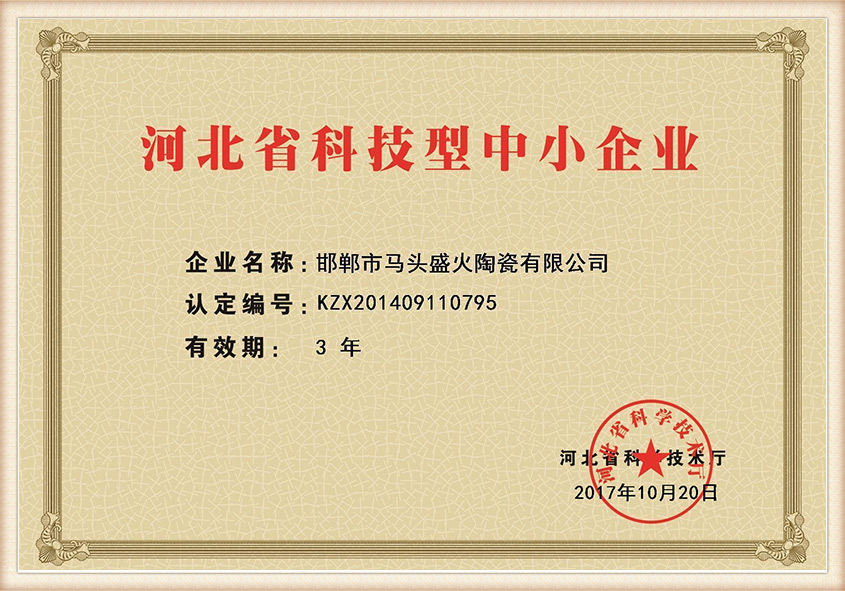
While the initial investment in 3D printing technology can be substantial, the long-term cost savings are undeniable. By reducing the time needed for pattern production and minimizing material waste, companies can see significant reductions in overall production costs. Furthermore, 3D printing eliminates the need for costly tooling, which is typically required in traditional sand casting methods. This aspect is particularly advantageous for small to medium-sized foundries looking to produce low-volume, high-variation parts.
Flexibility and Design Freedom
3D printing also offers unparalleled design freedom. Engineers and designers can experiment with complex geometries that were previously infeasible using traditional methods. This freedom leads to innovative product designs that can optimize performance and functionality. Companies are now able to produce lighter, stronger parts that meet specific design requirements thanks to the possibilities offered by 3D printing.
Environmental Considerations
As the world increasingly focuses on sustainability, 3D printing in sand casting presents an environmentally friendly alternative. The technology significantly reduces material waste since it only uses the sand needed to create the mold. Furthermore, the ability to produce parts on-demand means that excess inventory is minimized, contributing to a more efficient manufacturing process.
A Bright Future Ahead
The combination of 3D printing and sand casting represents a significant shift in the manufacturing landscape. As technology continues to advance, it is expected that the adoption of 3D printing will only increase, leading to further innovations within the foundry industry. This will not only enhance production capabilities but also elevate the quality and sustainability of metal parts across various sectors.
In conclusion, the integration of 3D printing in sand casting is transforming how manufacturers design and produce components. With benefits ranging from increased precision and cost savings to design flexibility and environmental sustainability, this technology is set to revolutionize the foundry industry, paving the way for more efficient and innovative manufacturing practices. As we move forward, embracing these advancements will be crucial for businesses looking to stay competitive in an ever-evolving marketplace.
Post time:Ara . 26, 2024 09:46
Next:Innovative Techniques in Large Sand Casting for Enhanced Manufacturing Efficiency