The Role of Sand in Metal Casting A Comprehensive Overview
Metal casting is a vital process in manufacturing that involves pouring molten metal into a mold to create various components. Among the different materials used in this process, sand has earned a prominent place due to its unique properties and versatility. This article explores the significance of sand in metal casting, the types of sands used, and the advantages it offers in producing high-quality castings.
Importance of Sand in Metal Casting
Sand has been a fundamental material in the metal casting industry for centuries. Its primary role is to form molds into which molten metal is poured. The success of the casting process largely depends on the characteristics of the sand used, including its grain size, shape, and permeability. These properties affect the mold's ability to withstand high temperatures and resist deformation under the pressure of the molten metal.
Types of Sand Used in Metal Casting
1. Green Sand This is the most commonly used sand in the metal casting process. It is a mixture of sand, clay, water, and other additives. Green sand molds are molded while wet, allowing for immediate use in casting. The presence of clay provides binder properties, which hold the sand grains together and help maintain the mold shape during casting. One of the key advantages of green sand is its recyclability—after use, it can be reclaimed and reused, making it cost-effective.
2. Synthetic Sand Often referred to as engineered sand, synthetic sand is composed of a mix of silica sand, resin, and other binding agents. This type of sand offers improved control over mold properties and can enhance casting surface finish and dimensional accuracy. The use of synthetic sand is particularly favored in industries requiring high-precision castings, such as aerospace and automotive.
3. Chromite Sand Known for its sand strength and heat-resistance properties, chromite sand is derived from the mineral chromite. It is primarily used in the production of molds for iron castings, especially when dealing with high melting-point alloys. Chromite sand helps in reducing oxidation during the casting process, which is crucial for maintaining the integrity and quality of the final product.
4. Zircon Sand This high-performance sand has exceptional thermal stability and is often used for casting high-temperature metals. Zircon sand molds can withstand intense heat without deforming, making it ideal for applications in aerospace and heavy machinery.
sand for metal casting
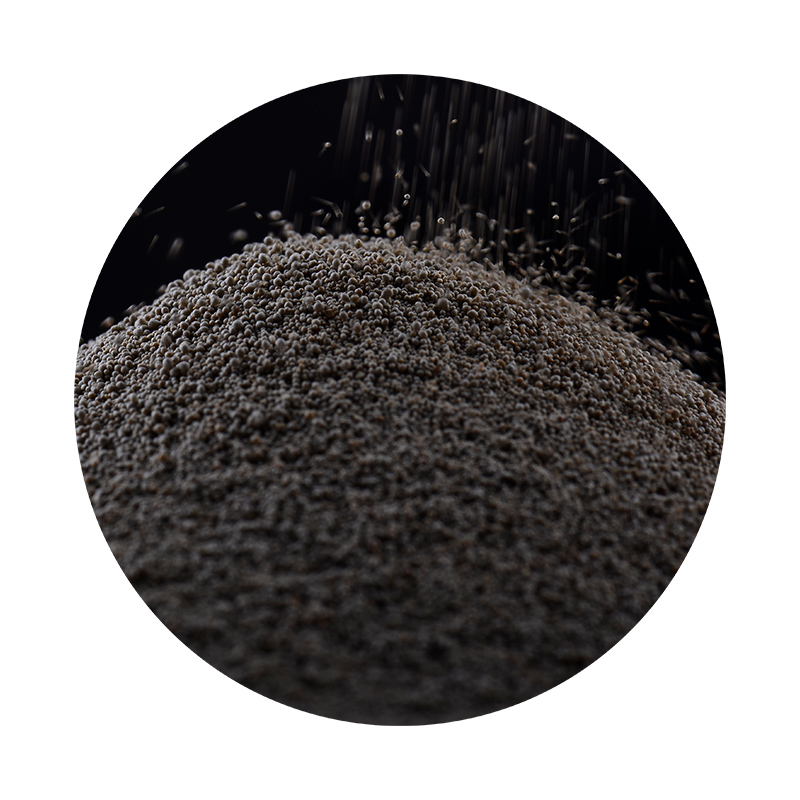
Advantages of Using Sand in Metal Casting
The use of sand in metal casting offers several benefits that contribute to the overall efficiency and quality of the casting process.
1. Cost-Effective Sand is relatively inexpensive compared to other molding materials. Since many types of sand can be easily reclaimed and reused, the production costs of sand molds are kept low.
2. Flexibility in Design Sand molds can be crafted into complex shapes and designs, providing manufacturers the flexibility needed for producing intricate components. This adaptability makes sand casting suitable for a wide range of industries.
3. Thermal Properties Sand has excellent thermal conductivity, allowing heat to be evenly distributed in the mold during casting. This helps prevent defects such as warping or cracks in the final product.
4. Environmental Impact Many sand types, especially green sand, are environmentally friendly. The ability to recycle sand reduces waste, and the process can be managed with minimal environmental impact when compared to other materials.
Conclusion
The use of sand in metal casting is indispensable due to its unique properties and advantages. From green sand to synthetic and specialty sands like chromite and zircon, each type offers different benefits that cater to diverse casting needs. As industries continue to evolve, the role of sand in metal casting will remain fundamental, ensuring that manufacturers can produce high-quality, cost-effective castings for a wide range of applications. The continued exploration and innovation in molding sands will likely lead to even more efficient and environmentally sustainable casting processes in the future.
Post time:Nov . 07, 2024 08:01
Next:Examining the Growth and Innovation in Sand Casting Industries Today