The Role of Sand in Sand Casting An Overview
Sand casting, a process that dates back thousands of years, remains one of the most widely used methods for producing metal parts across various industries. Central to this process is the material itself — sand. Understanding the types of sand used in sand casting, their properties, and the reasons for their extensive use sheds light on the importance of this versatile material in manufacturing.
Types of Sand Used in Sand Casting
The most commonly used sand for sand casting is silica sand, primarily composed of silicon dioxide (SiO2). This type of sand is favored due to its high melting point and thermal stability, making it suitable for casting in high-temperature environments. Silica sand is typically processed to achieve the desired grain size and cleanliness, ensuring that it can effectively form molds without introducing impurities that can affect the final product's quality.
Another type of sand used is olivine sand, which is a magnesium iron silicate. Olivine sand has a higher melting point than silica sand and is less prone to expansion during heating, making it less likely to deform under the stresses of the casting process. This quality can improve the accuracy of the final cast part. However, olivine sand is often more expensive than silica sand, which can limit its use in some applications.
Properties of Sand in Casting
The properties of sand are critical to the success of the casting process. Some key characteristics include grain size, shape, and distribution. The ideal sand should have a fine, consistent grain size that facilitates good compaction while also allowing for easy removal of the cast part after solidification. Rounded grains, as opposed to angular ones, are often preferred since they pack better and create molds with fewer defects.
Another important property is the sand's ability to hold moisture. Ideally, sand should contain a specific amount of water, which helps bind the grains together when forming a mold. This moisture content can vary based on environmental conditions and the specific requirements of the casting, but maintaining the correct mixture is crucial to producing molds that are sufficiently strong and stable during the casting process.
sand used for sand casting
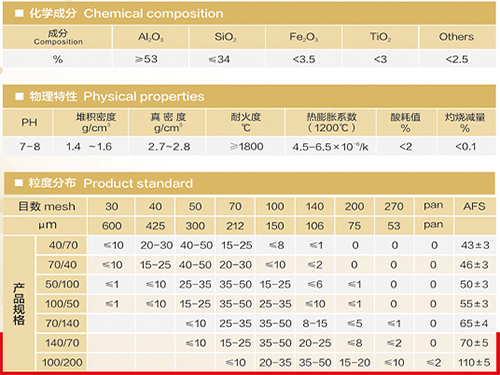
The Advantages of Using Sand in Casting
One of the primary advantages of using sand in casting is its cost-effectiveness. Silica sand, in particular, is relatively inexpensive and abundant, making it accessible for high-volume production. Additionally, the sand casting process allows for both small and large production runs, giving manufacturers flexibility in meeting varying demand levels.
Sand molds can be easily modified, allowing for significant design flexibility. Complex shapes can be created without the need for expensive tooling typically associated with processes like die casting. Moreover, sand casting is especially advantageous for producing large components, which may be difficult to manufacture using other methods.
Environmental Considerations
As industries become increasingly aware of their environmental impact, the sustainability of materials used in manufacturing processes is a growing concern. The sand used in casting can be recycled several times, reducing the need for virgin materials and minimizing waste. After casting, used sand can be reclaimed, processed, and reused in new molds, significantly decreasing the overall environmental footprint of the casting operation.
Conclusion
In conclusion, sand plays a pivotal role in the sand casting process due to its unique properties, versatility, and economic advantages. Whether it is silica sand or olivine sand, the choice of material directly influences the quality and performance of the final castings. As technological advancements continue to evolve in the casting industry, the critical use of sand will likely remain at the forefront, ensuring its relevance in the manufacturing landscape for years to come. Understanding the intricacies of different types of sand and their applications not only underscores the material's importance but also helps manufacturers optimize their processes for better efficiency and sustainability.
Post time:Nov . 07, 2024 20:17
Next:Exploring the Benefits and Uses of Foundry Casting Sand in Metalworking