Sand Casting Mass Production A Comprehensive Overview
Sand casting, a time-honored manufacturing process, plays a pivotal role in the mass production of various metal parts. This technique involves creating a mold from a sand mixture, which is then used to cast metal components by pouring molten metal into the mold cavity. Due to its versatility, cost-effectiveness, and ability to produce complex geometries, sand casting is extensively utilized across various industries, including automotive, aerospace, and machinery.
The Sand Casting Process
The sand casting process begins with the preparation of the mold. Typically, a mixture of silica sand, clay, and water is used to create the mold. The sand's particulate nature allows it to capture intricate details while remaining easy to shape. The mold consists of two halves the cope (top) and the drag (bottom). Once the mold halves are formed, they are clamped together, and a pouring cup and sprue are created to facilitate the flow of molten metal.
The next step involves melting the metal to be cast. Common metals used in sand casting include aluminum, steel, iron, and bronze. Once melted, the molten metal is poured into the mold through the pouring cup and allowed to fill the cavity. The metal then cools and solidifies, taking the shape of the mold.
After cooling, the mold is taken apart to reveal the cast part. The removal process may involve shaking out the sand or using mechanical means to dismantle the mold. Once the casting is extracted, it typically requires some finishing operations, such as grinding, machining, or surface treatment, to achieve the desired specifications.
Advantages of Sand Casting for Mass Production
1. Cost-Effectiveness Sand casting is one of the most economical methods for mass production, especially for small to medium-sized runs. The raw materials, primarily sand, are inexpensive, and the process requires minimal tooling, resulting in lower overall production costs.
2. Versatility This technique can be used to produce a wide range of metal components with varying sizes and complexities. From small intricate parts to large industrial components, sand casting can accommodate diverse design needs.
sand casting mass production
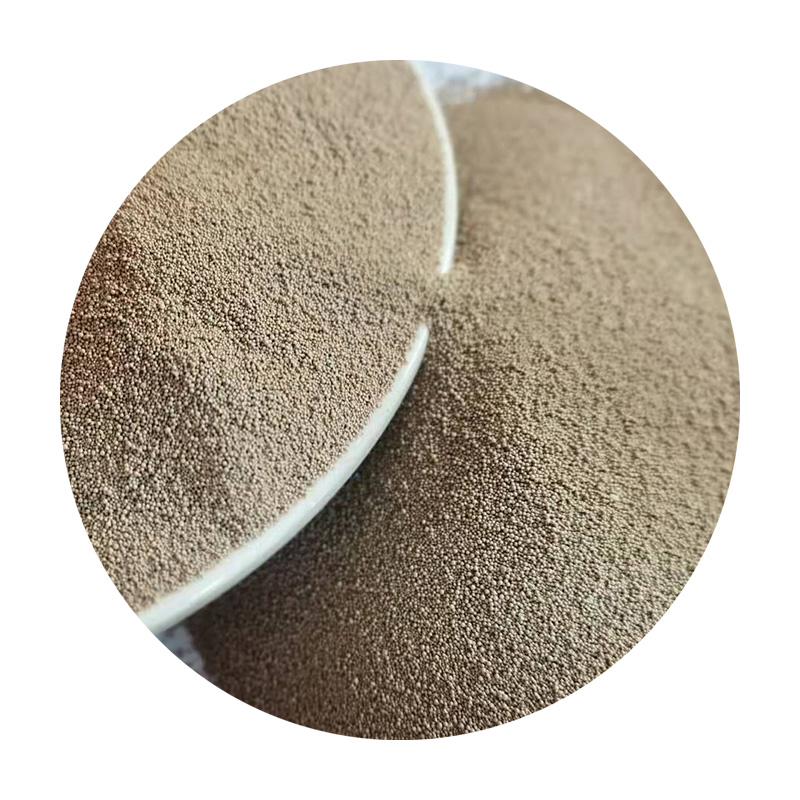
3. Complex Geometries Thanks to the flexibility of sand molds, manufacturers can produce intricate shapes and details that would be challenging with other manufacturing processes. This capability is particularly beneficial when designing components with internal passages or complex outlines.
4. Rapid Prototyping Sand casting is an excellent option for rapid prototyping. Designers can create and iterate on designs more quickly, testing different geometries without incurring significant costs.
5. Scalability The sand casting process can be scaled to meet the demands of mass production. As production volumes increase, manufacturers can optimize molds and automate certain aspects of the process to improve efficiency.
Challenges in Sand Casting Mass Production
Despite its many advantages, sand casting does come with certain challenges. One of the primary issues is the quality of the final product, which can be affected by variables such as mold preparation, metal pouring techniques, and cooling rates. Defects such as porosity, shrinkage, or surface imperfections can arise if these factors are not meticulously controlled.
Additionally, while sand casting is suitable for many applications, it may not be the optimal choice for all products, particularly those requiring high precision and surface finish. In such cases, alternative methods like investment casting or die casting may be more appropriate, albeit at a higher cost.
Conclusion
In summary, sand casting remains a vital method in the landscape of mass production due to its cost-effectiveness, versatility, and ability to create complex geometries. While challenges exist, advances in technology and process optimization continue to enhance the quality and efficiency of sand casting. As industries evolve and the demand for customized components grows, sand casting will likely maintain its relevance, adapting to meet the needs of modern manufacturing. Whether used for prototyping or large-scale production, sand casting proves to be a resilient and essential technique in today's manufacturing world.
Post time:Dec . 03, 2024 18:45
Next:Current Market Trends for Foundry Sand Pricing and Influencing Factors