The Importance of Sand in Sand Casting
Sand casting is one of the oldest and most versatile metal casting processes, widely used in the manufacturing industry for producing a range of complex shapes. At the heart of this process lies the material that not only defines its effectiveness but also dictates the quality of the finished products sand.
Composition and Types of Sand
The most commonly used sand in sand casting is silica sand, primarily composed of silicon dioxide. Its high melting point and excellent thermal properties make it suitable for withstanding the extreme temperatures encountered during the casting process. There are various types of sands utilized in sand casting, including green sand, dry sand, and loam sand, each having distinct characteristics and applications. Green sand, for instance, is a mixture of silica sand, clay, and water, which gives it a unique ability to retain moisture. This type of sand is advantageous for its excellent cohesiveness and ability to form intricate shapes without the use of binding agents.
The Molding Process
The sand used in sand casting acts as a mold material. The process begins by creating a pattern, often made from metals or plastics, which is then pressed into the sand to create a cavity that mimics the desired shape of the final product. The flexibility of sand allows for easy removal of the pattern, making it ideal for both one-off and mass production. Once the patterns are set, molten metal is poured into the cavity. The sand molds can handle high thermal loads, preventing deformation and ensuring that the molten metal solidifies into the intended shape.
sand casting sand
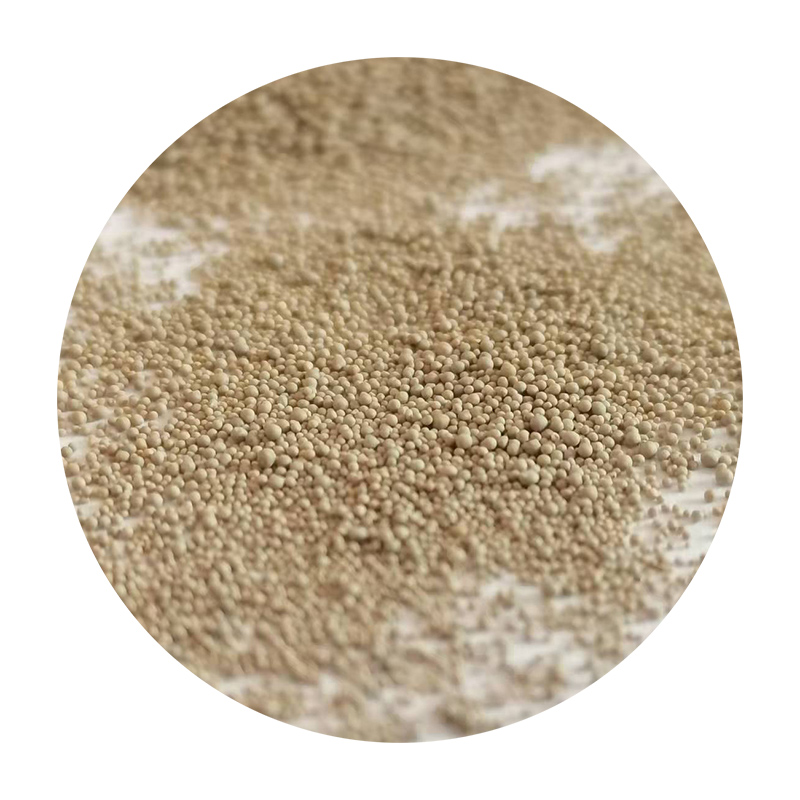
Benefits of Sand Casting
One of the main advantages of sand casting is its cost-effectiveness. The raw materials are relatively inexpensive, and the sand can be reused several times, significantly reducing waste. Moreover, the process accommodates a wide range of metals, including aluminum, iron, and bronze, catering to various industries such as automotive, aerospace, and art.
Challenges and Innovations
However, there are challenges associated with sand casting, such as the potential for sand inclusion and surface finish issues. Innovations in technology and materials have led to advancements that address these concerns. For example, the introduction of synthetic sands and advanced molding techniques has improved the strength and accuracy of castings, allowing for tighter tolerances and better surface finishes.
Conclusion
In conclusion, sand is not merely a component in the sand casting process; it is a pivotal element that influences the overall efficiency and effectiveness of metal casting. As industries continue to evolve, the significance of sand and its various types will remain central to the innovation and development of casting techniques, ensuring that sand casting remains a vital part of modern manufacturing.
Post time:Sep . 14, 2024 11:01
Next:what materials are used in sand casting