The Importance of Resin-Coated Sand Plants in Modern Casting
In the world of manufacturing, particularly in the foundry industry, the process of casting is paramount. This traditional method allows for the creation of complex metal components by pouring molten metal into shaped molds. As industries demand higher precision and improved performance from casted products, resin-coated sand has emerged as a superior alternative to conventional molding sands. At the heart of this innovation are resin-coated sand plants, which play a critical role in modern casting technology.
What is Resin-Coated Sand?
Resin-coated sand consists of standard foundry sand that has been coated with a resin mixture, typically phenolic or furan resin. This process enhances the sand's properties, significantly improving its ability to withstand high temperatures and reduce gas defects in castings. Unlike traditional green sand, which uses water and clay as a binder, resin-coated sand provides better mold strength, surface finish, and dimensional accuracy.
The Process of Resin Coating
The resin coating process involves several steps. Initially, clean silica sand is heated to remove any moisture. Then, it is mixed with pre-catalyzed resin and hardeners in a controlled environment. This mixture is subjected to a precise temperature and time schedule to ensure optimal coating. The result is a uniform distribution of resin on each sand grain, which enables the sand to form robust molds and cores.
Resin-coated sand plants are equipped with advanced machinery that automates this process, ensuring consistency and quality. The facilities often employ modern technology to monitor temperature, humidity, and mixing ratios, allowing for fine-tuning of the resin's properties based on customer specifications.
Advantages of Resin-Coated Sand
The use of resin-coated sand offers several benefits that have made it a preferred choice in the foundry industry
resin coated sand plant
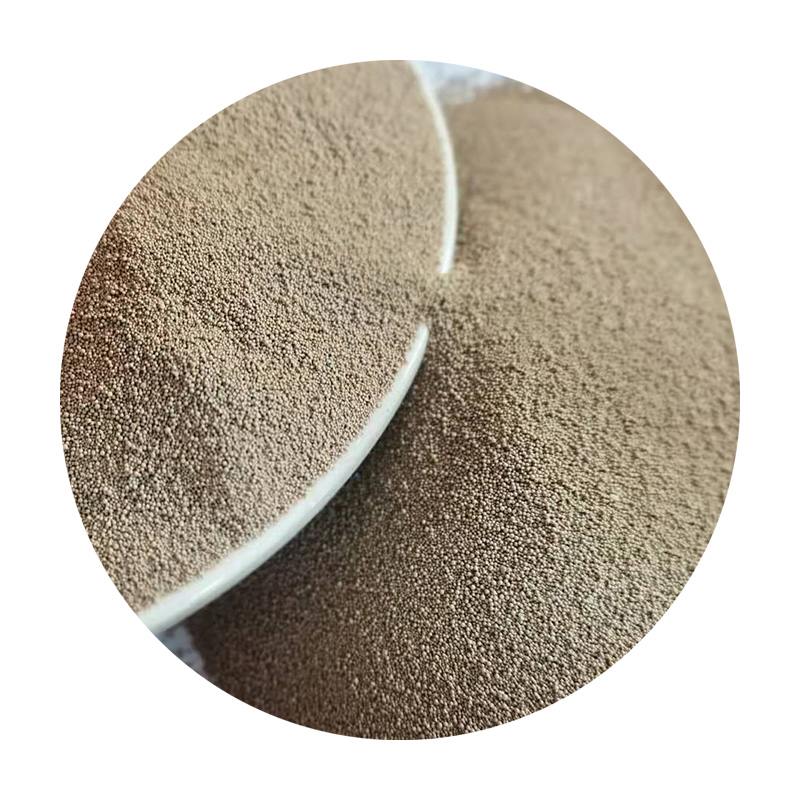
2. Superior Surface Finish Castings made with resin-coated sand exhibit smoother surfaces, reducing the need for additional machining and finishing processes, and thereby lowering production costs.
3. Reduced Gas Defects The heat-resistance properties of resin help minimize gas generation during pouring, leading to fewer casting defects, such as pinholes and blowholes.
4. Flexibility in Design Resin-coated sand can be molded into intricate shapes, enabling manufacturers to produce complex components with high precision.
5. Environmental Considerations Many modern resin systems are designed to reduce harmful emissions during the curing process, making resin-coated sand plants more environmentally friendly compared to traditional foundry operations.
Applications in Various Industries
Resin-coated sand finds applications across various sectors, including automotive, aerospace, and general engineering. In the automotive industry, components like engine blocks and transmission cases benefit from the high strength and precision that resin-coated sand provides. The aerospace sector relies on this technology for producing critical parts that must meet stringent quality and performance standards.
Conclusion
The resin-coated sand plant is integral to the evolution of casting technology, addressing the industry's increasing demands for higher quality and efficiency. By delivering superior molds and cores, these plants enable manufacturers to produce complex metal components with unmatched quality and performance. As technology continues to evolve, resin-coated sand is poised to play an even more significant role in the foundry industry, driving innovations that meet the needs of modern manufacturing. This shift not only enhances production capabilities but also supports the broader trend towards sustainability and reduced environmental impact in the manufacturing processes.
Post time:Dec . 09, 2024 14:36
Next:sand casting 101