Resin Coated Sand Enhancing Foundry Operations
In the foundry industry, the casting process plays a vital role in manufacturing components across various sectors, including automotive, aerospace, and machinery. One of the significant advancements in foundry technology is the use of resin coated sand, which has transformed traditional sand casting methods. This article explores the characteristics, benefits, and applications of resin coated sand, shedding light on its crucial role in enhancing foundry operations.
Resin coated sand consists of high-quality silica sand coated with a thermosetting resin, typically phenolic or epoxy-based. The incorporation of resin lends the sand its unique properties, making it an excellent choice for creating molds and cores. During the molding process, the resin-coated sand is typically mixed with a curing agent, which initiates a chemical reaction that hardens the mold. This process significantly improves the mold's durability and dimensional accuracy compared to conventional sand molds.
One of the most notable benefits of using resin coated sand is its ability to produce intricate and complex shapes with superior surface finish. The fine grain structure of the sand allows for better detail reproduction, essential for manufacturing components with tight tolerances. Additionally, the smooth surface finish reduces the need for extensive machining, saving both time and costs in the production process.
Another advantage of resin coated sand is its enhanced strength and stability. The resin binding ensures that the sand does not break down easily during the casting process, which can lead to defects in the final product. This stability allows foundries to create larger molds and cores without the fear of collapse or deformation, thus expanding the design possibilities for parts and components.
resin coated sand
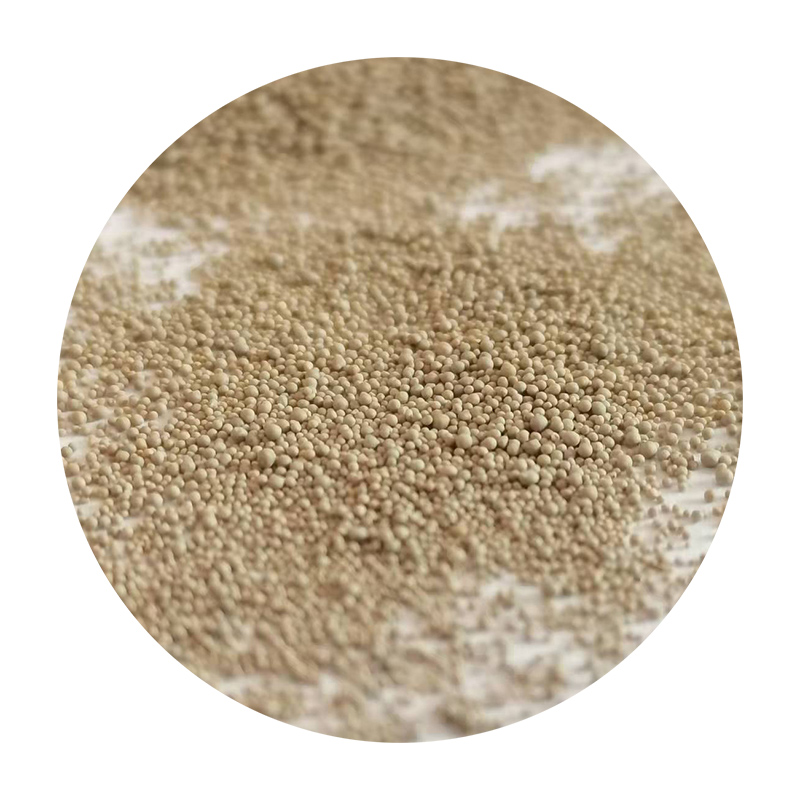
Moreover, resin coated sand exhibits excellent thermal properties, withstanding high temperatures during the casting process without losing its structural integrity
. This ability is particularly valuable in the foundry industry, where molten metal can reach temperatures exceeding 1,500 degrees Fahrenheit (800 degrees Celsius). The thermal stability of resin coated sand ensures that it can handle the intense heat associated with metal casting, which leads to improved casting quality and reduced scrap rates.Environmental considerations are also becoming increasingly important in modern manufacturing practices, and resin coated sand addresses several of these concerns. Traditional sand casting methods often involve additives that can be harmful to the environment. In contrast, many modern resin systems are formulated to be more eco-friendly, reducing emissions and limiting hazardous waste production. Additionally, the longevity of resin coated sand molds means that fewer resources are spent on producing new materials, contributing to a more sustainable casting process.
The versatility of resin coated sand makes it suitable for various applications beyond traditional foundry operations. This material is increasingly utilized in sectors such as oil and gas exploration, where sand is used in hydraulic fracturing processes. The robustness and reliability of resin coated sand make it an ideal choice for demanding applications that require high performance under extreme conditions.
Despite its numerous benefits, the adoption of resin coated sand may require initial investments in equipment and training. Foundries need to adapt their processes to accommodate this advanced material, which may pose a barrier for some businesses. However, the long-term advantages, including enhanced productivity, reduced waste, and improved product quality, often outweigh these initial challenges.
In conclusion, resin coated sand represents a significant advancement in foundry technology, offering a range of benefits that enhance the casting process. Its ability to produce intricate designs, reduce scrap rates, and improve surface finishes makes it a preferred choice for modern casting applications. As the industry continues to prioritize sustainability and efficiency, resin coated sand is likely to play an increasingly important role in shaping the future of foundry operations. By leveraging the advantages of this innovative material, foundries can achieve higher productivity levels and maintain a competitive edge in the market.
Post time:Nov . 08, 2024 22:00
Next:describe sand casting